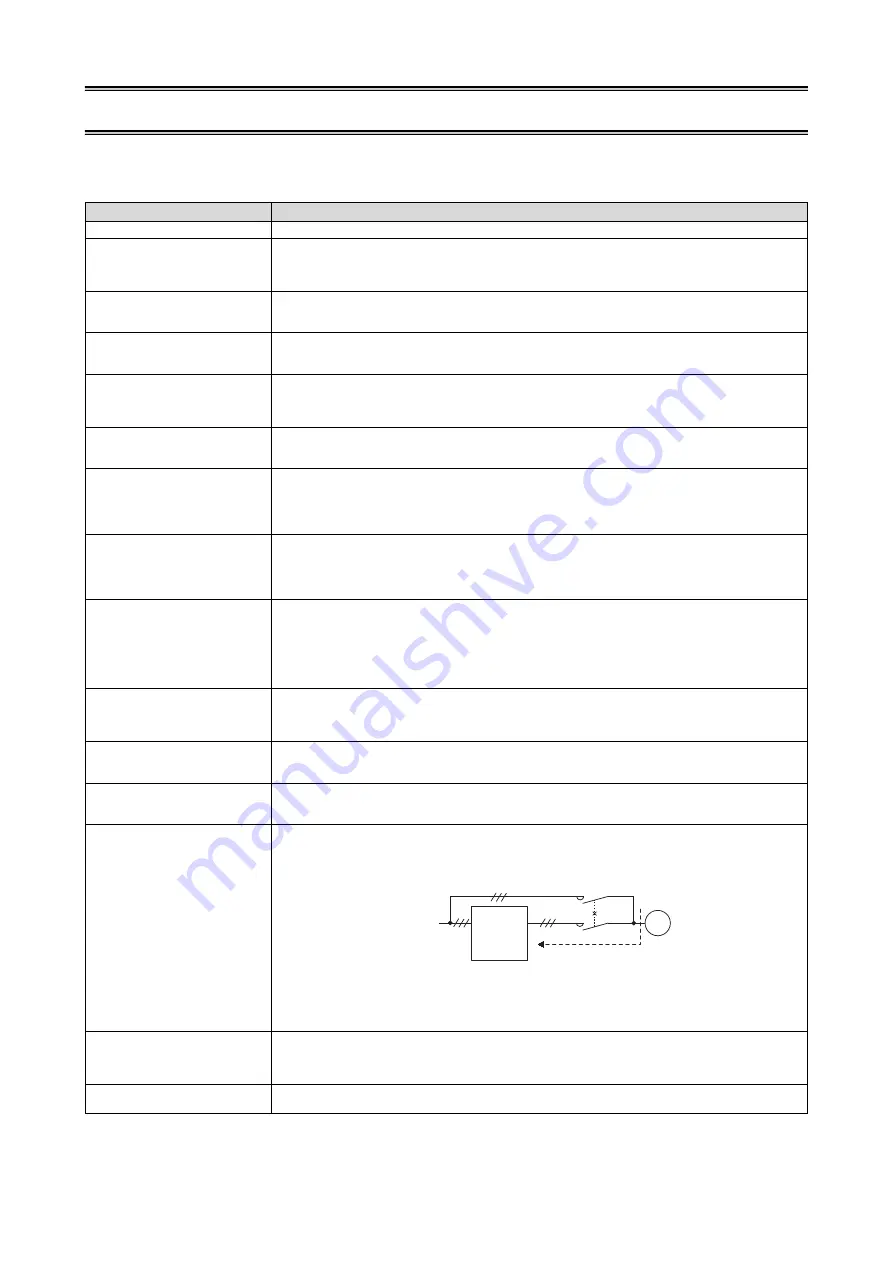
33
4 PRECAUTIONS FOR USE OF THE INVERTER
The FR-E800 series inverter is a highly reliable product, but incorrect peripheral circuit making or operation/handling
method may shorten the product life or damage the product. Before starting operation, always recheck the following
points.
Checkpoint
Countermeasure
Crimp terminals are insulated.
Use crimp terminals with insulation sleeves to wire the power supply and the motor.
The wiring between the power
supply (terminals R/L1, S/L2, T/
L3) and the motor (terminals U, V,
W) is correct.
Application of power to the output terminals (U, V, W) of the inverter will damage the inverter. Never
perform such wiring.
No wire offcuts are left from the
time of wiring.
Wire offcuts can cause a fault, failure, or malfunction. Always keep the inverter clean. When drilling
mounting holes in an enclosure etc., take caution not to allow chips and other foreign matter to enter
the inverter.
The main circuit cable gauge is
correctly selected.
Use an appropriate cable gauge to suppress the voltage drop to 2% or less. If the wiring distance is
long between the inverter and motor, a voltage drop in the main circuit will cause the motor torque to
decrease especially during the output of a low frequency.
The total wiring length is within
the specified length.
Keep the total wiring length within the specified length. In long distance wiring, charging currents
due to stray capacitance in the wiring may degrade the fast-response current limit operation or
cause the equipment on the inverter's output side to malfunction. Pay attention to the total wiring
length.
Countermeasures are taken
against EMI.
The input/output (main circuit) of the inverter includes high frequency components, which may
interfere with the communication devices (such as AM radios) used near the inverter. Connect radio
noise filters or EMC filters on the input side of the inverter to minimize interference.
On the inverter's output side,
there is no power factor
correction capacitor, surge
suppressor, or radio noise filter
installed.
Doing so will shut off the inverter output or damage the capacitor or surge suppressor. If any of the
above devices is connected, immediately remove it.
When performing an inspection
or rewiring on the product that
has been energized, the operator
has waited long enough after
shutting off the power supply.
For a short time after the power-OFF, a high voltage remains in the smoothing capacitor, and it is
dangerous. Before performing an inspection or rewiring, wait 10 minutes or longer after the power
supply turns OFF, then confirm that the voltage across the main circuit terminals P/+ and N/- of the
inverter is low enough using a digital multimeter, etc.
The inverter's output side has no
short circuit or ground fault
occurring.
A short circuit or ground fault on the inverter's output side may damage the inverter module.
Fully check the insulation resistance of the circuit prior to inverter operation since repeated short
circuits caused by peripheral circuit inadequacy or an earth (ground) fault caused by wiring
inadequacy or reduced motor insulation resistance may damage the inverter module.
Fully check the to-earth (ground) insulation and phase-to-phase insulation of the inverter's output
side before power-ON. Especially for an old motor or use in hostile atmosphere, securely check the
motor insulation resistance, etc.
The circuit is not configured to
use the inverter's input-side
magnetic contactor to start/stop
the inverter frequently.
Since repeated inrush currents at power ON will shorten the life of the converter circuit, frequent
starts and stops of the magnetic contactor must be avoided. Turn ON or OFF the inverter's start
(STF/STR) signal to run or stop the inverter.
A mechanical brake is not
connected to terminals P/+ and
PR.
To terminals P/+ and PR, connect only an external brake resistor.
The voltage applied to the
inverter I/O signal circuits is
within the specifications.
Application of a voltage higher than the permissible voltage to the inverter I/O signal circuits or
opposite polarity may damage the I/O devices.
When using the electronic bypass
operation, electrical and
mechanical interlocks are
provided between the electronic
bypass contactors MC1 and
MC2.
When using a switching circuit as shown below, chattering due to misconfigured sequence or arc
generated at switching may allow undesirable current to flow in and damage the inverter. Miswiring
may also damage the inverter. (Note that a PM motor cannot be driven by the commercial power
supply.)
If switching to the commercial power supply operation while a failure such as an output short circuit
has occurred between the magnetic contactor MC2 and the motor, the damage may further spread.
If a failure has occurred between the MC2 and the motor, a protection circuit such as using the OH
signal input must be provided.
A countermeasure is provided for
power restoration after a power
failure.
If the machine must not be restarted when power is restored after a power failure, provide an MC on
the inverter's input side and also make up a sequence which will not switch ON the start signal. If the
start signal (start switch) remains ON after a power failure, the inverter will automatically restart as
soon as the power is restored.
For Vector control, the encoder is
properly installed.
The encoder must be directly connected to a motor shaft without any backlash. (Real sensorless
vector control or PM sensorless vector control does not require an encoder.)
MC2
MC1
U
V
W
R/L1
S/L2
T/L3
IM
Power
supply
Inverter
Undesirable current
Interlock
Содержание 800 Series
Страница 10: ...4 INSTALLATION AND INSTRUCTIONS ...
Страница 46: ...40 BASIC OPERATION ...
Страница 64: ...58 INVERTER FAULT AND ALARM INDICATIONS ...
Страница 70: ...64 SPECIFICATIONS ...