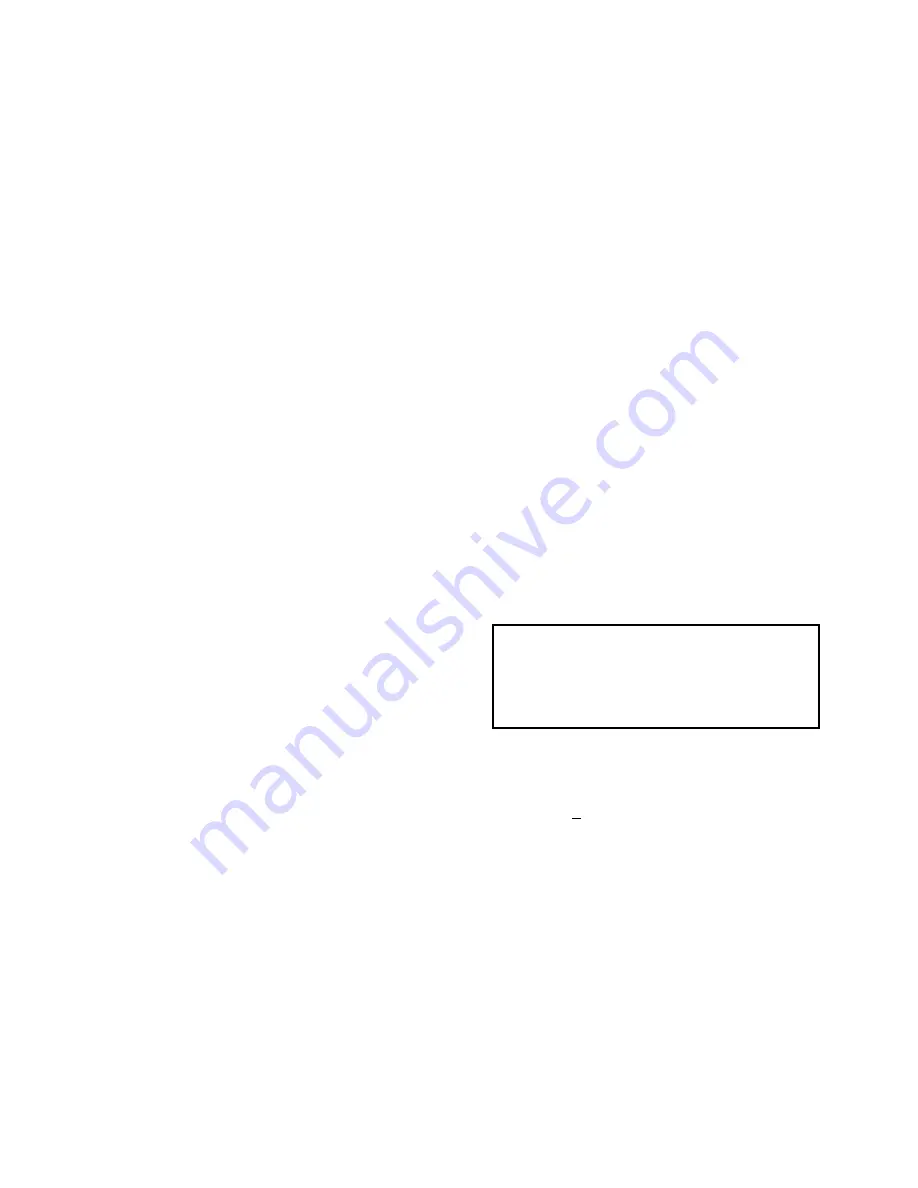
INSTALLATION
26
Electrical Hook up
Ensure that wire size and disconnect devices
conform to the installation contractor’s
drawings and to all applicable codes.
Power Connections
The three phase input power to the drive is
fuse protected internal to the Drive. However,
it is recommended to provide branch circuit
protection by means of a circuit breaker in
accordance with the National Electrical Code,
(USA) or as may be required by other local
electrical codes.
Signal Connections
All low power, low voltage wiring to the DSD
412 controller should be run separate from the
115VAC or higher power connections and the
DC motor armature and field connections.
These include:
Encoder Wiring
Speed Reference Wiring
Pre-Torque Reference Wiring
24 VDC Logic Inputs
Analog Outputs
Open Collector Logic Outputs
Rewiring these signals in shielded wire is
recommended to avoid noise pickup.
Grounding
The DSD 412 controller, the utility power
system feeding it and all other connected
power equipment should be grounded as
follows:
•
The facility power ground and grounding
wire sizes should comply with NEC, UL,
CSA and other applicable codes for power
distribution safety.
•
A common grounding stud or buss bar
should be provided within the drive
enclosure cabinet, electrically bonded to the
metal enclosure.
•
A grounding wire should be provided
directly from the grounding terminal on the
DSD 412 drive chassis to the common
grounding stud.
•
A grounding wire should be provided
directly from the electrical sub-panel on
which the DSD 412 drive is mounted to the
common grounding stud. Other electrical
equipment, such as fans or relay circuits
may be grounded to the electrical sub-
panel.
•
A grounding wire should be provided
directly from the elevator motor frame to the
common grounding stud.
•
A grounding wire should be provided
directly from the power isolation transformer
frame to the common grounding stud.
•
A grounding wire should be provided
directly from building steel to the common
grounding stud.
•
If an armature circuit ripple filter is used, a
grounding wire should be provided directly
from the ripple filter inductor frame to the
common grounding stud. The sub-panel for
capacitor mounting within the filter should
have a grounding wire to the inductor frame.
•
The secondary side of the power isolation
transformer should remain un-grounded.
•
The low voltage circuit common should be
grounded by connecting A1TB1-43 or
A1TB1-44 to A1TB11.
Pre-power Check
CAUTION
TO PREVENT DAMAGE TO THE DRIVE,
THE FOLLOWING CHECKS MUST BE
PERFORMED BEFORE APPLYING THE
INPUT POWER.
A. Inspect all equipment for signs of damage,
loose connections, or other defects.
B. Ensure the three-phase line voltage is
10% of the nominal input voltage
range of 150 to 525 VAC. The drive is not
sensitive to phase sequence. Input power
specifications are contained on the drive
nameplate or the drive system Schematic
Diagram.
C. Remove all shipping devices and relay
wedges. Manually operate all contactors
and relays to ensure that they move
freely.
D. Ensure that all electrical connections are
secure.
E. Ensure that all transformers are connected
for proper voltage according to the Drive
system Interconnection Diagram.
Содержание DSD 412
Страница 1: ...DSD 412 DC Elevator Drive Technical Manual CS00407 rev 06...
Страница 6: ...6...
Страница 102: ...MAINTENANCE 102 Figure 24 Connector and E prom Locations...
Страница 103: ...MAINTENANCE 103 Figure 25 Test Point Locations...
Страница 115: ...OUTLINE DRAWING 100A 115 Figure 26 Drive Chassis Outline DSD 412 100 Amp...
Страница 116: ...OUTLINE DRAWING 190A 116 Figure 27 Drive Chassis Outline DSD 412 195 Amp...
Страница 117: ...OUTLINE DRAWING 300A 117 Figure 28 Drive Chasis Outline DSD 412 300 Amp...
Страница 118: ...LAYOUT DRAWING 100A 118 Figure 29 Layout DSD 412 100 Amp A3 A1 A2 A2 L1 NEG GND L2 L3 POS...
Страница 119: ...LAYOUT DRAWING 195A 119 Figure 30 Layout DSD 412 195 Amp A3 A1 A2 A2...
Страница 120: ...LAYOUT DRAWING 300A 120 Figure 31 Layout DSD 412 300 Amp A3 A1 A2 A2...
Страница 121: ......