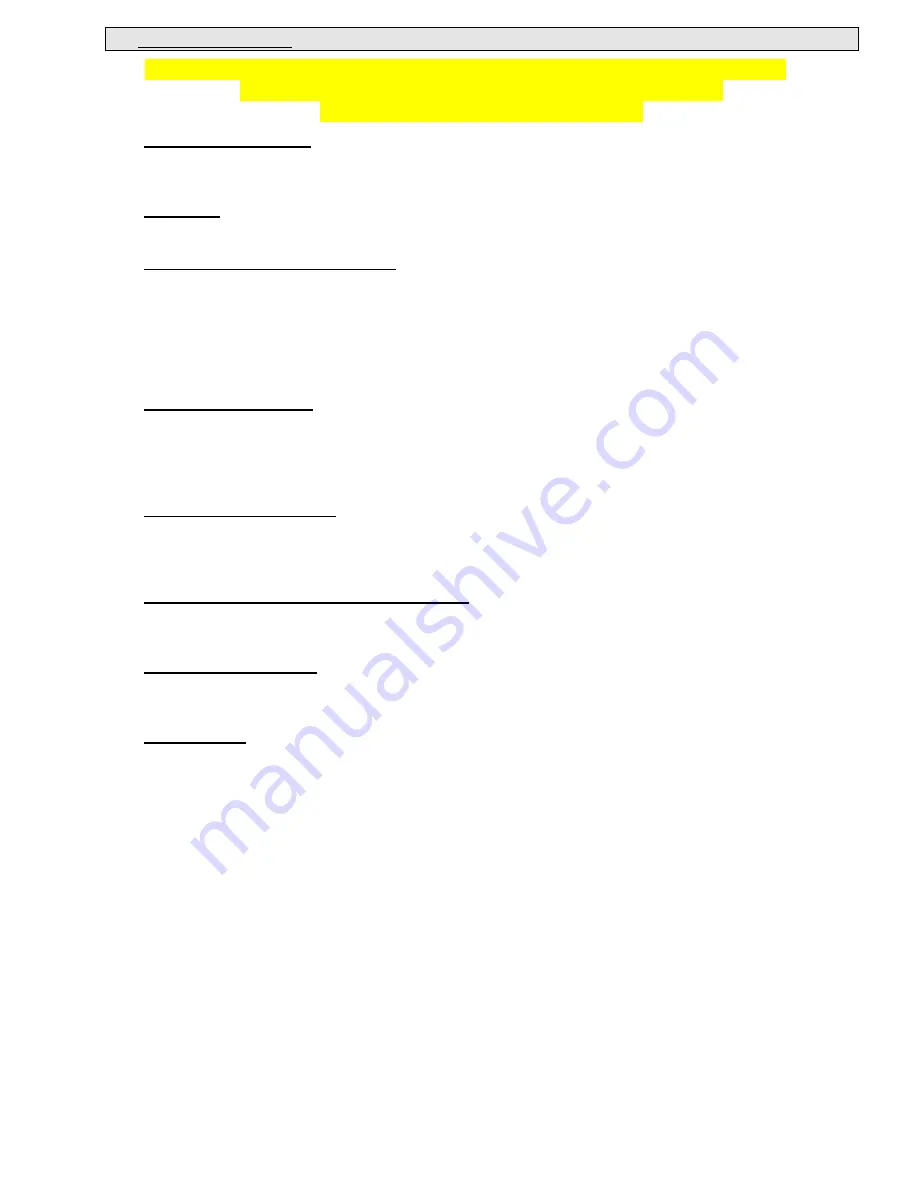
BIGHORN_March 2020.docx
March 26, 2020
Page
5 of 36
1.
BEFORE STARTING
PLEASE READ THIS GUIDE ENTIRELY BEFORE BEGINNING INSTALLATION
ALSO, READ SUPPLEMENTAL INFORMATION RELATING
TO OPTIONAL CONTROL EQUIPMENT
1.1
CRANKCASE OIL PLUG
The pump module crankcase vent has been plugged to prevent accidental oil leakage during shipment. Remove the
plug and replace with the supplied vent cap before operating pump unit. Failure to do so will cause oil leaks.
1.2
OIL LEVEL
Check that the oil level appears 1/2 way in the sight gauge or within range on the dipstick in the pump head.
1.3
INLET WATER SUPPLY PRESSURE.
When the pump module is running, it must be supplied with an inlet water supply of
NEVER LESS THAN 20 P.S.I.
(1.40 BAR)
and NEVER MORE THAN 90 P.S.I.
(6.20 BAR)
•
Inlet water supply pressure should be steady and should not be allowed to fluctuate outside of these ranges.
Failure to do so can result in damage to equipment and is not covered by warranty.
•
IF WATER PRESSURE DROPS BELOW 20 PSI, THE PUMP WILL SHUT OFF AND THE FAULT LIGHT
WILL COME ON. SEE SECTION 9
SYSTEM OPERATION
FOR FUTHER INFORMATION.
1.4
OIL CHANGE INTERVAL
The crankcase oil must be changed after the first
50 hours
of operation and from then on, once every 500 hours or
every 6 months, whichever comes first.
•
synthetic 75w-90 gear oil is recommended for all applications (mobile one or equal)
•
Secondary choice synthetic 15w-50 motor oil may be used for all applications (mobile one or equal)
1.5
HIGH PRESSURE FITTINGS
The system operates at 1,000 P.S.I. (70 bar) and should always be shut down when working on fittings or manifold
line. When adjusting the orientation of the nozzles, follow the procedures. Extreme caution should always be
exercised when working with high pressure water. Always wear safety glasses when working around fog equipment.
1.6
INLET WATER SUPPLY PLUMBING MATERIAL
Only rated and approved brass fittings or stainless steel fittings should be used to make plumbing connections. The
use of
galvanized or steel pipe fittings
can cause system failure, nozzle blockage and pump damage.
1.7
FLUSHING THE SYSTEM
Before pressurizing the system, flush all plumbing and atomization lines thoroughly to purge any residual debris.
Please refer to the startup section 7 of this manual.
1.8
TEFLON TAPE
When using Teflon tape on NPT threads, leave 1 or 2 of the starting threads showing. This will prevent pieces of
Teflon tape from entering the system, which could cause blockage or damage.
Содержание BIGHORN 1000
Страница 28: ...BIGHORN_March 2020 docx March 26 2020 Page 28 of 36 22 BIGHORN ILLUSTRATIONS...
Страница 29: ...BIGHORN_March 2020 docx March 26 2020 Page 29 of 36 22 1 BIGHORN FRONT EXTERNAL VIEW...
Страница 30: ...BIGHORN_March 2020 docx March 26 2020 Page 30 of 36 22 2 BIGHORN BACK EXTERNAL VIEW...
Страница 31: ...BIGHORN_March 2020 docx March 26 2020 Page 31 of 36 22 3 BIGHORN RIGHT EXTERNAL VIEW...
Страница 32: ...BIGHORN_March 2020 docx March 26 2020 Page 32 of 36 22 4 BIGHORN LEFT EXTERNAL VIEW...
Страница 33: ...BIGHORN_March 2020 docx March 26 2020 Page 33 of 36 22 5 BIGHORN TOP EXTERNAL VIEW...
Страница 34: ...BIGHORN_March 2020 docx March 26 2020 Page 34 of 36 22 6 BIGHORN TOP INTERNAL VIEW...
Страница 35: ...BIGHORN_March 2020 docx March 26 2020 Page 35 of 36 22 7 BIGHORN CONTROL PANEL VIEW...
Страница 36: ...BIGHORN_March 2020 docx March 26 2020 Page 36 of 36 22 8 NOTES...