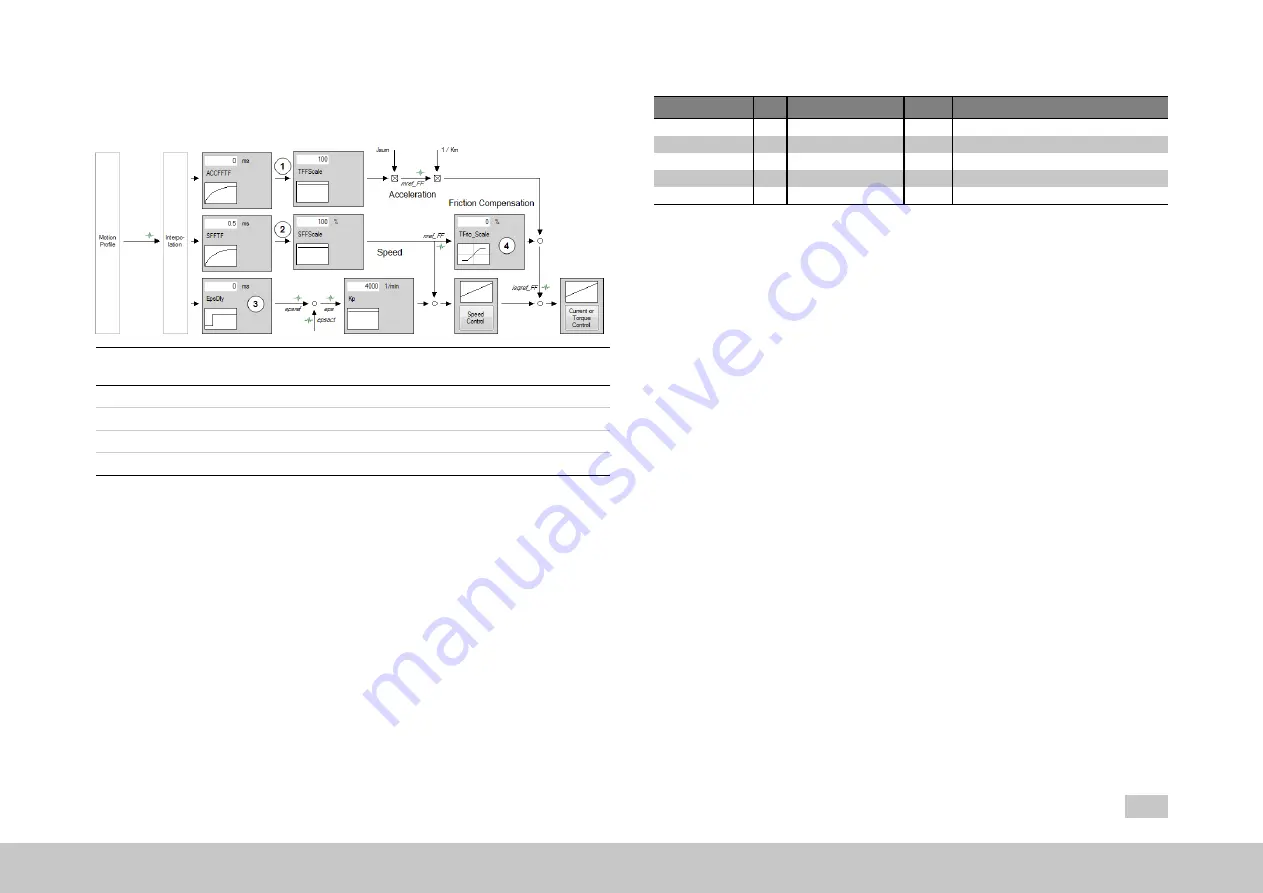
7.5 Position controller settings
Image 7.30: “Configuration of position controller and feed forward control” screen
①
Delay time and scaling for torque pre-control
②
Delay time and scaling for speed pre-control
③
Delay time for position pre-control
④
Scaling of friction torque
Legend for “Configuration of position controller and feed forward control” screen
The higher the dynamism of the speed controller, the more dynamically the position
controller can be set and the tracking error minimized. The variables for the pre-
control of the speed and position controller are additionally determined either from
the change in reference values or alternatively are already calculated and outputted
by the motion control. The time-related values for the position, speed and torque are
transmitted to the drive control. If the dynamic change in these values is within the
limits which the drive is able to follow dynamically, the load on the controllers is
significantly reduced. In order to improve the dynamism of the position controller, the
following screen is provided to optimize the speed and acceleration pre-control.
MOOG
ID No.: CB40859-001 Date: 11/2020
MSD Servo Drive - Device Help
140
7 Control
ID
Index Name
Unit
Description
276
0
MPRO_FG_UsrActPos mDegree Actual position in user units
277
0
MPRO_FG_UsrRefPos mDegree Setpoint position in user units
279
0
MPRO_FG_UsrPosDiff mDegree Position tracking error in user units
305
0
CON_PConTS
ms
Position control sampling time
360
0
CON_PCON_Kp
1/min
Position control gain
Table 7.20: “Position controller” parameters
7.5.1 Pre-control
l
The pre-control of the acceleration torque relieves the strain on the speed
controller and optimizes the control response of the drive. To be able to pre-
control the acceleration torque, the mass inertia referred to the motor shaft
must be known. If the parameter for the overall mass inertia of the system
(
P 1516[0] - SCD_Jsum)
has a value ≠ 0, that value will be automatically
used to pre-control the acceleration torque.
l
The pre-control of the speed reference is set to 100% via
P 375[0] - CON_
IP_SFF_Scale
. This value should not be changed.
l
The acceleration torque pre-control can be optimized with
P 376[0] - CON_
IP_TFF_Scale
. Reducing this reduces the pre-control value; conversely,
increasing this value also increases the pre-control value.
l
The position tracking error can be further reduced by predictive torque and
speed pre-control – that is, in advance of the position reference setting.
Owing to the time-discrete mode of operation of the control circuits and the
limited dynamism of the current control circuit, this prediction is necessary to
prevent the individual control circuits from oscillating against one another.
Prediction in pre-control is achieved by retarding the references for speed
and position controllers.