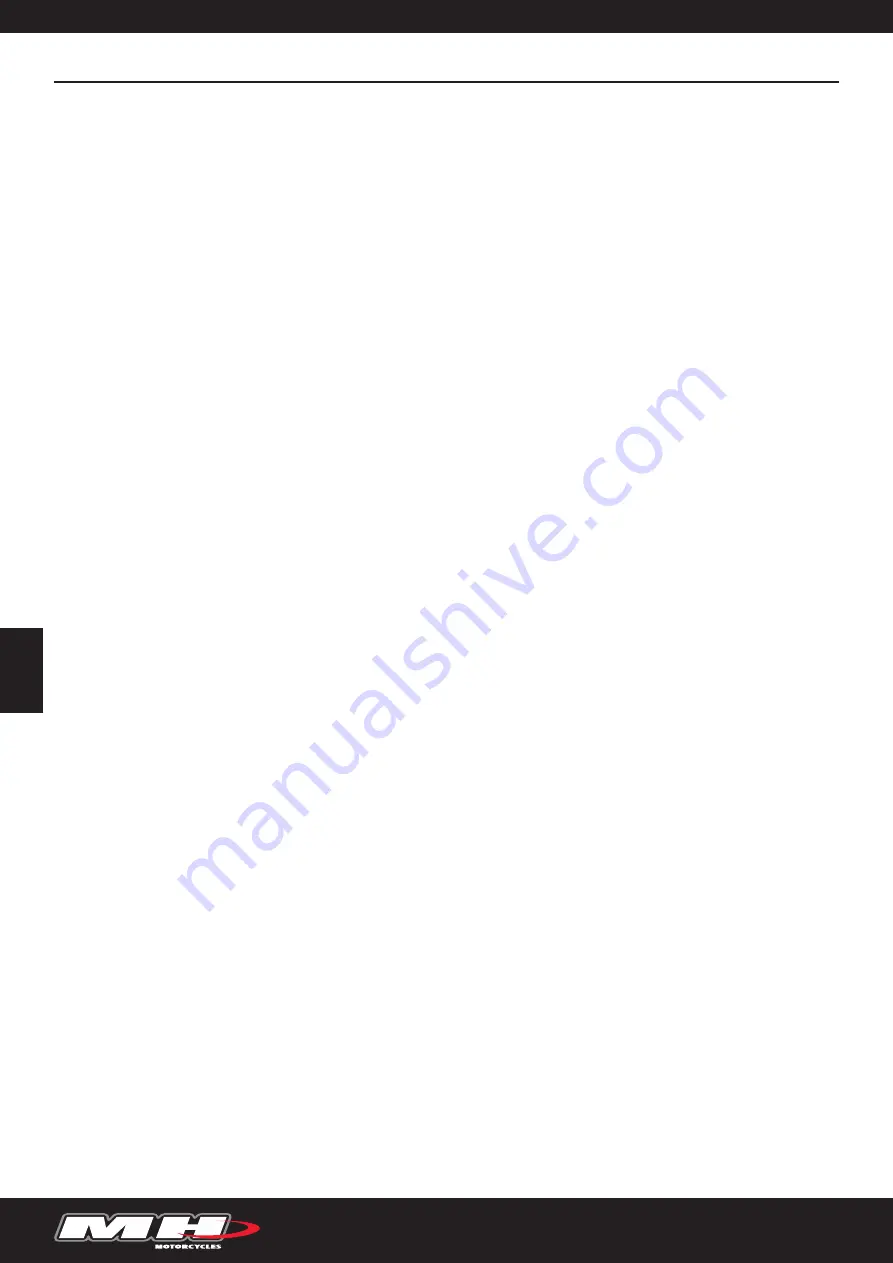
RYZ
THE GEARS JUMP
• Incorrect gear change pedal position.
• Incorrect stop lever return.
• Worn gear selector fork.
• Worn selection drum slot.
• Worn gear securing device.
FAULTY CLUTCH
THE CLUTCH SLIPS
• Clutch incorrectly fitted.
• Clutch cable incorrectly adjusted.
• Loose or fatigued clutch spring.
• Worn friction plate.
• Worn clutch plate.
• Incorrect oil level.
• Incorrect oil viscosity (low).
• Oil altered.
THE CLUTCH DRAGS
• Uneven clutch spring tension.
• Bent pressure plate.
• Bent clutch plate.
• Distorted friction plate.
• Bent clutch push bar.
• Broken clutch lobe.
• Marks not aligned.
• Incorrect oil level.
• Incorrect oil viscosity (high).
• Oil altered.
OVERHEATING
ENGINE
• Coolant passages blocked.
• Large accumulation of carbon deposits.
• Incorrect oil level
• Incorrect oil viscosity.
• Inferior oil quality.
COOLING SYSTEM
• Low coolant level.
• Radiator damaged or leaking.
• Defective radiator cap.
7-4 TROUBLESHOOTING
7
Содержание RYZ 50 Cross C
Страница 4: ...RYZ NOTES...
Страница 6: ...RYZ NOTES...
Страница 10: ...RYZ NOTES...
Страница 38: ...RYZ NOTES...
Страница 40: ...RYZ TIGHTENING TORQUE SPECIFICATIONS 5 29 SERVICING MATERIALS REQUIRED 5 29 SPECIAL TOOLS 5 30 5 2 ENGINE 5...
Страница 82: ...RYZ NOTES...
Страница 90: ...RYZ NOTES...
Страница 91: ......