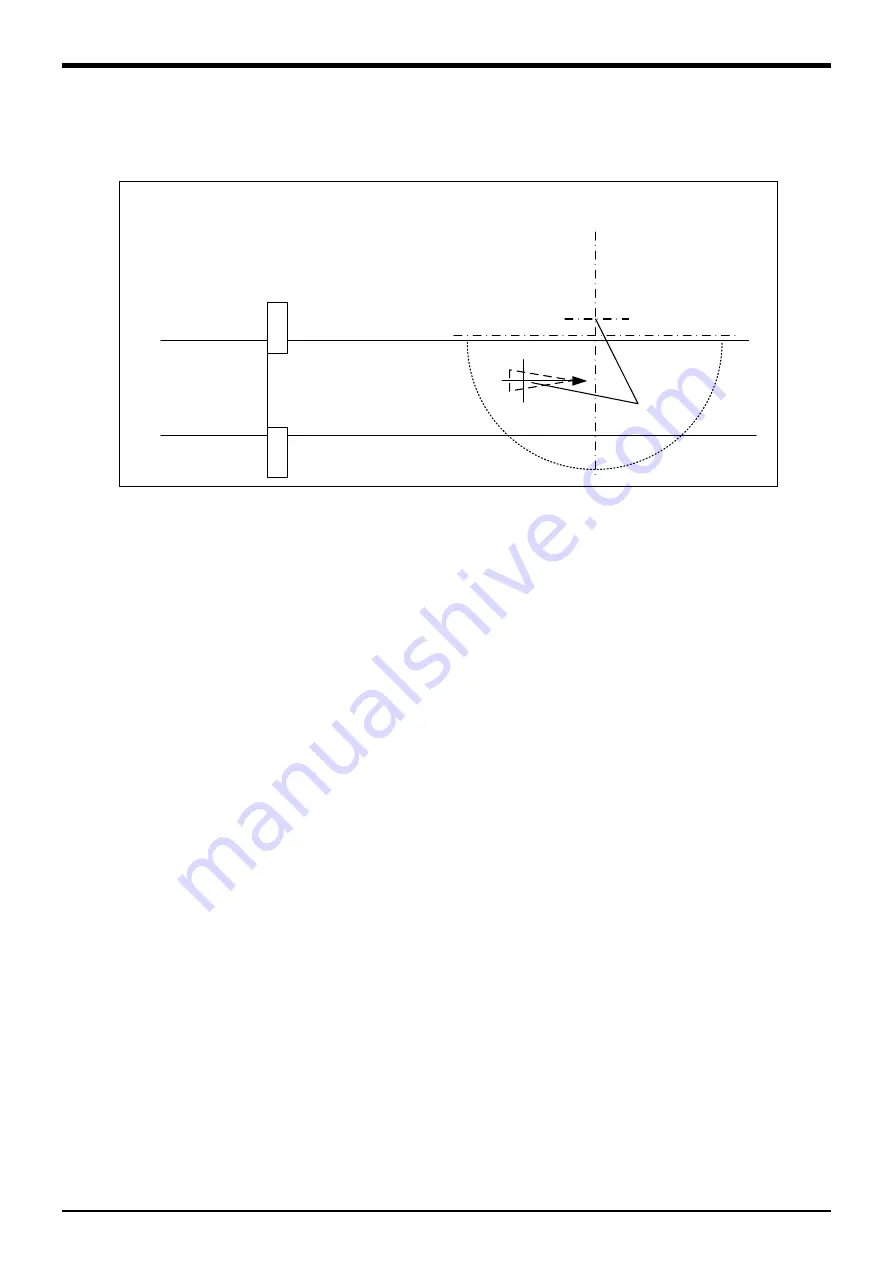
10 Workpiece Recognition and Teaching (“C1” program)
10-68 Conveyer Tracking
(11)
Press the [F1] (FWD) key and execut
e step feed. “
(6)Move the robot to the suction position…”
is displayed.
Move the robot to the position where it suctions the workpiece.
* With this operation, encoder data and robot position are acquired.
Area recognized by
a workpiece sensor
Robot movement range
Move the hand
(12)
Perform step operation until “End.”
* With this operation, the robot is able to calculate the position of a workpiece as soon as the
sensor is activated.
10.1.2.
Confirmation after operation
Confirm the values of “M_101(),” “P_100()” and “P_102()” using T/B.
Enter
encoder numbers
in array elements.
“M_101()”: Differences between the encoder values acquired at the position of the photoelectronic sensor
and the encoder values acquired on the robot side.
“P_100()”: Position at which workpieces are suctioned
“P_102()”:
Values of th
e X coordinate = variable "MEncNo (encoder number)", Y coordinate = "MSenNo
(sensor number)"
Check that each of the values above has been entered correctly.
10.1.3.
When multiple conveyers are used
Carry out the same operations as above when multiple conveyers are used as well, but pay attention to the
following points.
Example
)
When using conveyer 2 (encoder number
“
2”
), kind number “
2”
,
(a) Copy the “C
1”
program, please create a “C
2”
program.
(b)
Please change the kind number for variable
“MWrkNo
”
in the “
C2”
program to “
2”
.
(c)
Please change the encoder number for variable
“
MEncNo”
in the “
C2”
program to “
2”
.
Содержание CR800 Series
Страница 2: ......
Страница 12: ......
Страница 29: ...3 Specification Q173DPX manual pulser input unit specification 3 17 3 Specification of hardware 7 1ms ...
Страница 202: ...18 Appendix 18 190 Calibration sheet ...
Страница 203: ......
Страница 204: ...Apr 2020 MEE Printed in Japan on recycled paper Specifications are subject to change without notice ...