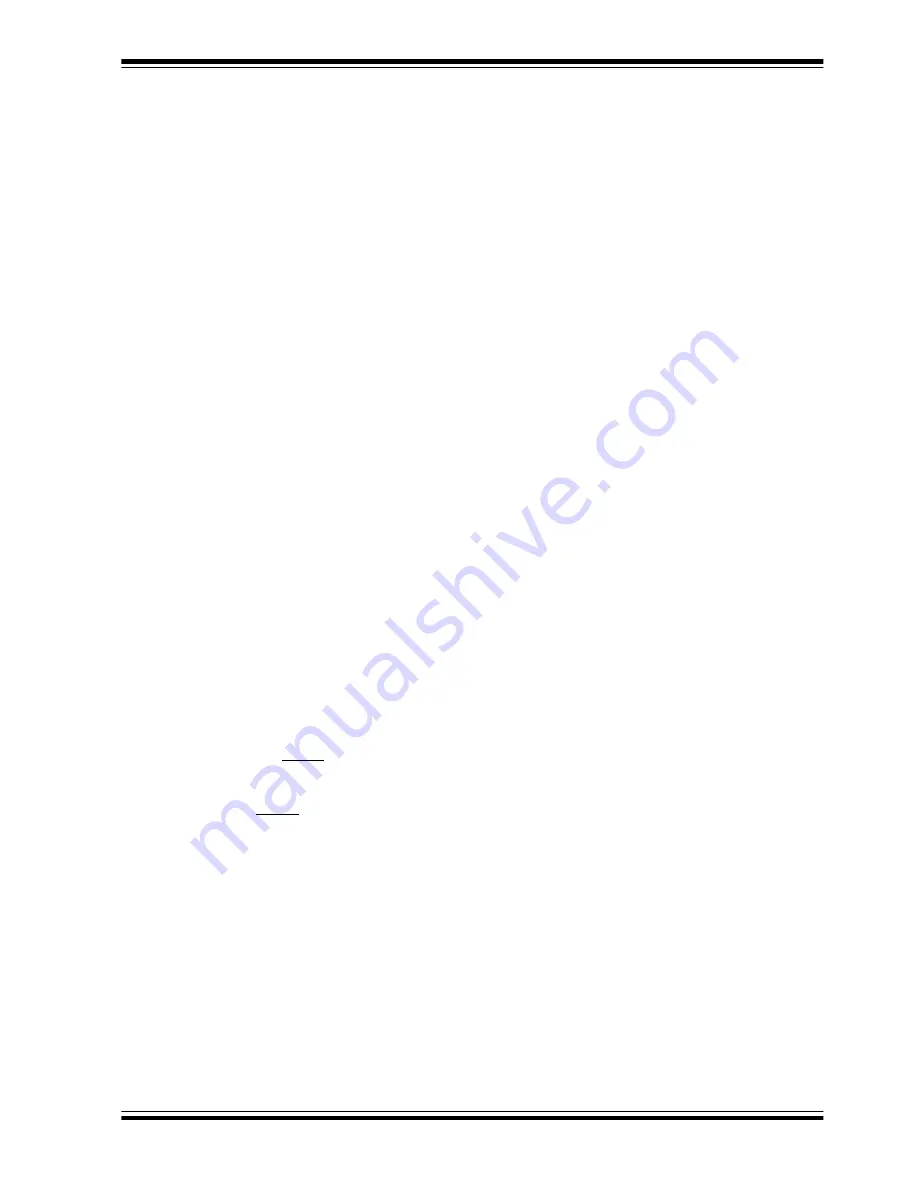
Hardware Description
2020 Microchip Technology Inc.
DS50002927A-page 31
3.2.1
dsPIC33CK256MP508 and Auxiliary Circuits
The dsPIC33CK Low-Voltage Motor Control Board features the dsPIC33CK256MP508
from Microchip’s dsPIC
®
DSC portfolio. dsPIC33C family devices implement a
100 MIPS high-performance dsPIC DSC core, and also integrate analog peripherals,
such as high-speed ADCs, op amps and analog comparators. The device also imple-
ments up to 16-channel, high-resolution Pulse-Width Modulators (PWMs) with built-in
Fault protection, triggering and synchronization features, which makes this dsPIC
device an ideal platform for the development of time-critical PMSM/BLDC motor control
applications.
The high-resolution PWM module in the dsPIC33C can generate, at specific instances,
multiple ADC triggers for measuring motor currents, phase voltages, inverter input volt-
age, total bus inverter current, etc. These feedbacks are required for implementing
motor control algorithms, such as sensor or sensorless Field-Oriented Control (FOC),
torque control, trapezoidal control, initial position detection, wind milling, flux
weakening and single-shunt current reconstruction. The PWM Control Input (PCI) of
the PWM module can be used for shutting down PWM outputs immediately when a
Fault is detected and synchronizing multiple PWM Generators (PGs) used for
controlling the three-phase inverter bridge.
The comparator module, along with the Digital-to-Analog Converter (DAC), can be
used for detecting overcurrent or overtemperature Faults to protect the inverter or
motor in case of malfunction. The dsPIC DSC has three operational amplifiers. These
can be configured by connecting an external input and feedback resistors for amplifying
currents sensed by shunt resistors.
The Change Notification (CN) feature of the I/O ports, along with the timer, can be used
for detection of Hall sensor state changes to obtain position and speed of the motor in
sensor-based BLDC motor control applications. Similarly, the Quadrature Encoder
Interface (QEI) in the dsPIC DSC can be configured to obtain the position/speed
information from the Quadrature Encoder feedbacks of the motor, which are required
for sensor-based Field-Oriented Control of PMSMs.
The dsPIC DSC also integrates several communication peripherals, such as CAN FD,
SENT, SPI, I
2
C and UART for communicating with the host PC, central controller or
master controller. Additionally, it features a Watchdog Timer, Deadman Timer, ECC
engine and BIST module required for safety-critical applications.
In the Motor Control Board, a provision is provided to mount an external crystal
oscillator to use its output as the dsPIC DSC clock input. Push button SW4 is tied to
the MCLR pin of the device and is provided to reset the dsPIC DSC. One of the
program/debug pin pairs, PGC3/PGD3, of the dsPIC device is connected to the
programmer/debugger interfaces provided on the Motor Control Board, along with
MCLR, to allow programming/debugging of the dsPIC33CK256MP508. Decoupling
capacitors are provided on all the power supply pins of the dsPIC DSC, including the
V
DD
/GND and AV
DD
/AGND pairs.
Содержание DM330031
Страница 1: ...2020 Microchip Technology Inc DS50002927A dsPIC33CK Low Voltage Motor Control Board User s Guide...
Страница 12: ...dsPIC33CK Low Voltage Motor Control Board User s Guide DS50002927A page 12 2020 Microchip Technology Inc NOTES...
Страница 54: ...dsPIC33CK Low Voltage Motor Control Board User s Guide DS50002927A page 54 2020 Microchip Technology Inc NOTES...
Страница 56: ...dsPIC33CK Low Voltage Motor Control Board User s Guide DS50002927A page 56 2020 Microchip Technology Inc NOTES...