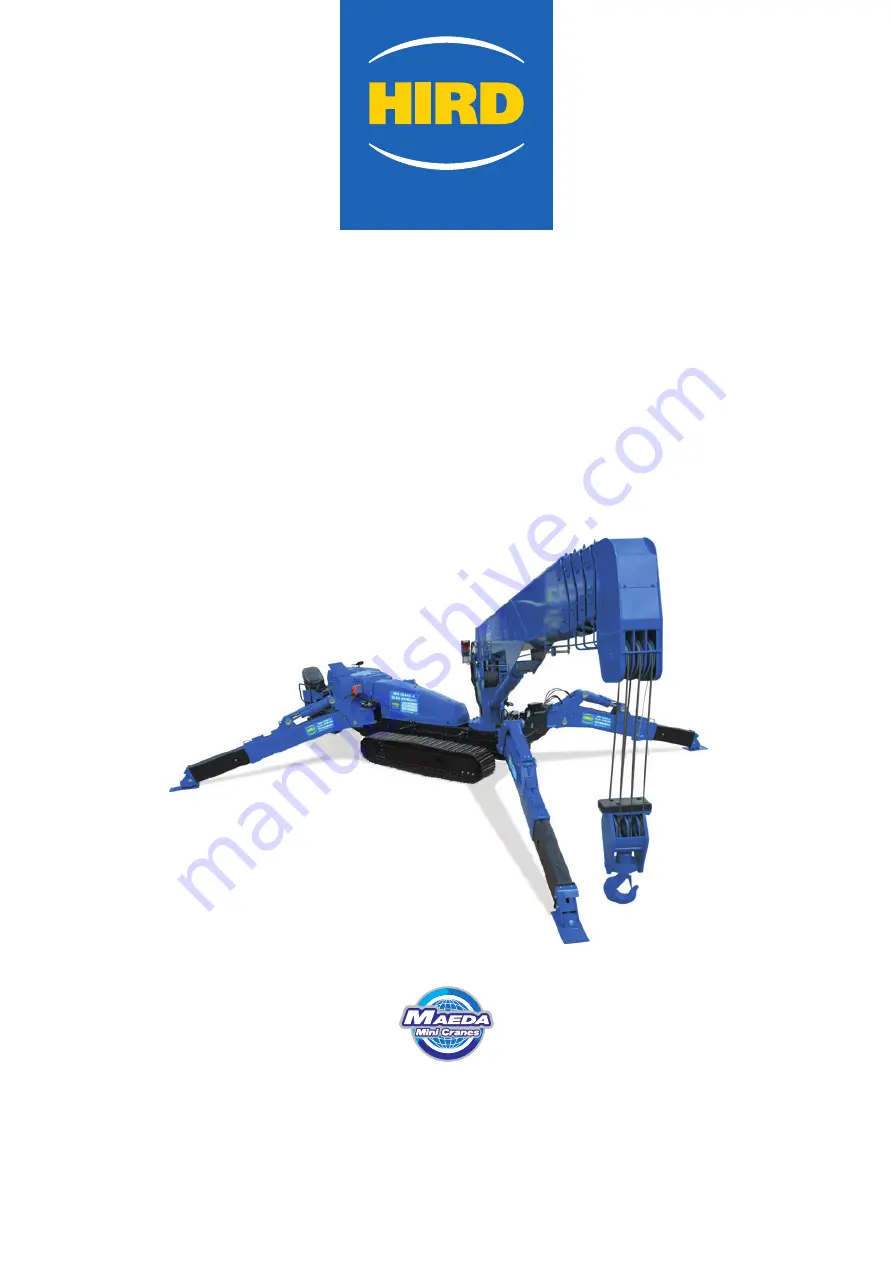
OPERATORS MANUAL
MAEDA MINI CRANE
MC815
www.hird.co.uk
DISCLAIMER - ALL INSTRUCTIONS ARE SUPPLIED FROM MANUFACTURER AND WHERE CORRECT AT TIME OF PRINT
OM 1704-2
Northern
(Head Office)
Tel: +44 (0)1482 227333
Western
Tel: +44 (0)1384 900388
Southern
Tel: +44 (0)203 174 0658
Central
Tel: +44 (0)1302 341659
Содержание HIRD MC815
Страница 29: ...20 This Page Intentionally Left Blank ...
Страница 72: ...63 3 Total load chart 106 2186300 ...
Страница 74: ...65 9 Precautions when using 106 2186600 ...
Страница 75: ...66 ...
Страница 81: ...72 This Page Intentionally Left Blank ...
Страница 196: ...187 Remote control menu ...
Страница 253: ...244 This Page Intentionally Left Blank ...
Страница 313: ...304 ...
Страница 337: ...328 This Page Intentionally Left Blank ...
Страница 342: ...333 2 SPECIFICATION DIMENSIONAL DRAWING ...
Страница 343: ...334 3 DIMENSIONAL DRAWING OF OUTRIGGER WIDTH ...
Страница 356: ...347 5 WORKING RADIUS LIFTING HEIGHT ...
Страница 361: ...352 1 Diagram of fly jib working range chart 106 2189200 ...
Страница 396: ...387 9 4 WORKING RADIUS LIFTING HEIGHT ...
Страница 397: ...388 This Page Intentionally Left Blank ...
Страница 401: ...392 1 Searcher hook working range diagram 106 2189200 ...
Страница 402: ...393 6 Maximum rated total load 106 4716100 2 locations 7 Notice on pin holes CL000100001 2 locations ...
Страница 423: ...414 9 4 WORKING RADIUS LIFTING HEIGHT ...