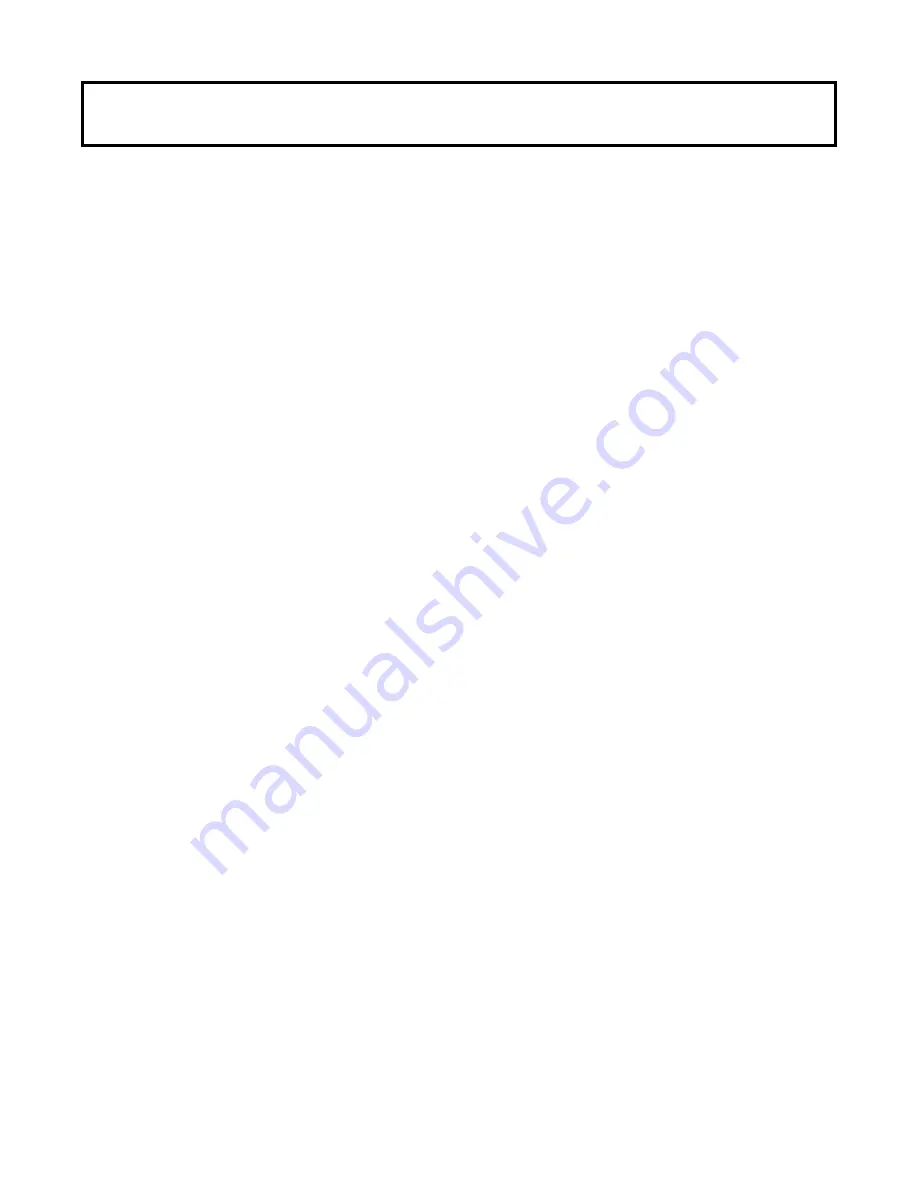
An active program of regular press inspection and pre-
ventive maintenance must be developed by the press
user management. Such a program is vital to the safe-
ty of press operators and necessary for continuous,
efficient production from the equipment. The complete
maintenance program should be set up as an orga-
nized procedure of routine press inspection, preventive
maintenance, repair or replacement of component
parts as required, and complete checkout after repair.
Regulations require records to be kept of press inspec-
tions and of the maintenance work performed.
Press inspection should be arranged to be performed
in varying degrees at predetermined intervals. For
example, daily inspections of a routine nature may be
handled by the press operators, die setters or foremen
during the course of their normal duties. This inspection
should cover obvious items such as point-of-operation
guards, lubricant levels, oil leaks, loose bolts, unusual
noises, loose belt, unusual vibrations, blown fuses,
varying speeds and operation of electrical controls.
More thorough inspections should be made on a week-
ly basis, usually with reference to a check list. These
inspections should include checks of fault detection cir-
cuits and checks for less obvious items such as
cracked or broken oil lines in concealed areas of the
press, condition of oil filters and proper operation of
press electrical controls through all functions.
In addition to the daily and weekly inspections, a
scheduled inspection should be performed each
month. Intensity of the monthly inspection will depend,
to a great degree, on how thoroughly the weekly
inspections are conducted. There is little to be gained
by duplicating checks of certain items while others go
unnoticed. Inspect items such as the clutch/brake unit,
slide parallelism, flywheel brake, solenoid valves, drive
belts, flywheel sheave and motor sheave. Also make
certain that all protective covers are securely installed.
Besides daily, weekly and monthly checks, a semian-
nual inspection should be performed to reveal general
condition of the press. At this time, check major frame
parts for cracks and broken sections; check bearing
clearances, press foundation and levelness; inspect all
components and wiring inside the electrical control
panel. Oil in the recirculating lube system should be
“reconditioned” or replaced after every 1300 hours of
operation and critical press parts inspected for cracks,
worn or broken sections. Parts needing replacement
should be ordered and time to perform repairs should
be scheduled.
As mentioned previously, a check list should be made
to cover each individual press installation. It should
include checkpoints recommended by Minster, plus
others that are special or applicable to the particular
press and its associated equipment. The list should be
arranged so that positive step by step inspections will
be performed at specific parts of the press on pre-
scribed dates. Copies of the list should be made so that
the inspector can check off or note results of each
check as it is made. The inspection reports may then be
filed as a part of the complete press record.
For your convenience, a sample “Press Inspection
Check List & Maintenance Record” is included in this
manual. Checkpoints normally required on most Model
101 OBI/OBS Series presses are listed. Make certain
to add any other items such as auxiliary equipment or
special features that are a part of the complete press
installation.
PERIODIC CLEANING
Press cleanliness is a very important part of good main-
tenance. Cleanliness contributes to safer and more
pleasant working conditions and the actual removal of
dirt, grime, oil and grease may reveal items that require
attention. Also, reduce the damaging effects of dirt and
other foreign particles by keeping cover plates in place,
by keeping cabinet doors tightly closed (except when
necessary to have them open) and by wiping up oil and
grease spills as soon as they occur.
Improperly controlled or misdirected air blowoffs, used
for part and scrap removal, may result in small parts
being blown into critical areas of the press. Adjoining
equipment and personnel may also be struck by these
particles. Safeguard personnel and increase protection
of the equipment by keeping air blowoff systems under
control. When cleaning the press, be sure to check for
any foreign particles that may be accumulating. Severe
damage to bearings, cylinders, motors, gears and
other parts may occur if these metal particles work their
way into them. Clean all accumulated metal particles,
chips and work pieces from press cavities, housings
and lube drains.
After each die installation, the press should be cleaned
and all wrenches, nuts, bolts, clamps and rags removed.
The floor around and under the press should also be
cleaned and kept free of finished parts, scrap material
and litter.
I - 2
INSPECTION & MAINTENANCE
Содержание IOI
Страница 1: ...Manual No 1010C MINSTER 8952 399 15 00 Service Manual OBI OBS SERIES PRESS MODEL...
Страница 2: ...Manual No 1010C MINSTER 8952 399 15 00 Service Manual OBI OBS SERIES PRESS MODEL...
Страница 9: ......
Страница 25: ......
Страница 51: ......
Страница 63: ......
Страница 85: ...I 8 COMMENTS CORRECTIVE STEPS TAKEN Inspected By Press approved for operation Press NOT approved for operation...
Страница 87: ...I 10 COMMENTS CORRECTIVE STEPS TAKEN Inspected By Press approved for operation Press NOT approved for operation...
Страница 89: ...I 12 COMMENTS CORRECTIVE STEPS TAKEN Inspected By Press approved for operation Press NOT approved for operation...
Страница 90: ...ADDITIONAL COMMENTS I 13...