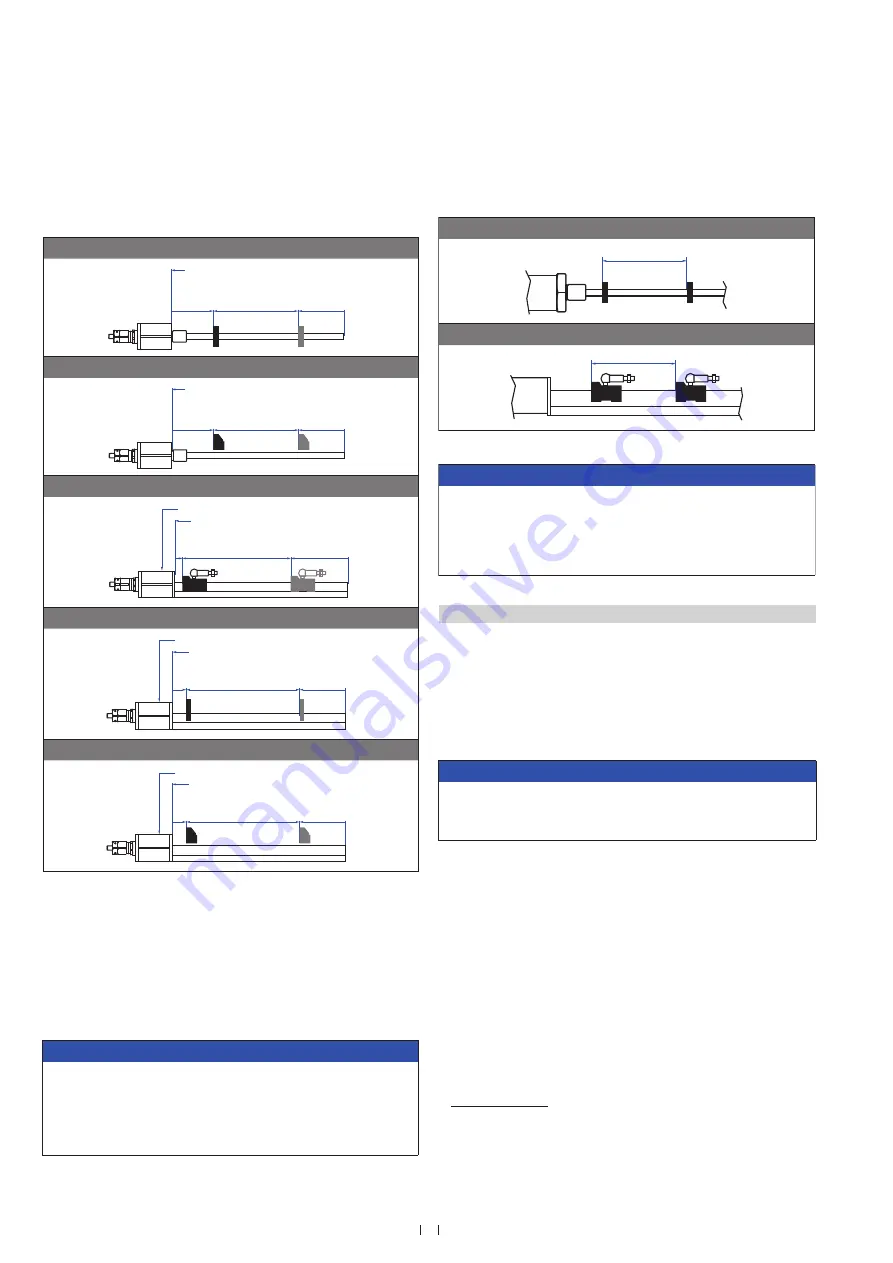
12
Temposonics
®
ET Analog ATEX / IECEx / CEC / NEC / CCC Certified
Operation Manual
Start and end positions of the position magnets
Consider the start and end positions of the position magnets during
the installation. To ensure that the entire stroke length is electrically
usable, the position magnet must be mechanically mounted as follows.
NOTICE
On all sensors, the areas left and right of the active stroke length are
provided for null and dead zone (see “4.2 Styles and installation of
Temposonics
ET (rod sensor)” on page 8). These zones should
not be used for measurement, however the active stroke length can
be exceeded.
Controlling design dimensions are in millimeters and measurements in ( ) are in inches
Fig. 17: Start and end positions of magnets
4.5 Electrical connection
Placement of installation and cabling have decisive influence on the
sensor‘s electromagnetic compatibility (EMC). Hence correct
installation of this active electronic system and the EMC of the entire
system must be ensured by using suitable metal connectors, shielded
cables and grounding. Overvoltages or faulty connections can damage
the sensor electronics despite protection against wrong polarity.
NOTICE
1. Do not mount the sensors in the area of strong magnetic or
electric noise fields.
2. Never connect / disconnect the sensor when voltage is applied.
Multi-position measurement
The minimum distance between the magnets is 75 mm (3 in.)
(used with all types of magnets).
Instruction for connection
• Connect the shield to ground externally via the controller equipment.
• Keep control and signal leads separate from power cables and
sufficiently far away from motor cables, frequency inverters, valve
lines, relays, etc..
• Use only connectors with metal housing, if you use a connector.
Connect the shielding to the connector housing.
• Keep all non-shielded leads as short as possible.
• Keep the earth connection as short as possible with a large cross
section. Avoid ground loops.
• With potential differences between machine and electronics
earth connections, no compensating currents are allowed to
flow across the cable shielding.
Recommendation:
Install potential compensating leads with large cross section.
• Use only stabilized power supplies in compliance with the specified
electrical ratings.
Fig. 18: Examples: Minimum distance for multi-position measurement
ET-F/-W/-M/-S with ring magnet / U-magnet
≥ 75
ET-P with magnet slider
≥ 75
NOTICE
For multi-position measurement, use magnets of the same type
e.g. 2 × U-magnet (part no. 251 416-2).
Do not underscore the minimum distance between the magnets of
75 mm (3 in.) for multi-position measurement. Contact MTS Sensors
if you need a magnet distance < 75 mm (3 in.).
ET-F/-W/-M/-S with ring magnet & U-magnet
Reference edge of mounting
Start position
51 (2)
End position
63.5 (2.5)
Active
measuring range
ET-F/-W/-M/-S with block magnet
Reference edge of mounting
Start position
48.5 (1.91)
End position
66 (2.6)
Active
measuring range
ET-P with magnet slider “S”, “N”, “V”, “G”
Reference edge of mounting
Sensor electronics housing
End position
82 (3.23)
Start position
12 (0.47)
Active
measuring range
ET-P with U-magnet
Reference edge of mounting
Sensor electronics housing
End position
66 (2.6)
Start position
28 (1.1)
Active
measuring range
ET-P with block magnet
Reference edge of mounting
Sensor electronics housing
End position
68.5 (2.7)
Start position
25.5 (1)
Active
measuring range
Содержание Temposonics E Series
Страница 32: ......