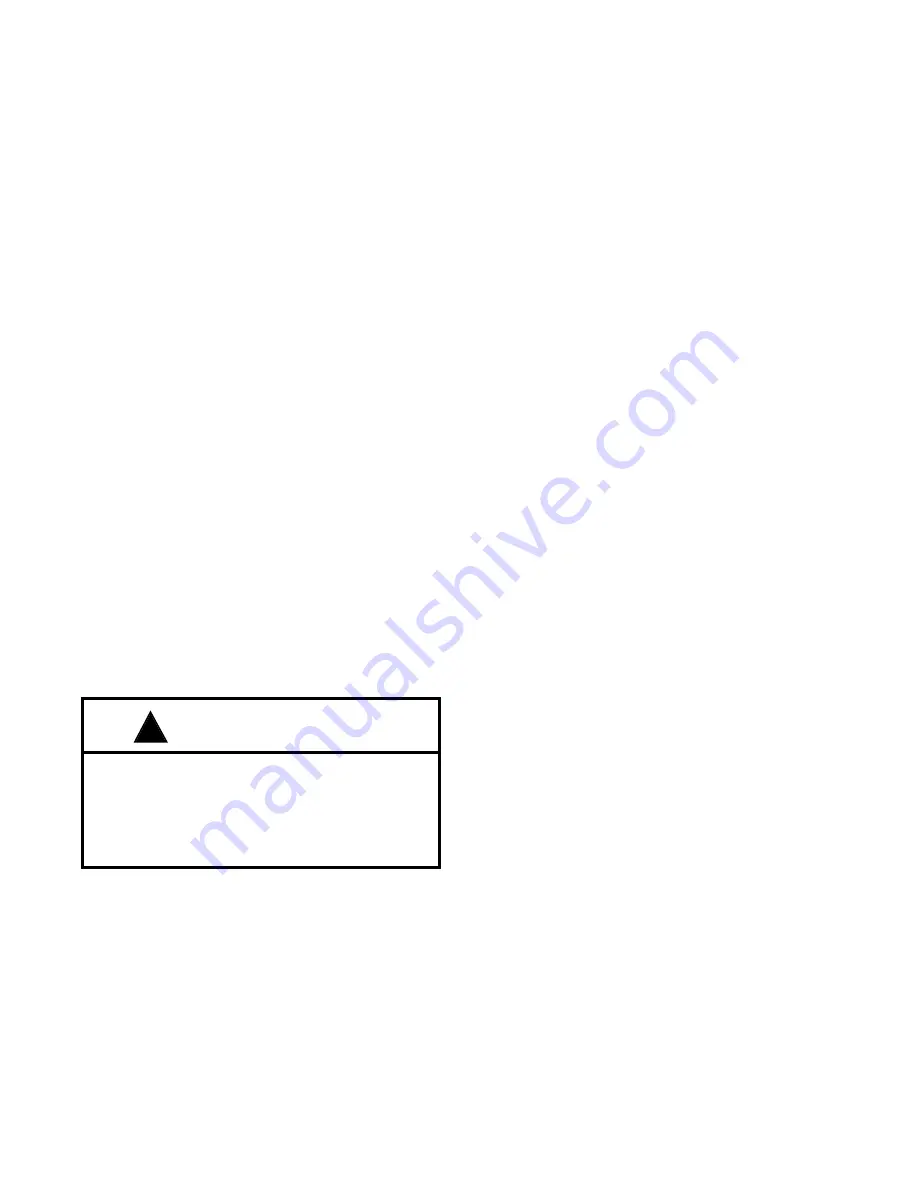
Effects of Improper Pressure
Having insufficient counterbalance air pressure can
lead to the following:
•
Linkage clearances are opened causing
hammering and die bounce
•
Sags on heavier end of slide
•
Motor and flywheel are required to lift unbalanced
weight to top of stroke causing excessive strain on
motor and clutch
•
Low pressure may allow downward movement
when clutch and brake are released
•
Cause damage to the slide adjust mechanism
•
Cause increased wear on bearings & gears
Having excessive counterbalance pressure can lead to
the following:
•
Excessive pressure may force slide upward when
clutch/brake is released
•
Takes energy out of the flywheel
•
Adds additional force to start/stop
•
Raises energy/air cost
•
Adds force on drive components and may cause
more wear.
•
May not allow proper lubrication
•
Cause damage to the slide adjust mechanism
•
Cause increased wear and damage to bearings and
gears
Both cases may have adverse effects on the bearings,
gears and slide adjust mechanism.
CAUTION
IMPROPER COUNTERBALANCE AIR PRESSURE
MAY CAUSE DAMAGE TO THE BEARINGS, GEARS
AND SLIDE ADJUST MECHANISM. MAKE CERTAIN
TO PROPERLY ADJUST COUNTERBALANCE
PRESSURE BEFORE ADJUSTING SLIDE
SHUTHEIGHT.
Service and Maintenance
Oil and other moisture accumulated in the bottom of
counterbalance cylinders must be drained once a week
- more often if necessary. An accumulation of oil or
other liquid may form a type of hydraulic lock inside the
cylinder, a condition that could cause extensive dam-
age to cylinders and other press parts. Start the drain-
ing procedure by relieving all air pressure within the
cylinders and surge tanks – then open the drain cocks
and wait for moisture to drain completely.
With air pressure turned off, check tightness of coun-
terbalance mounting bolts, rods and brackets. Perform
this check at least once per month. At the same time
check alignment of the cylinder with slide. A monthly
check should be made of lubrication lines and associ-
ated fittings connected to the counterbalance. Make
certain that they are not pinched shut, broken or leak-
ing.
Once a month, counterbalance cylinders and the sup-
ply lines should be checked for leaks. The air supply
lines should also be checked visually, for cracked and
damaged fittings.
Re-Applying Air After Shutdown
After shutting off the incoming air supply to the press,
do not open up the air lockout valve without first reduc-
ing counterbalance pressure. This is required so that
when air is reapplied to the counterbalance system it
will not experience a massive surge of air to the system
creating a shock load on the brackets and rods. This
could cause damage to the brackets and/ or rods.
NOTE: Newer automatic systems (i.e. the PMC con-
trol) may be pre-programmed to pulse air into
the system negating the need to reduce air
pressure before opening up the air lockout
valve.
To Check For Air Leaks In
The Counterbalance System:
1. Pressurize the counterbalance to approximately 60
psi (4.1 Bar) and then close the air lockout valve.
2. Observe counterbalance gauge for a sudden or
rapid drop in pressure. If pressure drops rapidly,
and external piping shows no signs of leakage (See
“Air Leaks,” page E-15), then the problem is most
likely caused by a worn seal within the cylinder.
Replace seal as outlined in the following procedure.
To Replace Slide
Counterbalance Cylinder Air Seal:
1. Stop the main drive motor.
2. Place the POWER, OFF-ON or POWER, OFF-ON-
BAR Selector Switch (whichever is applicable) in
the OFF position and remove the key (if applicable)
to lock the switch in the OFF position.
3. Lock the disconnect switch in the OFF position.
Make certain the flywheel has stopped turning com-
pletely. Attach a WARNING sign to the press con-
trols to advise other personnel that the press is
currently being serviced.
4. Shut OFF the air supply to the press and lock the air
lockout valve.
E - 9
!
Содержание IOI
Страница 1: ...Manual No 1010C MINSTER 8952 399 15 00 Service Manual OBI OBS SERIES PRESS MODEL...
Страница 2: ...Manual No 1010C MINSTER 8952 399 15 00 Service Manual OBI OBS SERIES PRESS MODEL...
Страница 9: ......
Страница 25: ......
Страница 51: ......
Страница 63: ......
Страница 85: ...I 8 COMMENTS CORRECTIVE STEPS TAKEN Inspected By Press approved for operation Press NOT approved for operation...
Страница 87: ...I 10 COMMENTS CORRECTIVE STEPS TAKEN Inspected By Press approved for operation Press NOT approved for operation...
Страница 89: ...I 12 COMMENTS CORRECTIVE STEPS TAKEN Inspected By Press approved for operation Press NOT approved for operation...
Страница 90: ...ADDITIONAL COMMENTS I 13...