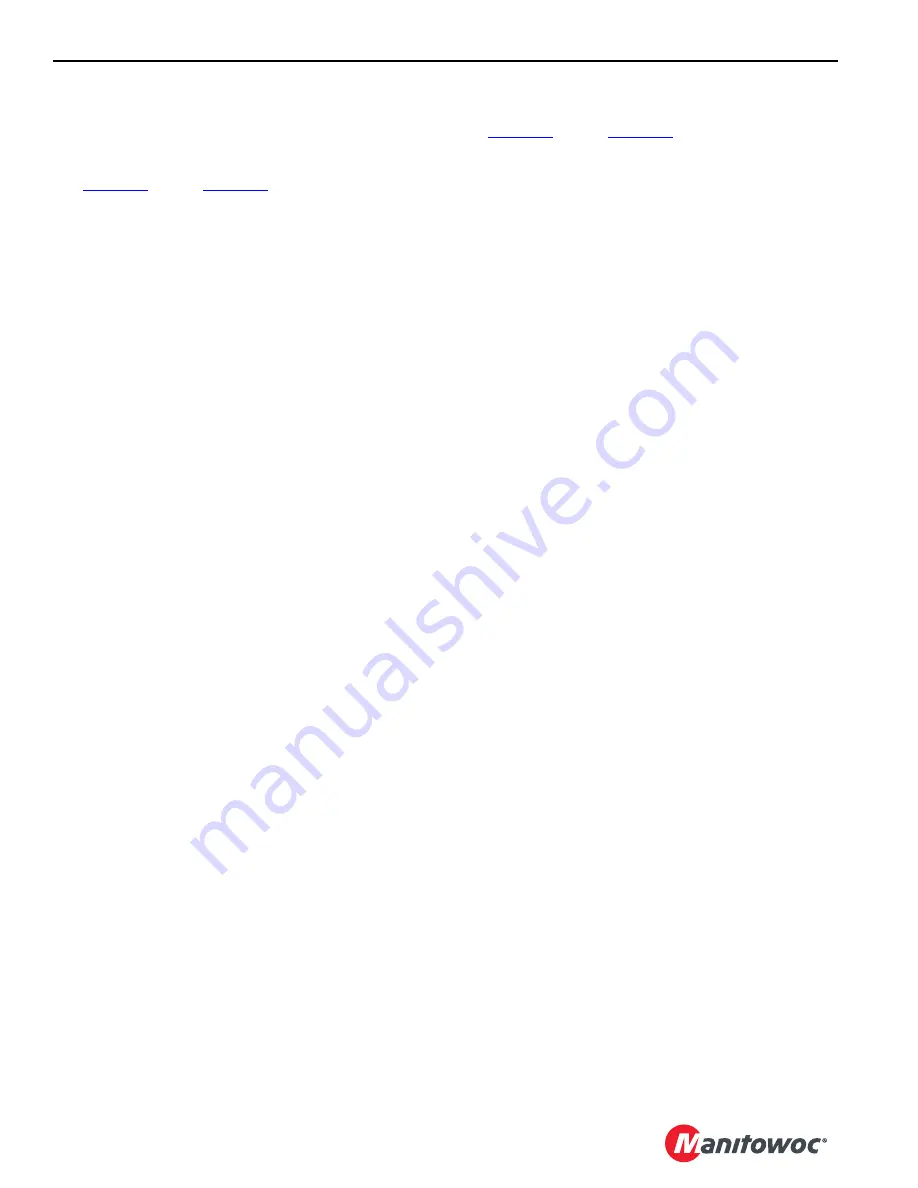
HOISTS
MLC150-1 SERVICE/MAINTENANCE MANUAL
5-2
Published 03-21-2021, Control # 264-01
NOTE:
In the following instructions,
CCS
stands for
C
rane
C
ontrol
S
ystem.
ALL DRUMS
.
Seat Switch
The operator must be seated to close the seat switch before
the drums can be operated.
The CCS disables the drum control handles and prevents
the drum brakes from being released (spring applied) until
the seat switch is closed.
Drum Brake
Each drum is equipped with a spring-applied, hydraulically-
released disc brake located between the motor and the drum
gear box. The brakes are controlled by 2-position solenoid
valves that receive oil flow from the pilot pump.
The un-parked switch for the desired drum must be pressed
before the drum can be operated.
The CCS disables the drum control handle and prevents the
drum brake from being released (spring applied) or the pawl
from being disengaged (Drums 2 and 4) until the un-parked
switch is closed.
The point at which a drum brake releases or applies in
response to control handle movement is determined by the
CCS. When the control handle is moved off center, a signal is
sent to the brake solenoid. The solenoid then opens a
hydraulic valve to allow pressure to release the brake. When
the control handle is moved back to center and the controller
sees zero pressure for a set amount of time, the brake
applies.
Brake Release
All load hoists utilize a pressure memory routine to control
drum brake release in order to provide smooth brake release
without any load droop. The CCS remembers the load-
induced pressure from the last hoist cycle and operates the
pump and control valve such that the pressure in on the
raising side of the hoist is increased to nearly this stored
value before releasing the drum brake and starting drum
movement.
Speed Sensor
When a drum motor rotates, a sensor mounted on the motor
sends an input voltage to the designated controller. The
controller in turn sends corresponding voltage pulses to the
rotation indicator (thumper solenoid) in the drum control
handle. The rotation indicator pulsates with a varying
frequency to indicate drum rotational speed. The direction of
rotation is also displayed on the main display via an arrow on
the corresponding drum icon.
DRUMS 1 AND 2
.
Overview
The hydraulic circuit for each drum consist of an open loop
pump which contains a 130 cc rotary group, an electrically
operated directional control valve, and a 171,8 cc variable
displacement motor with holding valve and internal relief
valve.
The control signals to these hydraulic elements are
determined by the CCS, which uses a number of inputs to
determine speed, direction, and brake release commands.
Drum 2 Pawl
The Drum 2 pawl is controlled by a 3-position solenoid valve
that receives oil flow from the pilot pump.
When the Drum 2 park switch is in the parked position, the
CCS shifts the pawl valve to the position that extends the
pawl cylinder (rotates cam away from pawl), allowing the
pawl to spring engage the drum ratchet.
When the Drum 2 park switch is in the un-parked position,
the CCS shifts the pawl valve to the position that retracts the
pawl cylinder, allowing the cam to disengage the pawl from
the drum ratchet.
Holding Valve
A holding valve is attached to each motor. The purpose of
the valve is to:
•
Ensure that the hoist powers down properly
•
Hold the load when the control handle is in center
•
Ensure smooth starts, stops, and changes in hoist
speed
•
Relieve momentary excess pressure that may occur
when bringing a heavy load to a quick stop.
The valve functions differently in each direction:
Lowering Load
When flow is in the
down
direction, the holding valve
functions as a hydraulically operated proportional spool
valve which checks motor outflow in one position and in the
other position allows motor outflow.
When there is no working pressure (handle in center), a
check valve stops hydraulic flow in the return side of the
down
circuit. This prevents the hoist motor from turning in
the
down
direction.
As the control handle is moved off center in the
down
direction, the working pressure begins to act on the valve,
which begins to shift to the unchecked position to allow
motor outflow. When the control handle is moved toward
REFERENCE
ONLY
Содержание MLC150-1
Страница 1: ...Service Maintenance Manual Manitowoc MLC150 1 R E F E R E N C E O N L Y ...
Страница 2: ...R E F E R E N C E O N L Y ...
Страница 4: ...THE ORIGINAL LANGUAGE OF THIS PUBLICATION IS ENGLISH R E F E R E N C E O N L Y ...
Страница 98: ...MLC150 1 SERVICE MAINTENANCE MANUAL 5 iv Published 03 21 2021 Control 264 01 R E F E R E N C E O N L Y ...
Страница 205: ...R E F E R E N C E O N L Y ...
Страница 206: ...R E F E R E N C E O N L Y ...