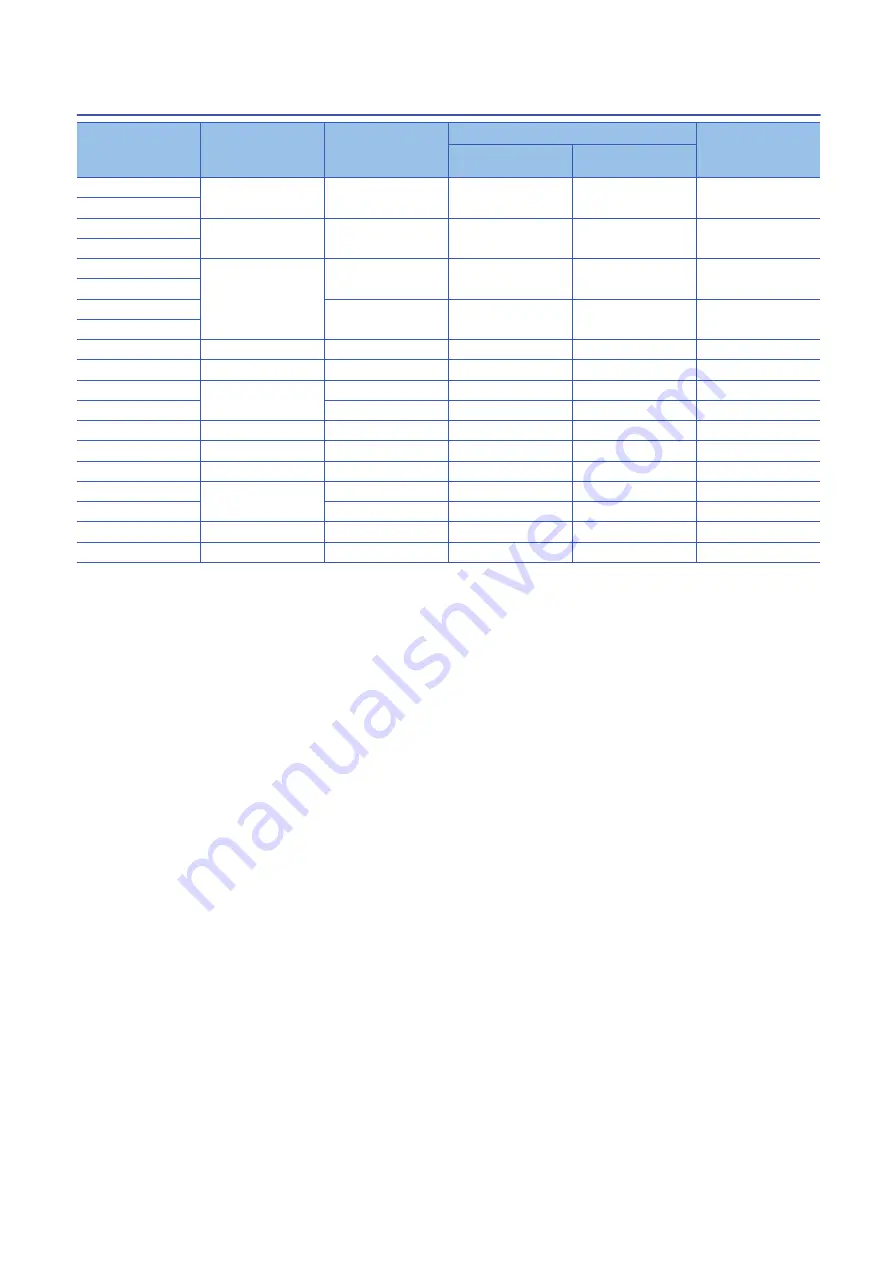
290
10 USING A DIRECT DRIVE MOTOR
10.5 Characteristics
Power supply capacity and generated loss
Direct drive motor
Servo amplifier
Power supply
capacity [kVA]
Servo amplifier-generated heat [W]
Area required for
heat dissipation
[m
2
]
At rated output
At servo-off
TM-RG2M002C30
MR-J5-20_
0.25
25
15
0.5
TM-RU2M002C30
TM-RG2M004E30
MR-J5-20_
0.5
25
15
0.5
TM-RU2M004E30
TM-RG2M004E30
MR-J5-40_
0.7
35
15
0.7
TM-RU2M004E30
TM-RG2M009G30
0.9
35
15
0.7
TM-RU2M009G30
TM-RFM002C20
MR-J5-20_
0.25
25
15
0.5
TM-RFM004C20
MR-J5-40_
0.38
35
15
0.7
TM-RFM006C20
MR-J5-60_
0.53
40
15
0.8
TM-RFM006E20
0.46
40
15
0.8
TM-RFM012E20
MR-J5-70_
0.81
50
15
1.0
TM-RFM018E20
MR-J5-100_
1.3
50
15
1.0
TM-RFM012G20
MR-J5-70_
0.71
50
15
1.0
TM-RFM048G20
MR-J5-350_
2.7
130
20
2.6
TM-RFM072G20
3.8
130
20
2.6
TM-RFM040J10
MR-J5-70_
1.2
50
15
1.0
TM-RFM120J10
MR-J5-350_
3.4
130
20
2.6
Содержание MR-J5 Series
Страница 1: ...MR J5 User s Manual Hardware MR J5 _G_ MR J5W_ _G MR J5 _A_ Mitsubishi Electric AC Servo System ...
Страница 2: ......
Страница 315: ......