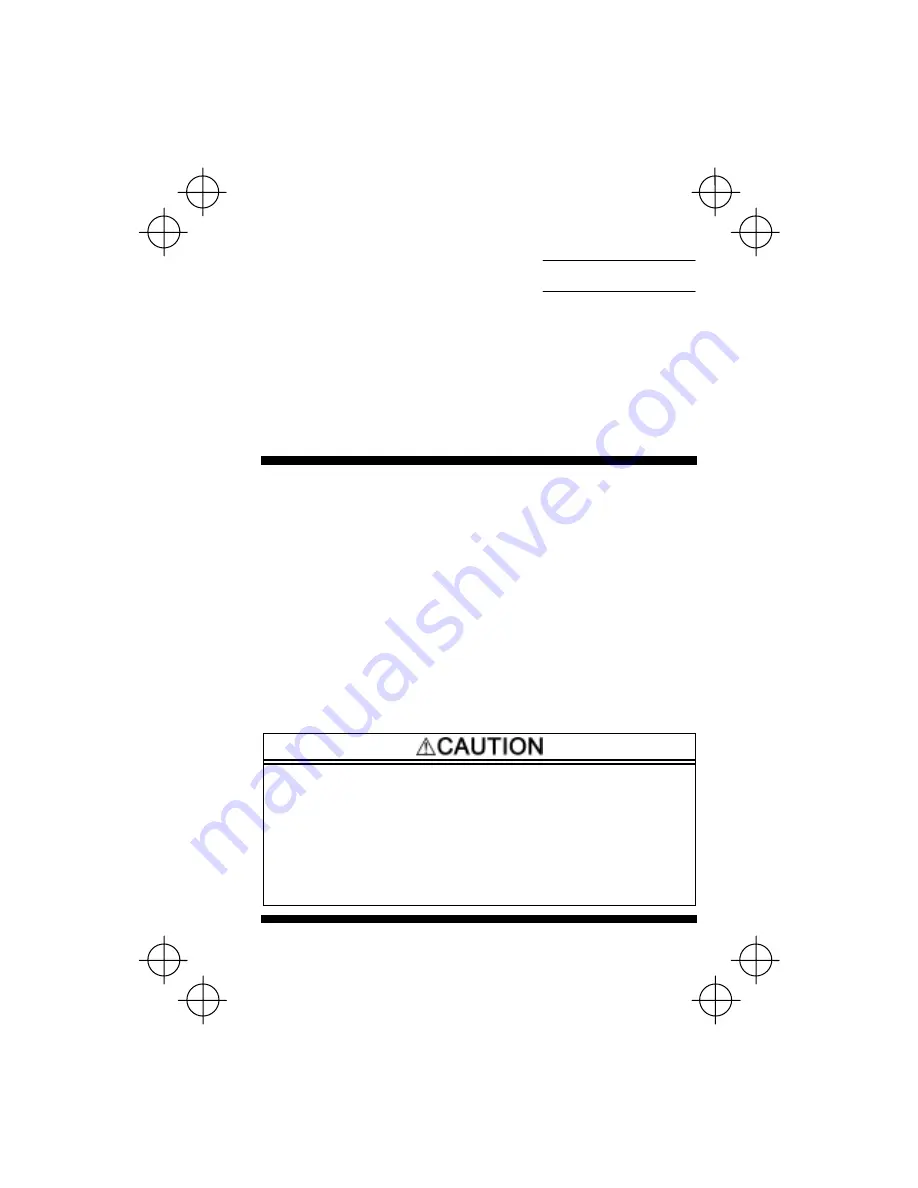
Instruction Manual
Compact Inverter
V6 series
Thank you for purchasing our V6 series of inverters.
• This product is designed to drive a three-phase induction motor. Read through this instruction
manual and be familiar with the handling procedure for correct use.
• Improper handling might result in incorrect operation, a short life, or even a failure of this
product as well as the motor.
• Deliver this manual to the end user of this product. Keep this manual in a safe place until this
product is discarded.
• For how to use an optional device, refer to the instruction and installation manuals for that
optional device.
Miki Pulley Co., Ltd.
TRS-IV-008
[ IBD#D-I-25-B ]
Содержание V6 series
Страница 16: ...xv Table of Contents Preface i Safety precautions ii Precautions for use xi How this manual is organized xiv ...
Страница 56: ...3 15 Figure 3 5 shows the status transition for Menu 1 Data setting Figure 3 5 Data Setting Status Transition ...
Страница 72: ...3 31 DC link circuit voltage Shows the DC link circuit voltage of the inverter s main circuit Unit V volts ...
Страница 75: ...3 34 Figure 3 12 Alarm Mode Status Transition ...
Страница 82: ...5 4 ...
Страница 85: ...5 7 ...
Страница 86: ...5 8 C codes Control Functions of Frequency ...
Страница 158: ...8 2 8 2 Common Specifications ...
Страница 159: ...8 3 ...
Страница 162: ...8 6 8 4 External Dimensions 8 4 1 Standard models and models available on order braking resistor built in type ...
Страница 163: ...8 7 ...
Страница 172: ...MEMO ...
Страница 173: ...MEMO ...