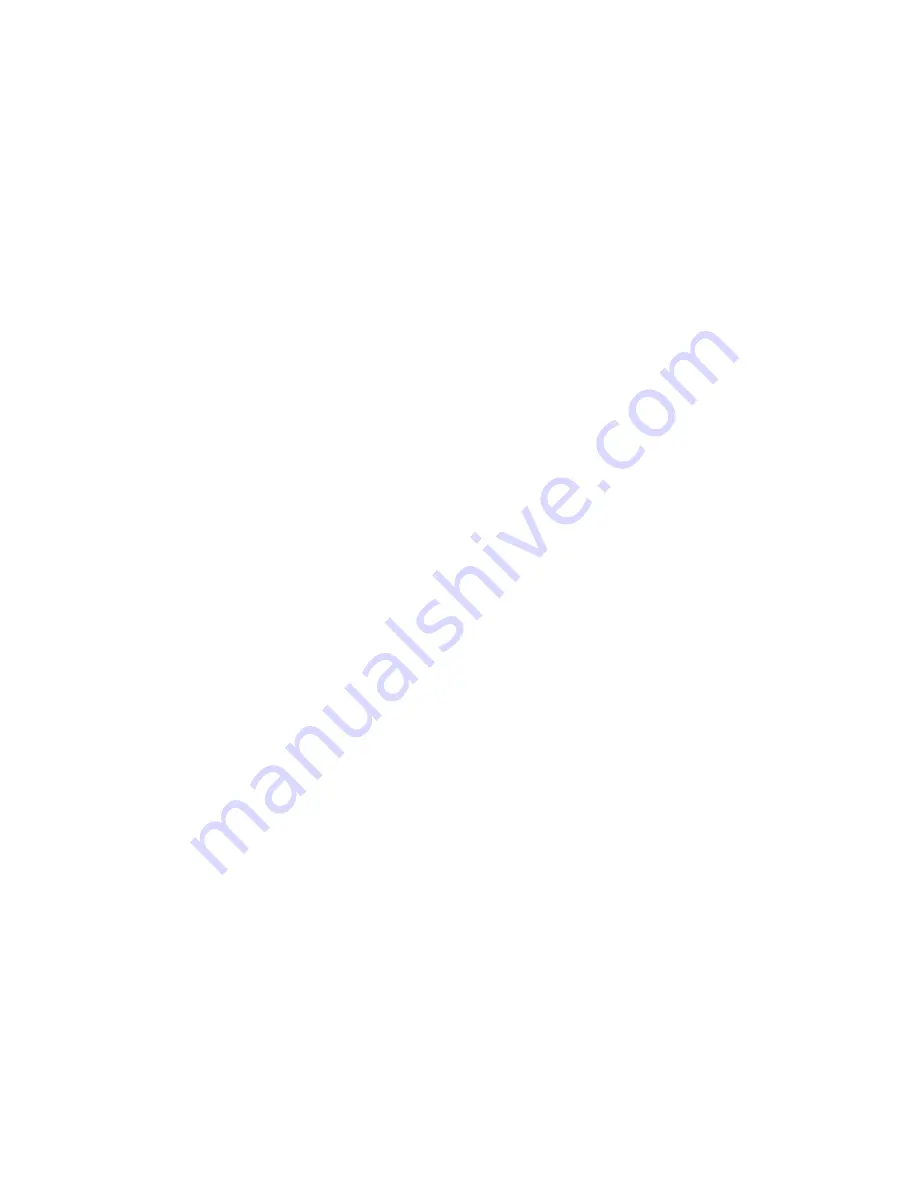
946 Controller Instruction Manual
pg. 74
7.6.3 Setup
1. Set the mass flow controller into position where it will be connected to a gas supply.
Placement of flow components in an orientation other than that in which they were
calibrated (typically horizontal) may cause a small zero shift. The zero offset can be
removed by adjusting the zero potentiometer on the mass flow controller, or via the 946
Controller.
2. Install the flow controller in the gas stream such that the flow will be in the direction of the
arrow on the side of the controller.
3. Allow adequate clearance for the cable connector (approximately 3” height) and tubing
connections/fittings.
4. Position the flow controller to provide access to the zero potentiometer. The zero
potentiometer is located on the inlet side of the flow controller body.
7.6.4 Gas Line Connections
Connect the gas line (via tubing) from the gas supply to the flow controller’s inlet, and from the flow
controller’s outlet, to the downstream tubing. Remember to follow all applicable procedures for gas line
installation, gas handling and leak testing of gas lines especially when toxic or corrosive gases are used.
7.7 Installing a Pressure Control Valve
Either an upstream solenoid valve or a downstream throttle valve can be connected to the 946 to perform
system pressure control. This feature requires the 946 to have the Pressure Control (PC) option installed.
7.7.1 Installing an Upstream Solenoid Valve
Only one upstream valve (148, 248, 154) can be controlled with the 946 Vacuum System Controller. If
multiple gases are used for system pressure control, MFC based ratio control is recommended.
7.7.1.1 Mounting the Valve
•
Ensure the flow direction arrow on the valve body is pointing towards the vacuum chamber.
•
The valve may be installed in any position, although base down is recommended.
•
Although ¼” O.D. tubing connections are generally adequate to support the weight of the valve, it
is recommended to mount the valve on a base plate with the two 10-24 mounting holes in the
valve body.
•
Tubing lengths should be kept short throughout the flow control loop. Restrictions and bends
should be eliminated wherever possible.
7.7.1.2 Inlet Pressure
•
The 148/248/154 valve may be operated with 150 psig maximum inlet pressure, however, the
nominal flow rating is established at 1 atmosphere differential across the valve, increasing with
the inlet pressure up to the maximum allowed. This extends the maximum flow control range from
approximately 3X (10,000 SCCM range) to 250X (10 SCCM range).
•
Decreasing the outlet pressure increases the flow range until the choked flow condition is
reached. Further lowering of outlet pressure for a fixed inlet pressure will not increase flow
because a sonic restriction exists.
•
If low flow rate is desired (such as used in control the high vacuum system pressure), the inlet
pressure must be regulated at very low pressure to avoid pressure burst inside the chamber
during the valve operation, which may cause damage to the turbo pump or a hot cathode sensor.
7.7.1.3 Connecting the Valve to 946 Controller
Cable part number 100018192 can be used to connect an MKS 148/248/154 upstream valve to the 946
Vacuum System Controller.
The pinout for the connector on 946 pressure control module is shown in Table 7-. When the pressure
control board is used for controlling an upstream solenoid valve, only pins 6 and 7 are used.