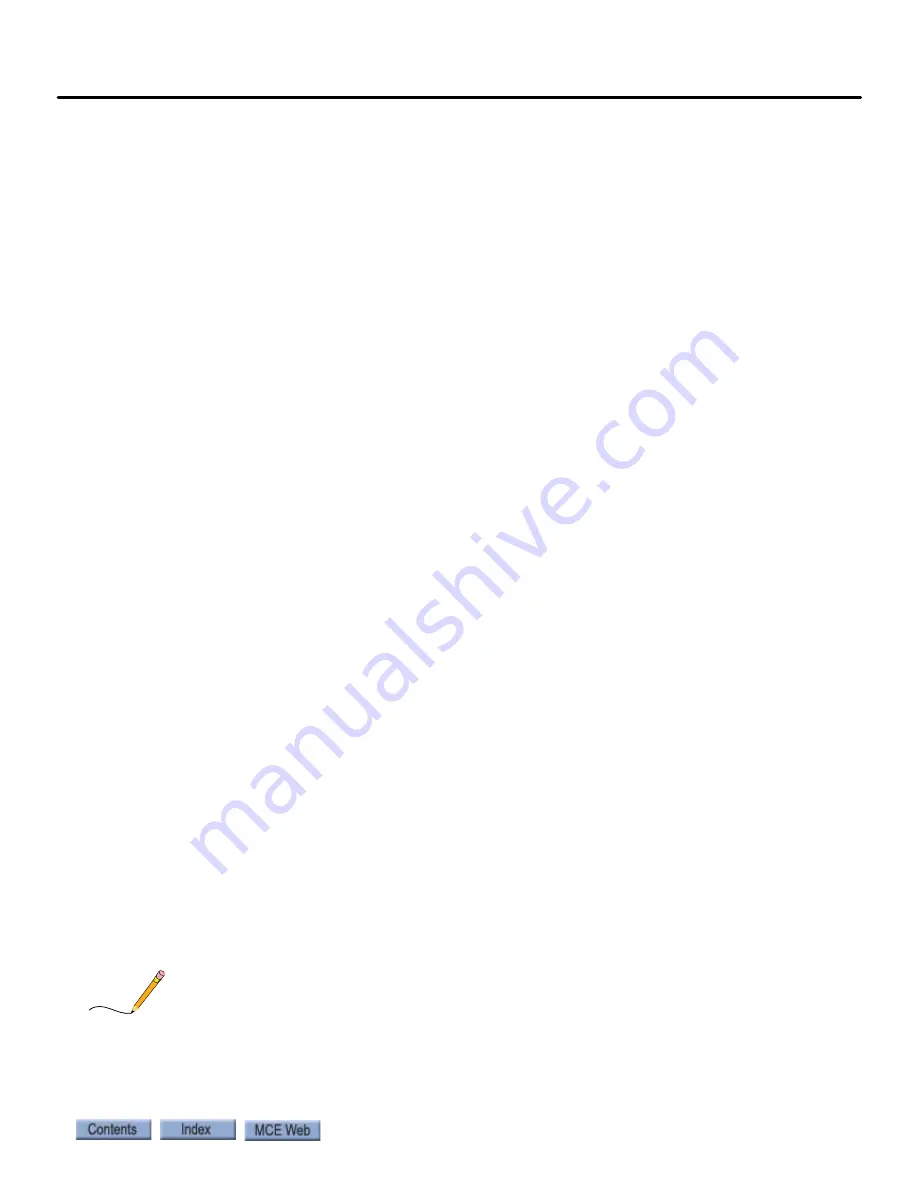
System Features
1-3
1
Motion 4000
System Features
Motion 4000 design incorporates:
• Solid state implementation of redundancy and proofing requirements, eliminating relays
whenever possible to improve service life and reliability.
• Retention of the simple LCD/keypad programming interface used on earlier MCE pro-
grammable controls but with the addition of a hand-held interface (
mPAC
) that can be
plugged in to any system CAN connector.
• Easy software updates — Internet download through a PC to the hand-held user interface,
MCE SD card, or EEPROM replacement.
• CAN Bus: Circuit boards and major components all communicate through light weight,
serial CAN Bus connections. Communication between major system components (i.e.,
controller to car, controller to hall calls, etc.) uses shielded, twisted-pair cables connected
to pluggable terminals (CAN).
• ASME A17.1/CSA B44 compliant throughout.
• Field connections: Field connections are handled by Universal I/O boards. The boards are
factory set to handle 24V, 48V, 110V, or 120V AC or DC inputs. This allows a single board
design to service all common inputs.
• Positioning: Permanently encoded magnetic tape, or steel tape positioning systems.
• Minimized hoistway peripherals: Motion 4000 design allows slowdown, emergency termi-
nal, and hoistway access limit switches to be eliminated. These switches exist as virtual
switches in system software.
• Serial hall call: Motion 4000 may use serial hall calls for easier field wiring. The riser drop
provides CAN communication and power to the fixtures. (Discrete hall call wiring is sup-
ported through Universal I/O boards.)
• Serial car panel option: Discrete signals from car panel buttons may be serialized for easy
connection to the controller via CAN bus through the cartop interface.
• Light weight traveler and hoistway cabling: Serial communication allows low traveler and
hoistway cable conductor counts.
• Optional monitoring capabilities using mView, iMonitor, and iReport software.
• Optional integration with Building Management Software using BMS-LINK.
• Optional Jail Services application for detention center operation.
• (MRL) Optional passenger rescue system provides input from a cartop mounted camera
and a rescue control panel with LCD display to allow a technician to safely drift the car to a
landing in the absence of commercial or emergency power. Once at the landing, doors
must be opened manually.
• Optional Traction Auxiliary Power Supply (TAPS) provides automated return of the car to
a landing and automated door opening in the absence of commercial power. Power is pro-
vided via an integrated UPS/battery system and requires no generator.
Note
If the job uses a TAPS system and a TorqMax/KEB F5 drive, drive parameter LF.61 must be set
to Di1.
Содержание Motion 4000
Страница 20: ...xiv Manual 42 02 2P24 5 20 13 ...
Страница 38: ...Motion 4000 Traction Elevator Control 1 18 Manual 42 02 2P24 ...
Страница 178: ...Final Adjustments 3 56 Manual 42 02 2P24 ...
Страница 322: ...User Interface 4 144 Manual 42 02 2P24 ...
Страница 391: ...PC Board Quick References 5 69 5 Motion 4000 Figure 5 11 Example MC CPI Wiring ...
Страница 439: ...Customer Notations A 27 A Motion 4000 Customer Notations Table A 4 Customer Notation Area ...
Страница 444: ...Appendix A 32 Manual 42 02 2P24 ...