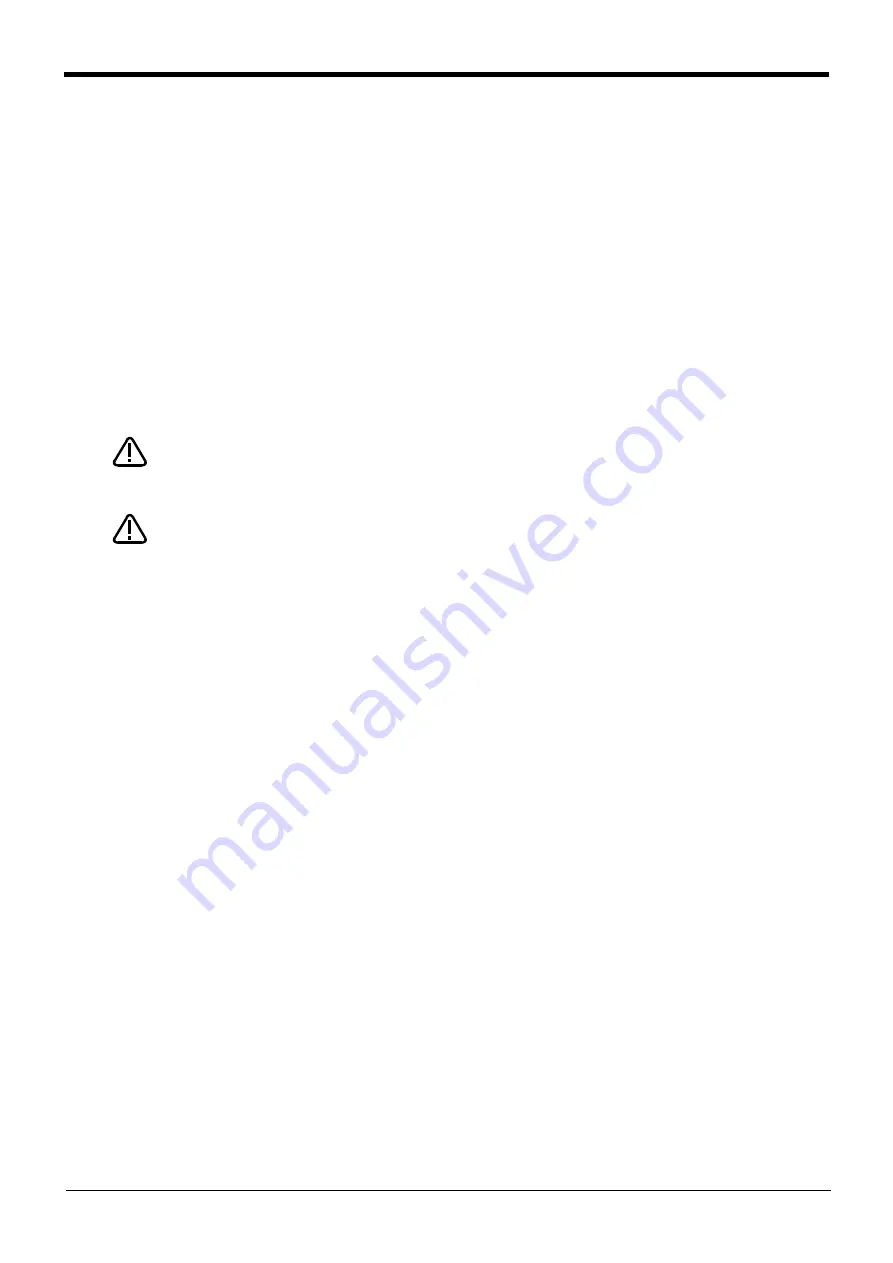
5
55
5-
--
-42
42
42
42
Maintenance and inspection procedures
Maintenance and inspection procedures
Maintenance and inspection procedures
Maintenance and inspection procedures
5
55
5Maintenance and Inspection
Maintenance and Inspection
Maintenance and Inspection
Maintenance and Inspection
5.3.3 Inspecting, servicing, replacing and cleaning the timing belt
5.3.3 Inspecting, servicing, replacing and cleaning the timing belt
5.3.3 Inspecting, servicing, replacing and cleaning the timing belt
5.3.3 Inspecting, servicing, replacing and cleaning the timing belt
This robot uses a timing belt for the drive conveyance system. Compared to gears and chains, the timing belt
This robot uses a timing belt for the drive conveyance system. Compared to gears and chains, the timing belt
This robot uses a timing belt for the drive conveyance system. Compared to gears and chains, the timing belt
This robot uses a timing belt for the drive conveyance system. Compared to gears and chains, the timing belt
does not require lubrication and has a low noise. However, if the belt usage method and tension adjustment are
does not require lubrication and has a low noise. However, if the belt usage method and tension adjustment are
does not require lubrication and has a low noise. However, if the belt usage method and tension adjustment are
does not require lubrication and has a low noise. However, if the belt usage method and tension adjustment are
inadequate, the life could drop and noise could be generated. Sufficient aging to remove the initial elongation of
inadequate, the life could drop and noise could be generated. Sufficient aging to remove the initial elongation of
inadequate, the life could drop and noise could be generated. Sufficient aging to remove the initial elongation of
inadequate, the life could drop and noise could be generated. Sufficient aging to remove the initial elongation of
the belt, and adjustment of the belt tension have been carried out before shipment from the factory.
the belt, and adjustment of the belt tension have been carried out before shipment from the factory.
the belt, and adjustment of the belt tension have been carried out before shipment from the factory.
the belt, and adjustment of the belt tension have been carried out before shipment from the factory.
However, depending on the robot working conditions, elongation will occur gradually over a long time. The tension
However, depending on the robot working conditions, elongation will occur gradually over a long time. The tension
However, depending on the robot working conditions, elongation will occur gradually over a long time. The tension
However, depending on the robot working conditions, elongation will occur gradually over a long time. The tension
must be confirmed during the periodic inspection. The timing belt must be replaced in the following cases.
must be confirmed during the periodic inspection. The timing belt must be replaced in the following cases.
must be confirmed during the periodic inspection. The timing belt must be replaced in the following cases.
must be confirmed during the periodic inspection. The timing belt must be replaced in the following cases.
(
1
) Timing belt replacement period
(
1
) Timing belt replacement period
(
1
) Timing belt replacement period
(
1
) Timing belt replacement period
The timing belt life is greatly affected by the robot working conditions, so a set time cannot be given. However, if
The timing belt life is greatly affected by the robot working conditions, so a set time cannot be given. However, if
The timing belt life is greatly affected by the robot working conditions, so a set time cannot be given. However, if
The timing belt life is greatly affected by the robot working conditions, so a set time cannot be given. However, if
the following symptoms occur, replace the belt.
the following symptoms occur, replace the belt.
the following symptoms occur, replace the belt.
the following symptoms occur, replace the belt.
1
) When cracks form at the base or back of the belt teeth.
1
) When cracks form at the base or back of the belt teeth.
1
) When cracks form at the base or back of the belt teeth.
1
) When cracks form at the base or back of the belt teeth.
2) When the belt expands due to adherence of oil, etc.
2) When the belt expands due to adherence of oil, etc.
2) When the belt expands due to adherence of oil, etc.
2) When the belt expands due to adherence of oil, etc.
3) When the belt teeth wear (to approx. half of the tooth width).
3) When the belt teeth wear (to approx. half of the tooth width).
3) When the belt teeth wear (to approx. half of the tooth width).
3) When the belt teeth wear (to approx. half of the tooth width).
4) When the belt teeth jump due to belt teeth wear.
4) When the belt teeth jump due to belt teeth wear.
4) When the belt teeth jump due to belt teeth wear.
4) When the belt teeth jump due to belt teeth wear.
5) When the belt snaps.
5) When the belt snaps.
5) When the belt snaps.
5) When the belt snaps.
Due to the manufacturing of the timing belt, initial wear will occur. Wear chips may
Due to the manufacturing of the timing belt, initial wear will occur. Wear chips may
Due to the manufacturing of the timing belt, initial wear will occur. Wear chips may
Due to the manufacturing of the timing belt, initial wear will occur. Wear chips may
accumulate in the cover after approx. 300 Hr of operating the robot, but this is not a
accumulate in the cover after approx. 300 Hr of operating the robot, but this is not a
accumulate in the cover after approx. 300 Hr of operating the robot, but this is not a
accumulate in the cover after approx. 300 Hr of operating the robot, but this is not a
fault. If the wear chips appear soon after wiping them off, replace the belt.
fault. If the wear chips appear soon after wiping them off, replace the belt.
fault. If the wear chips appear soon after wiping them off, replace the belt.
fault. If the wear chips appear soon after wiping them off, replace the belt.
When the belt is replaced, the origin of the machine system could deviate. In this
When the belt is replaced, the origin of the machine system could deviate. In this
When the belt is replaced, the origin of the machine system could deviate. In this
When the belt is replaced, the origin of the machine system could deviate. In this
case, review the position data.
case, review the position data.
case, review the position data.
case, review the position data.
CAUTION
CAUTION
CAUTION
CAUTION
CAUTION
CAUTION
CAUTION
CAUTION