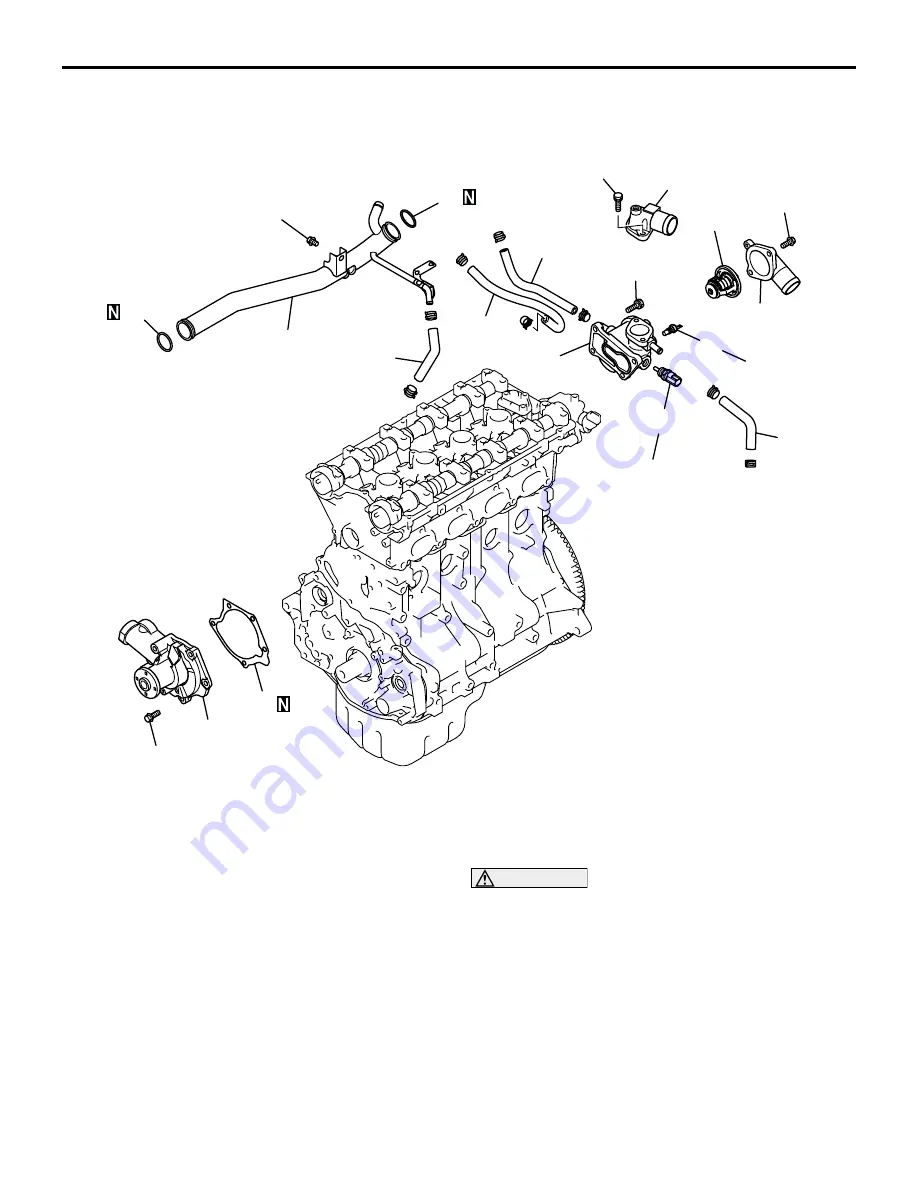
WATER PUMP AND WATER HOSE
ENGINE OVERHAUL <4G63-Turbo>
11D-33
WATER PUMP AND WATER HOSE
REMOVAL AND INSTALLATION
M1113017900372
INSTALLATION SERVICE POINTS
>>A<< O-RING/WATER INLET PIPE
INSTALLATION
CAUTION
•
Never allow any oil or grease to touch the
O-rings.
•
Clamp the water inlet pipe only after
installation of the thermostat case.
Replace the O-rings at both ends of the water inlet
pipe with new ones. Insert the O-rings into the water
pump and thermostat housing after wetting their
peripheries with water.
AK304981
13 ± 2 N·m
15
AC
29 ± 10 N·m
14 ± 1 N·m
14
3
2
1
4
5
10
6
8
7
9
13 ± 2 N·m
10.8 ± 1.0 N·m
23 ± 4 N·m
13 ± 2 N·m
11
13
12
Removal sequence
1. Water hose
2. Water hose
3. Water hose
4. Water hose
>>E<<
5. Engine coolant temperature sensor
>>D<<
6. Engine coolant temperature gauge
unit
7. Water inlet fitting
8. Thermostat
>>C<<
9. Water outlet fitting
>>B<<
10. Thermostat housing
>>A<<
11. O-ring
>>A<<
12. Water inlet pipe
>>A<<
13. O-ring
14. Water pump
15. Water pump gasket
Содержание 4g63
Страница 68: ...NOTES ...