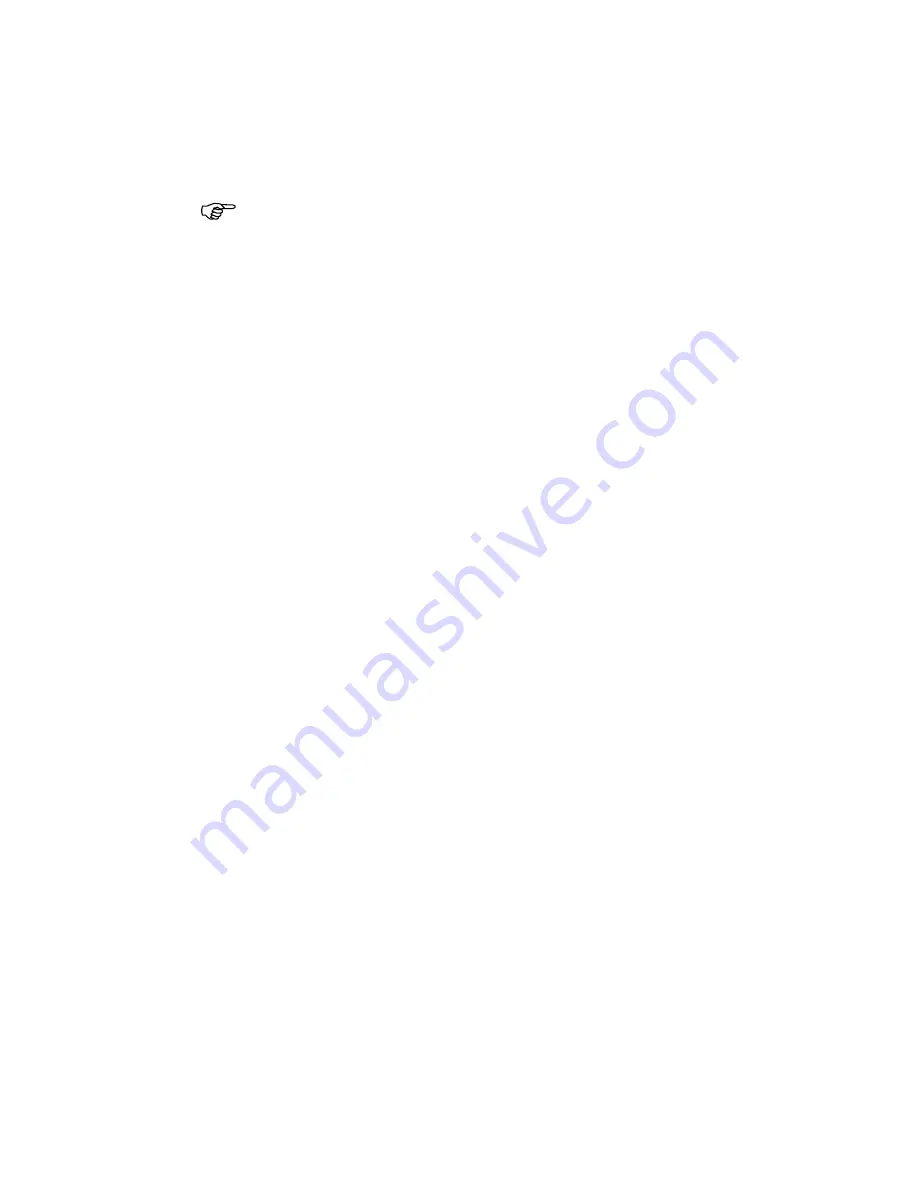
946 Controller Instruction Manual
pg. 50
7. Flow Rate SP
Flow Rate SP is the entered flow rate set point for MFC set point mode operation. The MFC
can be set to close when the set point value is less than 2% of the full scale and to open
when the set point value is greater than the full scale (100%). When the MFC is set to run in
other control modes (Open, Close, Ratio, PID), this set point value is ignored.
The value for the Flow Rate SP is the actual flow rate after accounting for the
scale factor.
8. Operation Voltage
The 946 can power both +/-15 Vdc MFCs and +15 to +24 Vdc MFCs. Before selecting
the operating voltage, verify the operating voltage of the MFC. Note that the voltage
selection applies to both channels of the module, i.e. B1 and B2.
9. Relay
There are two relays assigned for each MFC. These relays are normally used to provide
alarm signals. For example, a relay can be used to report a low flow, such as would be
caused by an empty gas cylinder.
6.7.3 Set MFC(s) for Dynamically Controlling System Pressure
MFC(s) can be used for the dynamic control of system pressure such as in process control,
calibration and controlled chamber backfilling where a stable chamber pressure is required. The
system pressure may be controlled by single MFC (PID Ctrl) or multiple MFCs (Ratio Control).
Several control parameters are involved in dynamic pressure control using MFC(s) and control
recipes must be defined before activating the control. For single MFC pressure control, only the
PID recipe needs to be defined. However, when multiple MFCs are used for ratio system
pressure control, a ratio recipe must be defined in addition to the PID recipe.
In the 946 Controller, only one PID control recipe can be run at a time, but PID and Set Point
modes are independent. If one MFC is set to PID control mode, other MFCs can operate
simultaneously in the Set point mode. Similarly, if several MFCs are operated under the ratio
control mode, the remaining connected MFCs can still operate in Set point mode.
6.7.3.1 Set Single MFC for Controlling System Pressure
PID dynamic control of flow rates allows quicker, more exact attainment and maintaining of a
pressure than set point control. Due to variations in pumping speed, chamber outgassing and
size, there can be a wide variance in the pressure attained with set point control. At least one
pressure control module (e.g., a Capacitance Manometer) is required for measuring the pressure
when PID control is used.
For PID operation, an appropriate PID recipe must first be defined. In a 946 Controller, a
maximum of 8 recipes (R1 to R8) can be defined as shown in Figure 6-14.