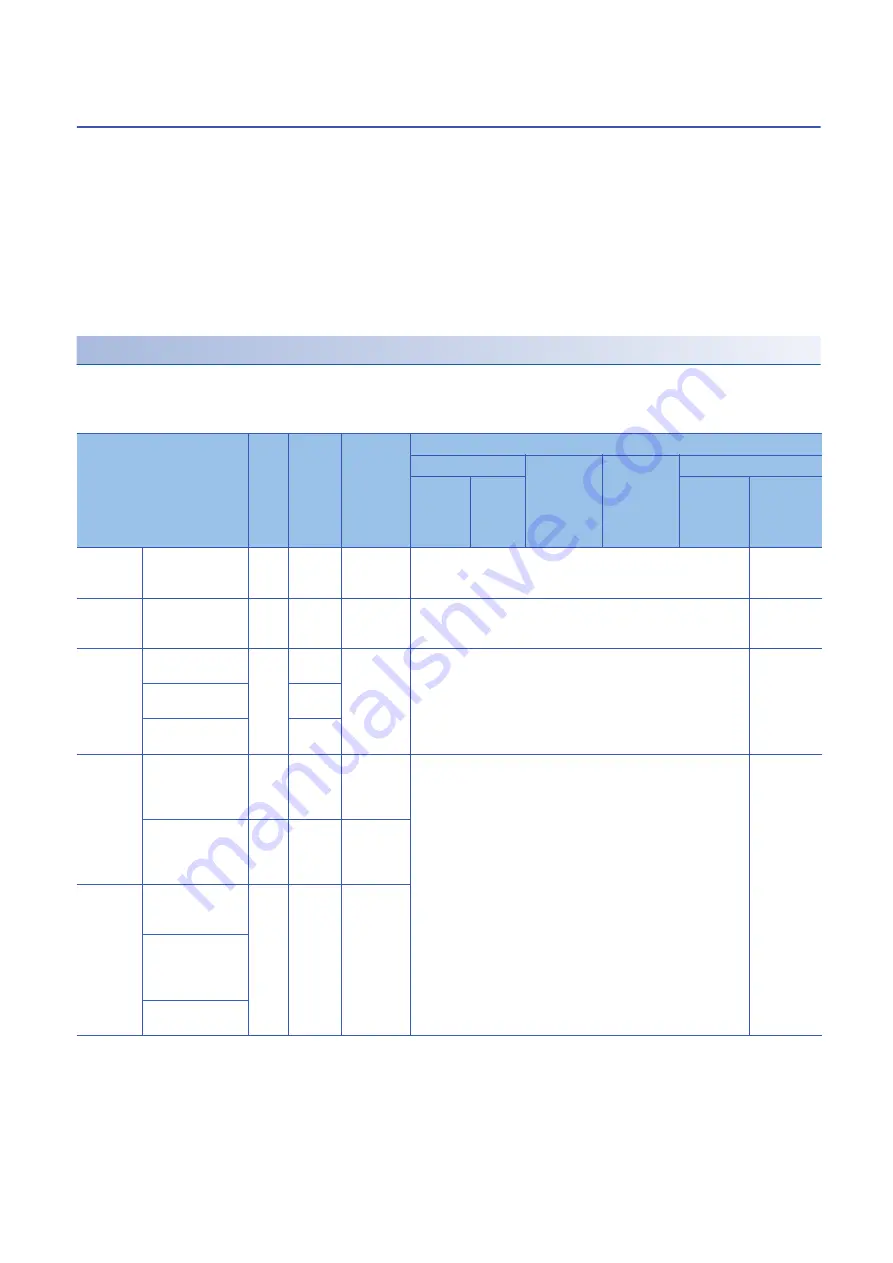
32
1 STARTING AND STOPPING
1.2 Stopping
1.2
Stopping
This section describes the stop control of the positioning. The following events may stop each positioning control by the
RD75.
• When each control ends normally
• When Drive unit READY signal (READY) is turned off
• When an error occurred in the CPU module
• When PLC READY signal [Y0] is turned off
• When an error occurs in the RD75
• When an operation is intentionally stopped (When a stop signal sent from the CPU module is turned on, or a stop signal
from an external device)
Stop processing
The stop controls are classified into three types: deceleration stop, sudden stop, and immediate stop. The following table
describes the stop controls (deceleration stop, sudden stop, and immediate stop) at the occurrence of each stop cause (When
the automatic deceleration control is performed).
Stop cause
Stop
axis
M code
ON
signal
after
stop
[Md.26]
Axis
operation
status
after stop
Stop processing
OPR control
Major
positioning
control
Advanced
positioning
control
Manual control
Machine
OPR
control
Fast
OPR
control
Inching
operation,
JOG
operation
Manual
pulse
generator
operation
Forced
stop
Drive unit READY
signal (READY) is
off
Each
axis
Not
changed
Error
Immediate stop
Deceleration
stop
Fatal stop
(Stop
group 1)
Hardware stroke
limit upper/lower
limit error occurred
Each
axis
Not
changed
Error
Deceleration stop or sudden stop (Select with [Pr.37] Stop group 1
sudden stop selection.)
Deceleration
stop
Emergency
stop (Stop
group 2)
CPU module error
occurred
All
axes
Not
changed
Error
Deceleration stop or sudden stop (Select with [Pr.38] Stop group 2
sudden stop selection.)
Deceleration
stop
PLC READY signal
[Y0] is off
Turned
off
Failure in the test
mode
Not
changed
Relatively
safe stop
(Stop
group 3)
Axis error detection
(errors other than
the ones in stop
group 1 and 2)
Each
axis
Not
changed
Error
Deceleration stop or sudden stop (Select with [Pr.39] Stop group 3
sudden stop selection.)
Deceleration
stop
Error at operation
mode switching in
amplifier-less
operation
All
axes
Not
changed
Error
Intentional
stop (Stop
group 3)
Stop signal turned
on by an external
device
Each
axis
Not
changed
Stopped
(standby)
Axis stop signal [Y4,
Y5, Y6, Y7] from the
CPU module is
turned on.
Stop signal from an
engineering tool
Содержание MELSEC iQ-R RD75P4
Страница 1: ...MELSEC iQ R Positioning Module User s Manual Application RD75P2 RD75P4 RD75D2 RD75D4 ...
Страница 2: ......
Страница 13: ...11 MEMO ...
Страница 19: ...17 CONTENTS INDEX 588 REVISIONS 592 WARRANTY 593 TRADEMARKS 594 ...
Страница 498: ...496 13 PROGRAMMING 13 2 List of Labels Used ...
Страница 503: ...13 PROGRAMMING 13 4 Program Example 501 13 ...
Страница 511: ...13 PROGRAMMING 13 4 Program Example 509 13 Torque change program Step operation program Skip program ...
Страница 512: ...510 13 PROGRAMMING 13 4 Program Example Teaching program Continuous operation interrupt program ...
Страница 513: ...13 PROGRAMMING 13 4 Program Example 511 13 Target position change program Absolute position restoration program ...
Страница 514: ...512 13 PROGRAMMING 13 4 Program Example Restart program Parameter data initialization program ...
Страница 515: ...13 PROGRAMMING 13 4 Program Example 513 13 Flash ROM write program Error reset program ...
Страница 516: ...514 13 PROGRAMMING 13 4 Program Example Stop program ...
Страница 565: ...APPENDICES Appendix 4 Operation Examples of When the Remote Head Module Is Mounted 563 A ...
Страница 568: ...566 APPENDICES Appendix 4 Operation Examples of When the Remote Head Module Is Mounted Common program ...
Страница 584: ...582 APPENDICES Appendix 4 Operation Examples of When the Remote Head Module Is Mounted Restart program ...
Страница 587: ...APPENDICES Appendix 4 Operation Examples of When the Remote Head Module Is Mounted 585 A Stop program ...
Страница 597: ......