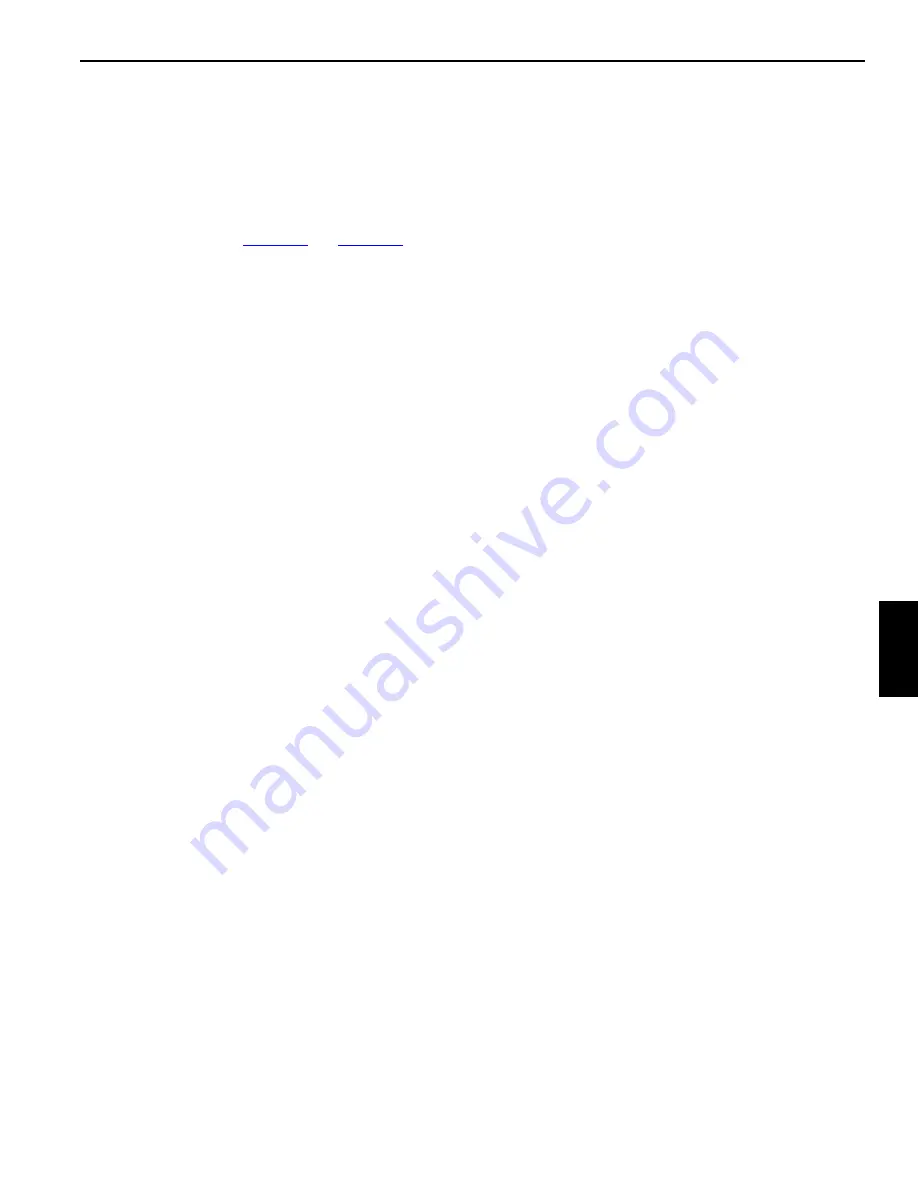
Reference
Only
Manitowoc
Published 09-09-16, Control # 229-09
6-1
MLC650 SERVICE/MAINTENANCE MANUAL
SWING SYSTEM
6
6
SECTION 6
SWING SYSTEM
GENERAL
This section provides the hydraulic and electrical information
for the crane’s swing system. Hydraulic and electrical circuit
schematics are provided (
).
Details of individual components are covered later in this
section. Component information can also be found in the
following sections of the Service Manual:
•
Section 2: Hydraulics
•
Section 3: Electrical
SWING SYSTEM OVERVIEW
The swing system is a closed-looped system consisting of an
engine-driven hydraulic pump and two hydraulic motors or
three hydraulic motors, if the crane is equipped with the
VPC-MAX™ option.
The swing pump is an electronically controlled, bi-directional,
variable-displacement pump that provides hydraulic flow to
the swing motors.
The swing motors are bi-directional fixed-displacement type
of motors mounted on the planetary swing drives. The
planetary swing drives are mounted onto the adapter frame.
To swing the crane, each swing motor rotates a pinion gear
located on the corresponding planetary swing drive. The
pinion gear meshes with a ring gear that is attached to the
carbody, causing the adapter frame (and rotating bed) to
rotate relative to the carbody.
The speed of the swing motors is proportional to the output
flow volume of the swing pump that is controlled by the
position of the J1 joystick.
The J1 joystick left-right position determines the crane’s
swing direction and speed. The J1 joystick also has a
momentary contact switch to control the swing brake.
The J1 joystick communicates with the crane’s control
system using the controller area network bus (CAN Bus).
NOTE:
The J1 joystick has no external locations where
voltages can be checked.
Swing speed and swing torque can be selected for the type
of work being performed from the speed and torque limits
screen on the main display (see the MLC650 Main Display
Operation F2267).
SWING BRAKE OPERATION
The swing brake is a spring-applied, hydraulically released
brake system located between each swing motor and its
corresponding planetary drive. If the brake hydraulic
pressure or electrical control is lost, the brake is applied by
spring force.
The swing brake release system uses charge pressure from
the swing pump, supplied to the swing brake solenoid valve.
The brake release pressure must be at least 18 bar (261 psi)
to fully release the brakes. If the pressure is less than 18 bar
(261 psi), the brakes could remain partially applied, which
could damage the swing brake system.
Swing Park Switch Control
The J2 joystick sends a 24 V
DC
output to the swing park
switch. When the swing brake switch is at the UN-PARK
position, the swing park switch is closed, sending a 24 V
DC
signal back to the J2 joystick.
The J2 joystick communicates
the un-park brake command
to the IOLC30 control module via the CAN Bus. The IOLC30
control module then sends a 24 V
DC
output to the swing
brake release solenoid valve, energizing the solenoid. The
solenoid valve shifts position, routing hydraulic fluid to the
swing brake cylinders, releasing the brakes.
When the swing brake switch is moved to the ON-PARK
position, the swing park switch is open, sending a 0 V
DC
signal back to the J2 joystick.
The J2 joystick communicates
the on-park brake command
to the IOLC30 control module via the CAN Bus. The IOLC30
control module then sends a 0 V
DC
output voltage to the
swing brake release solenoid valve, de-energizing the
solenoid. This causes the solenoid valve to return to the
default position, allowing the hydraulic fluid in the brake
cylinders to flow back to the tank. The reduced hydraulic
pressure allows spring force to apply the brake.
Momentary Swing Brake Control
When the momentary swing brake button is pressed on the
J1 joystick, the joystick communicates
the brake command
to the IOLC30 control module via the CAN Bus. The IOLC30
control module then sends a 0 V
DC
output voltage to the
swing brake release solenoid valve, de-energizing the
solenoid. This causes the solenoid valve to return to the
default position, allowing the hydraulic fluid in the brake
cylinders to flow back to the tank. The reduced hydraulic
pressure allows spring force to apply the brake.
Содержание MLC650
Страница 1: ...R e f e r e n c e O n l y Service Maintenance Manual Manitowoc MLC650 ...
Страница 2: ...R e f e r e n c e O n l y ...
Страница 4: ...R e f e r e n c e O n l y THE ORIGINAL LANGUAGE OF THIS PUBLICATION IS ENGLISH ...
Страница 375: ...R e f e r e n c e O n l y ...
Страница 376: ...R e f e r e n c e O n l y ...