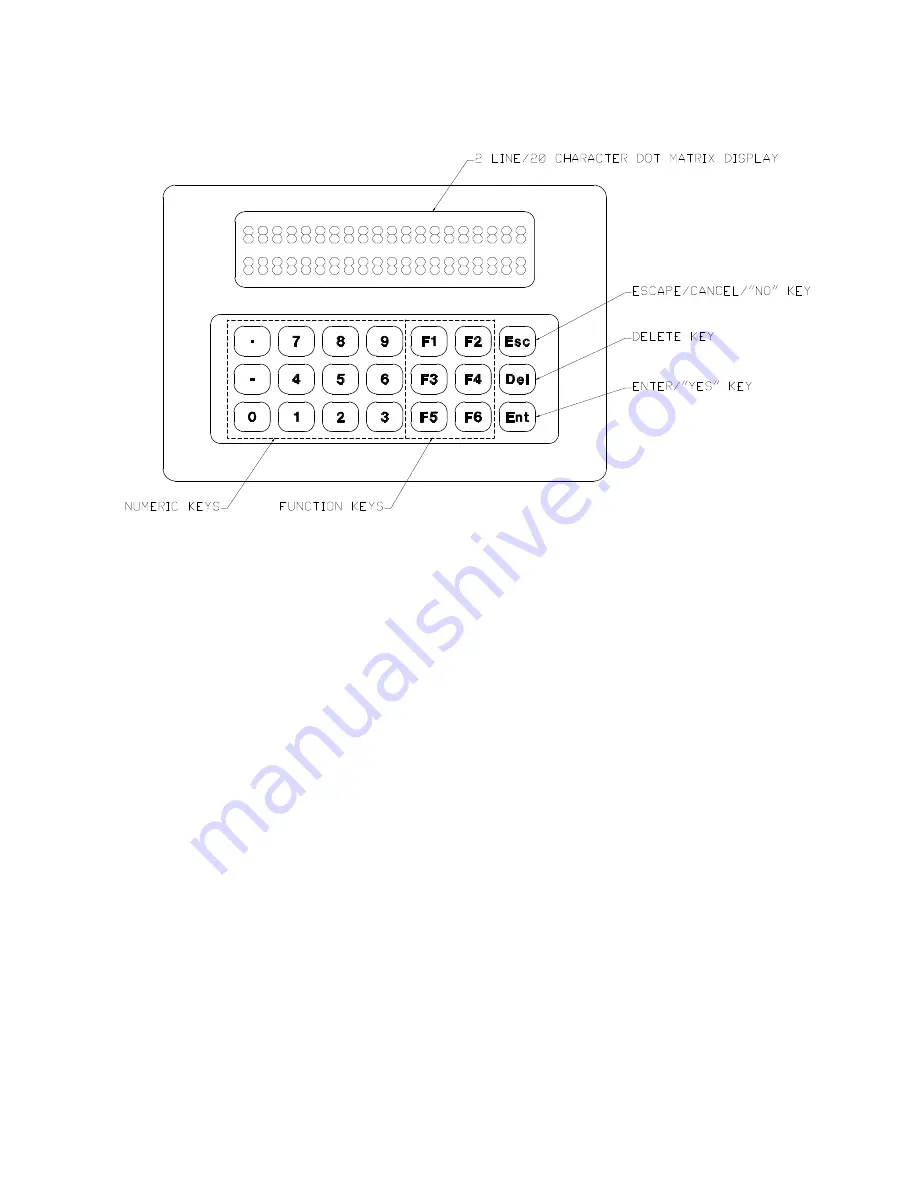
4-2 | Model 920 Multi-Gas Analyzer
Introduction to the User Interface
Figure 4-1 illustrates the layout of the analyzer User Interface.
User Interface Components
The User Interface is made up of two areas:
•
Display area
Consists of two lines, each capable of displaying up to 20 alphanumer-
ic characters. The information displayed depends on the current op-
eration mode. Messages and other information displayed is discussed
in “Messages/Information Displayed on the User Interface.”
- The top line displays the current mode of operation, or a prompt
for further keypad input.
During normal operating conditions in RUN mode, the top line
displays the names of the outputs. When operating in CALibration
or ConFiGuration mode, the mode of operation (CAL or CFG) is
also displayed.
- The bottom line displays the results of the outputs.
During normal operating conditions in RUN mode, the bottom
line continually displays the value of each output parameter being
monitored/controlled by the analyzer.
Depending on the operation mode or the command entered, other
information can also be displayed on the bottom line.
Figure 4-1.
User Interface layout.
Содержание 920
Страница 39: ...Specifications 2 11 ...
Страница 40: ...2 12 Model 920 Multi Gas Analyzer ...
Страница 41: ...Specifications 2 13 2019 02 05 ...
Страница 42: ...2 14 Model 920 Multi Gas Analyzer ...
Страница 43: ...Specifications 2 15 ...
Страница 44: ...2 16 Model 920 Multi Gas Analyzer ...
Страница 45: ...Specifications 2 17 ...
Страница 47: ...Specifications 2 19 Heater Plate ATEX and IECEx Certificates and Marking ...
Страница 48: ...2 20 Model 920 Multi Gas Analyzer ...
Страница 49: ...Specifications 2 21 ...
Страница 50: ...2 22 Model 920 Multi Gas Analyzer ...
Страница 51: ...Specifications 2 23 ...
Страница 52: ...2 24 Model 920 Multi Gas Analyzer ...
Страница 53: ...Specifications 2 25 ATEX and IECEx certified Model 920 Analyzers are marked with this label ...
Страница 54: ...2 26 Model 920 Multi Gas Analyzer Disconnect Enclosure Type 200 ATEX and IECEx Certificates and Marking ...
Страница 55: ...Specifications 2 27 ...
Страница 56: ...2 28 Model 920 Multi Gas Analyzer ...
Страница 57: ...Specifications 2 29 ...
Страница 58: ...2 30 Model 920 Multi Gas Analyzer ...
Страница 59: ...Specifications 2 31 ...
Страница 60: ...2 32 Model 920 Multi Gas Analyzer ATEX and IECEx certified Model 920 Analyzers are marked with this label ...
Страница 71: ...Installation and Start Up 3 11 Figure 3 4 Optical Bench Measuring Cell assembly ...
Страница 99: ...Installation and Start Up 3 39 Figure 3 11 Over Temp alarm reset switch SW300 Termination board ...
Страница 108: ...3 48 Model 920 Multi Gas Analyzer This page intentionally left blank ...
Страница 173: ...Controller User Interface 4 65 Figure 4 8 Customer signal connections ...
Страница 187: ...Maintenance and Troubleshooting 5 11 Figure 5 1 Measuring Cell assembly ...
Страница 211: ...Maintenance and Troubleshooting 5 35 Figure 5 5 Optical Bench Chopper Assembly Maintenance Diagram ...
Страница 226: ...5 50 Model 920 Multi Gas Analyzer Figure 5 8 Flameproof Heater Seal Assembly layout WX 14324 1A ...
Страница 227: ...Maintenance and Troubleshooting 5 51 Figure 5 9 Flameproof Heater Seal internal component layout 100 1622 1A ...
Страница 228: ...5 52 Model 920 Multi Gas Analyzer Figure 5 10 Oven Heater and Temperature Sensor wiring WX 14161 ...
Страница 243: ...Maintenance and Troubleshooting 5 67 Figure 5 13 Over temp alarm reset switch SW300 Termination board ...
Страница 262: ...A 2 Model 920 Multi Gas Analyzer Ribbon Cable Interconnect WX 102836 ...
Страница 263: ...Appendix A Drawings A 3 GP Lower Enclosure to Electronics Wiring CE Analyzers WX 102810 ...
Страница 264: ...A 4 Model 920 Multi Gas Analyzer Heater and Sensor Wiring GP Div 2 Analyzers WX 102851 ...
Страница 265: ...Appendix A Drawings A 5 Heater and Sensor Wiring CE Zone 1 Analyzers WX 102852 ...
Страница 266: ...A 6 Model 920 Multi Gas Analyzer Lower Cabinet Wiring CE GP Analyzers 120V 100 1341 3 ...
Страница 267: ...Appendix A Drawings A 7 Lower Cabinet Wiring CE GP Analyzers 240V 100 1342 3 ...
Страница 268: ...A 8 Model 920 Multi Gas Analyzer Signal Wiring PD GP Div 2 CE Zone 1 Analyzers WX 102815 ...
Страница 270: ...A 10 Model 920 Multi Gas Analyzer 15V and 5V Power Supply DC Wiring GP Div 2 CE Zone 1 Analyzers WX 102811 ...
Страница 271: ...Appendix A Drawings A 11 24V Power Supply DC Wiring CE Zone 1 Analyzers WX 102812 ...
Страница 272: ...A 12 Model 920 Multi Gas Analyzer RS 232 Communications Cable Wiring 300 9480 ...
Страница 273: ...Appendix A Drawings A 13 RS 232 RS 485 Module Wiring CE Zone 1 GP Div 2 Analyzers 100 2185 ...
Страница 274: ...A 14 Model 920 Multi Gas Analyzer Microcontroller Board 100 0117 ...
Страница 275: ...Appendix A Drawings A 15 Host Controller Board Display Interface 100 0138 ...
Страница 276: ...A 16 Model 920 Multi Gas Analyzer Model 9xx Series Analyzer Type 200 Disconnect Enclosure Details ...
Страница 278: ...S 2 Model 920 Multi Gas Analyzer This page intentionally left blank ...