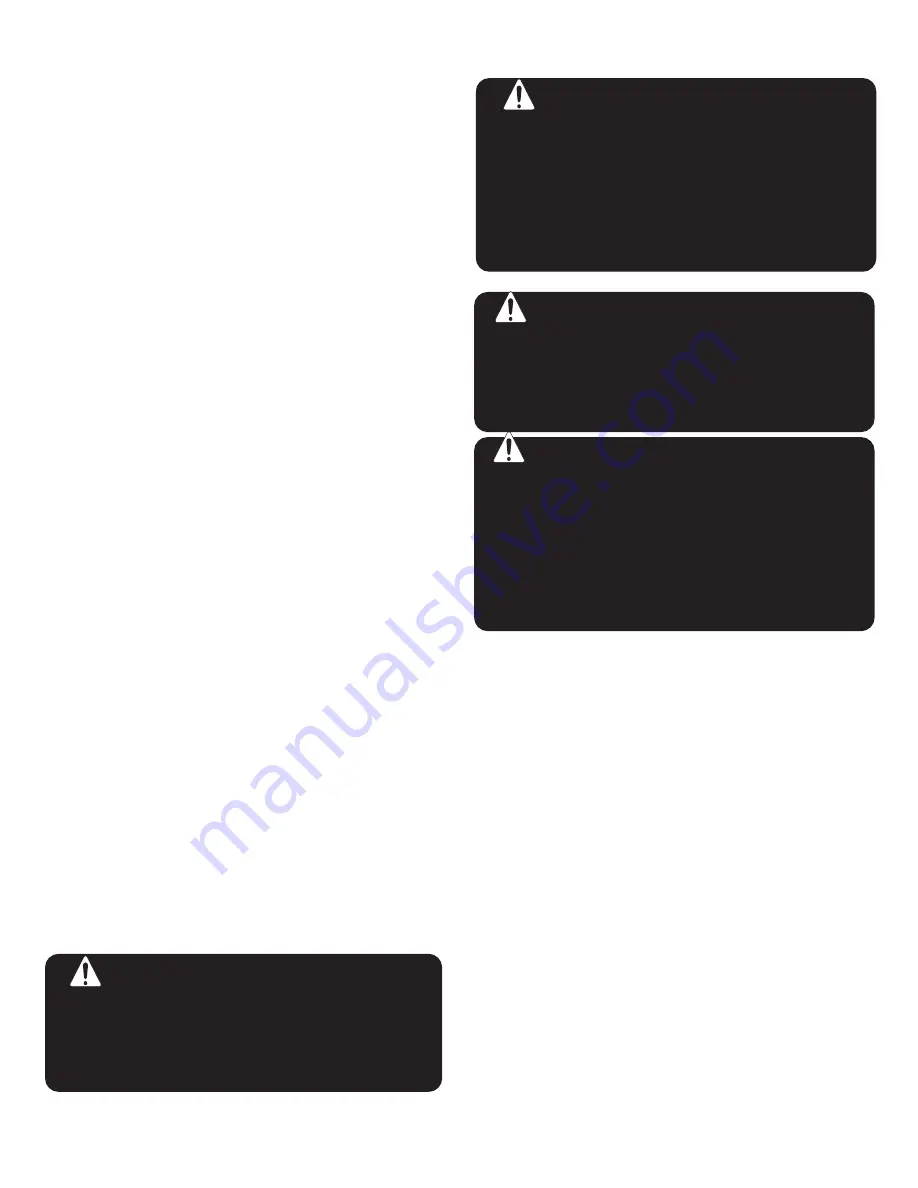
© Miller Diving All Rights Reserved Document # 030715001
16
2) Place the new Teflon washer and new packing on the
stem. NOTE: There are two different packings and
washers supplied in the kit, for rebuilding both the older
style and the newer high flow emergency valve which
is what all new Miller Helmets are equipped with. Match
the removed packing and washer to the new ones
supplied and discard the others.
3) Holding these components in place on the stem, screw
the stem into the emergency valve body.
4) Rotate the stem until it is seated all the way in.
5) Thread the packing nut onto the body. Run the nut in
and tighten slightly with a wrench.
6) Place the knob onto the stem and rotate the stem all
the way out, then back again. The rotation must be
smooth. If “hard spots” or unevenness are felt during
the rotation, the stem may be bent and could need re-
placement.
7) Tighten the packing nut with a wrench until moderate
resistance is felt when turning the knob.
8) Place the spring, and locknut onto the stem securing
the knob.
9) Tighten the locknut until it is flush with the knob. The
assembly is now complete and ready for testing.
10) Test the valve by attaching it to an emergency air
supply source. There must be no leakage of gas past the
stem or through the packing nut. Turn on the bailout bottle
and leave the supply on for several hours. There must be
no drop in pressure in the system if the valve is operat-
ing properly.
11) If the emergency valve had been removed from the
side block, ensure the pipe threads are clean and retape
with teflon tape. Wrap the pipe threads starting two
threads back, under tension, clockwise with 1
1
/
2
wraps.
Reinstall the emergency valve in the side block then re-
install the one way valve and torque to 240 inch lbs.
DANGER: Do not allow any excess Teflon
tape to cover the end of the pipe thread fittings.
Loose pieces of Teflon tape can interfere with
the performance of helmet components and
may block the diver's air supply. This could lead
to death through suffocation.
WARNING: A leaking emergency valve
assembly can cause the diver to exhaust his
entire emergency air supply (bailout) without
his knowledge. This may lead the diver to mis-
takenly assume his bailout supply is available
when it is not. This could lead to panic or
drowning in an emergency. Any worn compo-
nent that causes an emergency valve to leak
must be replaced.
CAUTION/WARNING: Never connect the
main gas supply hose from the diving station/
umbilical to the emergency valve. There is no
one way valve in the emergency valve. If this
mistake is made, any break in the supply hose
could possibly result in a “squeeze”.
WARNING: Be sure the Emergency air/
gas first stage regulator is fitted with an over-
pressure relief valve. A leaky first stage can
overpressure the hose, bursting it and causing
a loss of the entire bailout supply and possible
physical injury to the diver as the hose whips
about. Do not use a high pressure hose as the
system on the helmet is not designed for high
pressure.
3-H
SIDE EXHAUST
DESCRIPTION:
The Side Exhaust consists of the Main Body held in place
by a Retainer Plate. The Closeable Handle is secured by
a Clip Ring. The Rubber Exhaust Valve is of the mush-
room type. As a safety feature the exhaust can be fully
closed. It also serves as a buoyancy control while using
a dry suit. The primary function of the Valve is to ex-
haust gas from the main Helmet Shell when Freeflow is
used.
MAINTENANCE AND REPLACEMENT:
1. To change the Rubber Exhaust Valve it is not neces-
sary to remove the complete Side Exhaust Body from
Helmet. Remove Handle by dislodging Exhaust Clip
Ring from its retaining groove. Locate the end of the
split Exhaust Clip Ring and dislodge by poking a small
nail or sharp punch into one of the holes in the Exhaust
Body and popping it out.
2. Grasp the Rubber Exhaust Valve and pull to remove.