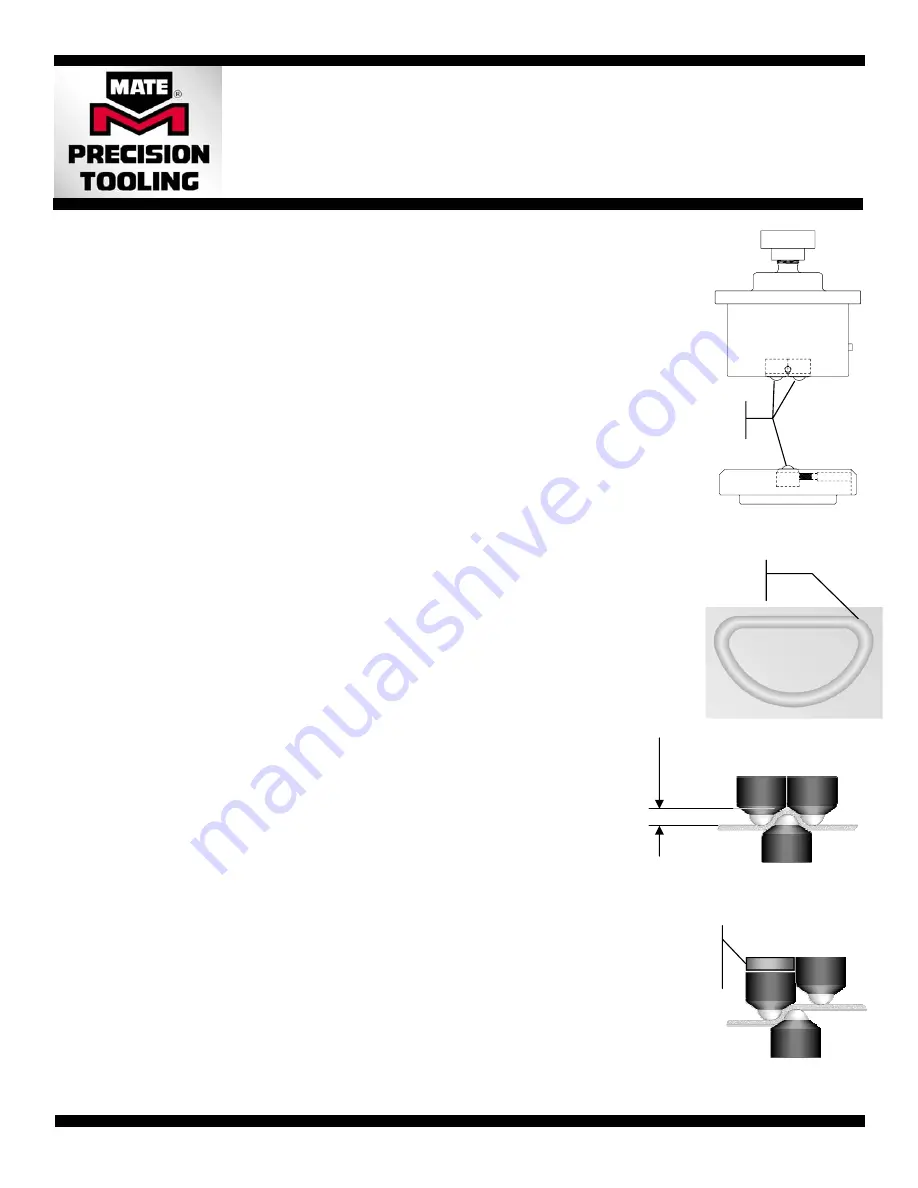
The Mate Logo is a registered trademark of Mate Precision Tooling Inc.
Dimensions in Inches(millimeters)
Mate Precision Tooling • 1295 Lund Boulevard • Anoka, Minnesota 55303 USA • Phone 763.421.0230 • 800.328.4492 • Fax 763.421.0285 • 800.541.0285
mate.com
Rollerball
®
Set-Up and Operating
Instructions for Strippit Style Tooling
Tool Set-up
1. Adjust the overall length of you Rollerball® upper assembly to 5.400" (137.16)
minus the thickness of the material to be formed.
2. Install the Rollerball assembly into the 3-1/2" auto-index station of your Strippit
style press.
Programming
1. The Rollerball tool can be programmed with an automated programming
system, by commands manually added to the program by the operator, or by a
combination of these two methods. The method used will depend upon the
make and model of the press as well as the programming software being used.
2. The intent is to move the work piece while the ram is down in a programmed
position. The alignment of the three rollerballs must be perpendicular to the
travel path.
3. Consult your programming manual for special commands and techniques
associated with rolling element tools.
4. Minimum forming radius is 0.433(11.00).
Operation
1. Before attempting to make forms with a new program, it is best to "dry run"
either by running the program without a sheet or by adjusting the ram height
setting so that the upper tool is well above the sheet during the initial run.
Carefully observe the tool orientation and ram functions in relation to the
desired result. Make programming adjustments as necessary .
2. Maximum form height is 0.144(3.70) minus the material thickness.
3. Maximum material to be worked is 0.105(2.70) mild steel.
4. Reduce the machine feed rate to achieve acceptable results. The maximum
feed rate will depend upon the material type and thickness. It is best to start
with a conservative value such as 250" (635mm) per minute.
5. For best results clean the work piece of any foreign matter or debris before
attempting to roll forms into it.
Maintenance
1. Keep the rollerballs free of excessive grit build up. Periodically clean the
rollerballs with a lint free cloth soaked with a light lubricating oil.
2. The maintenance interval will depend upon the conditions of use.
Rollerball Offset Forming
1. Loosen the two set screws retaining the upper Rollerball inserts and replace
one with the shorter Rollerball offset forming insert. Install and adjust the tool
using the same method as described for standard Rollerball forms.
2. For shallower offset forms, install tbe offset adjustment shims under the offset
rollerball insert to change the height of the offset rollerball.
3. Continuous offset forms (circles and rectangles with radiused corners) can be
used to create large embosses in the upward or downward direction, depending
upon the position of the offset rollerball insert in relation to the machine travel
path.
Configuration for
Bead Forming
Maximum
Form Height
0.433(11.00)
Minimum Radius
Configuration for
Offset Forming
Offset
Adjustment
Shim
Rollerball®
Inserts x3