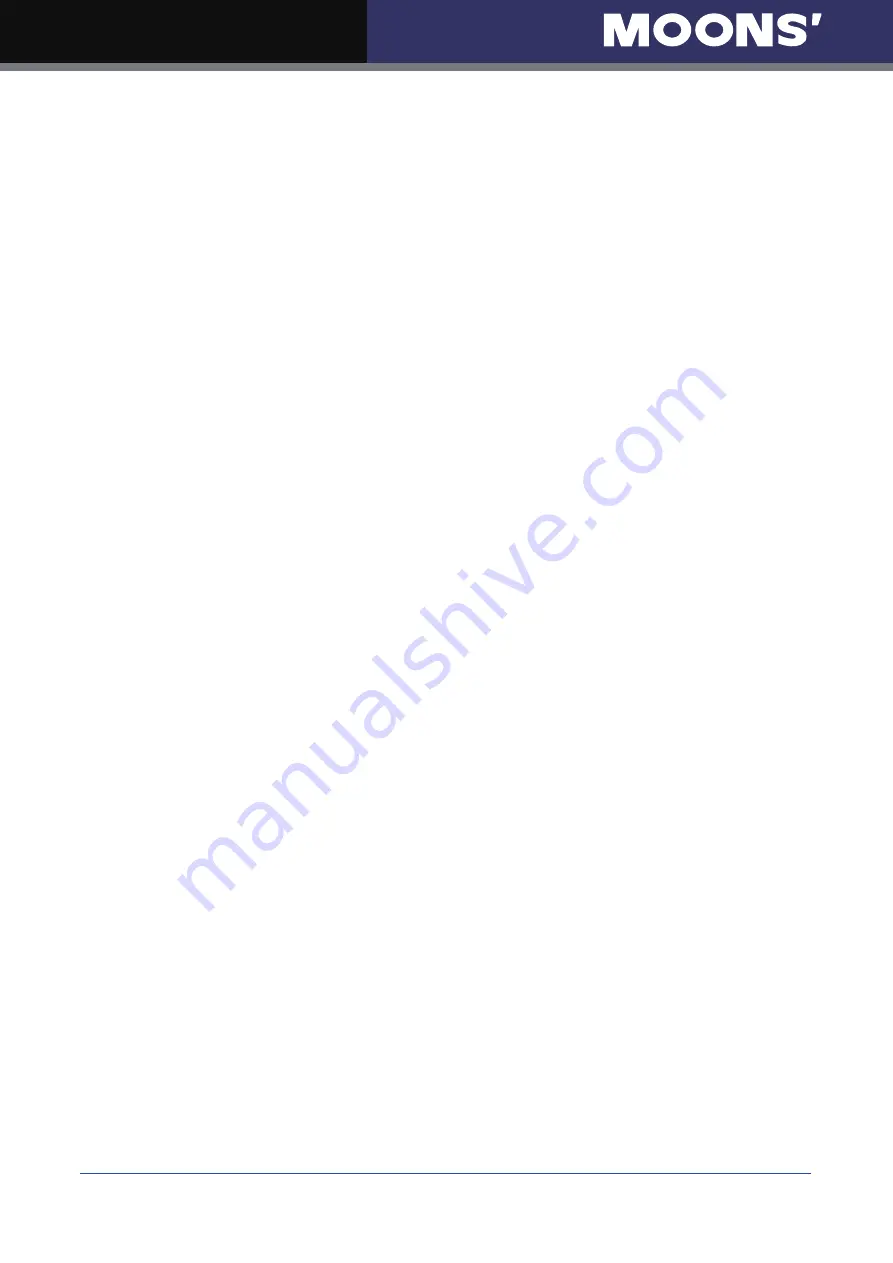
6
Rev. 1.0
8/26/2015
STM11 Hardware Manual
1.3 Safety Instructions
Only qualified personnel should transport, assemble, install, operate, or maintain this equipment.
Properly qualified personnel are persons who are familiar with the transport, assembly, installation,
operation, and maintenance of motors, and who meet the appropriate qualifications for their jobs.
To minimize the risk of potential safety problems, all applicable local and national codes regulating
the installation and operation of equipment should be followed. These codes may vary from area
to area and it is the responsibility of the operating personnel to determine which codes should be
followed, and to verify that the equipment, installation, and operation are in compliance with the
latest revision of these codes.
Equipment damage or serious injury to personnel can result from the failure to follow all applicable
codes and standards. MOONS’ does not guarantee the products described in this publication
are suitable for a particular application, nor do they assume any responsibility for product design,
installation, or operation.
Read all available documentation before assembly and operation. Incorrect handling of the
products referenced in this manual can result in injury and damage to persons and machinery. All
technical information concerning the installation requirements must be strictly adhered to.
It is vital to ensure that all system components are connected to earth ground. Electrical safety is
impossible without a low-resistance earth connection.
This product contains electrostatically sensitive components that can be damaged by incorrect
handling. Follow qualified anti-static procedures before touching the product.
During operation keep all covers and cabinet doors shut to avoid any hazards that could possibly
cause severe damage to the product or personal health.
During operation the product may have components that are live or have hot surfaces.
Never plug in or unplug the Integrated Motor while the system is live. The possibility of electric
arcing can cause damage.
Be alert to the potential for personal injury. Follow recommended precautions and safe operating
practices emphasized with alert symbols. Safety notices in this manual provide important
information. Read and be familiar with these instructions before attempting installation, operation,
or maintenance. The purpose of this section is to alert users to the possible safety hazards
associated with this equipment and the precautions necessary to reduce the risk of personal injury
and damage to equipment. Failure to observe these precautions could result in serious bodily
injury, damage to the equipment, or operational difficulty.