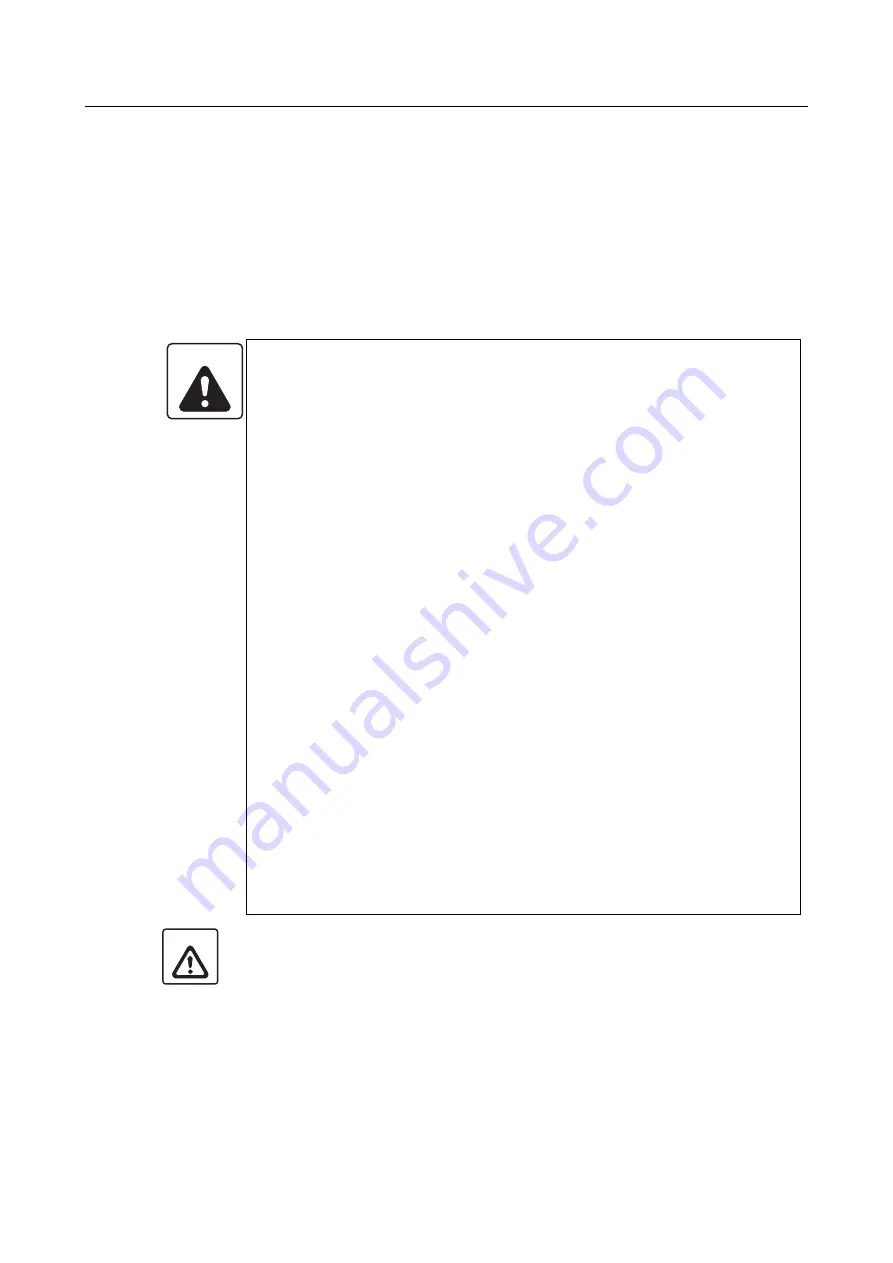
CHUCKING C-9
3
SHAPING SOFT JAWS FOR FINISHING
This section describes the cautions to be observed when shaping the soft jaws and the procedure
used for shaping the soft jaws for external and internal gripping.
3-1
Cautions on Shaping the Soft Jaws
When shaping soft jaws, pay attention to the following points.
1.
Never subject the chuck, chuck jaws, or workpiece to shock by tapping them with
a hammer, etc., since this will adversely affect accuracy and functions and reduce
the chuck service life.
2.
Choose the machining conditions with particular care when shaping soft jaws,
since this work involves intermittent machining. Inappropriate machining
conditions could damage the cutting tool or cause machining defects.
3.
When soft jaws are used, they must be made of a softer material than the
workpiece. If they are harder, the workpiece could be distorted or scratched.
WARNING
1.
Deburr soft jaws after shaping them. Switch off the power before
starting the deburring work. If you do not switch the power off the
machine could operate unexpectedly if someone carelessly
interferes with the machine controls, causing serious injuries or
damage to the machine.
2.
The T-nuts in the chuck must not protrude from the master jaw. If
they do the master jaw or T-nuts may be damaged, and machining
accuracy will be impaired. Breakage of the T-nuts or master jaw
while the spindle is rotating could cause accidents involving serious
injuries or damage to the machine.
3.
Mount soft jaws in the chuck in a well-balanced manner. Poor
balance will cause runout of the spindle and could cause the soft
jaws to fly out of, causing serious injuries or damage to the machine.
It will also adversely affect machining accuracy.
4.
Clamp workpieces at the center of the master jaws' stroke or within
their appropriate stroke range. If a workpiece is clamped in the
chuck with the jaws positioned near the stroke end it will not be
possible to clamp the workpiece securely and it may slip and fly out
of the chuck as a result of impact during cutting, causing serious
injuries or damage to the machine.
5.
Before shaping jaws, read the instruction manuals supplied by the
chuck manufacturer to determine the jaw shaping procedures
optimized for the chuck to be used, since the jaw shaping
procedures in this manual assume the use of a standard 3-jaw chuck
and may be inapplicable to the chuck actually used.
CAUTION