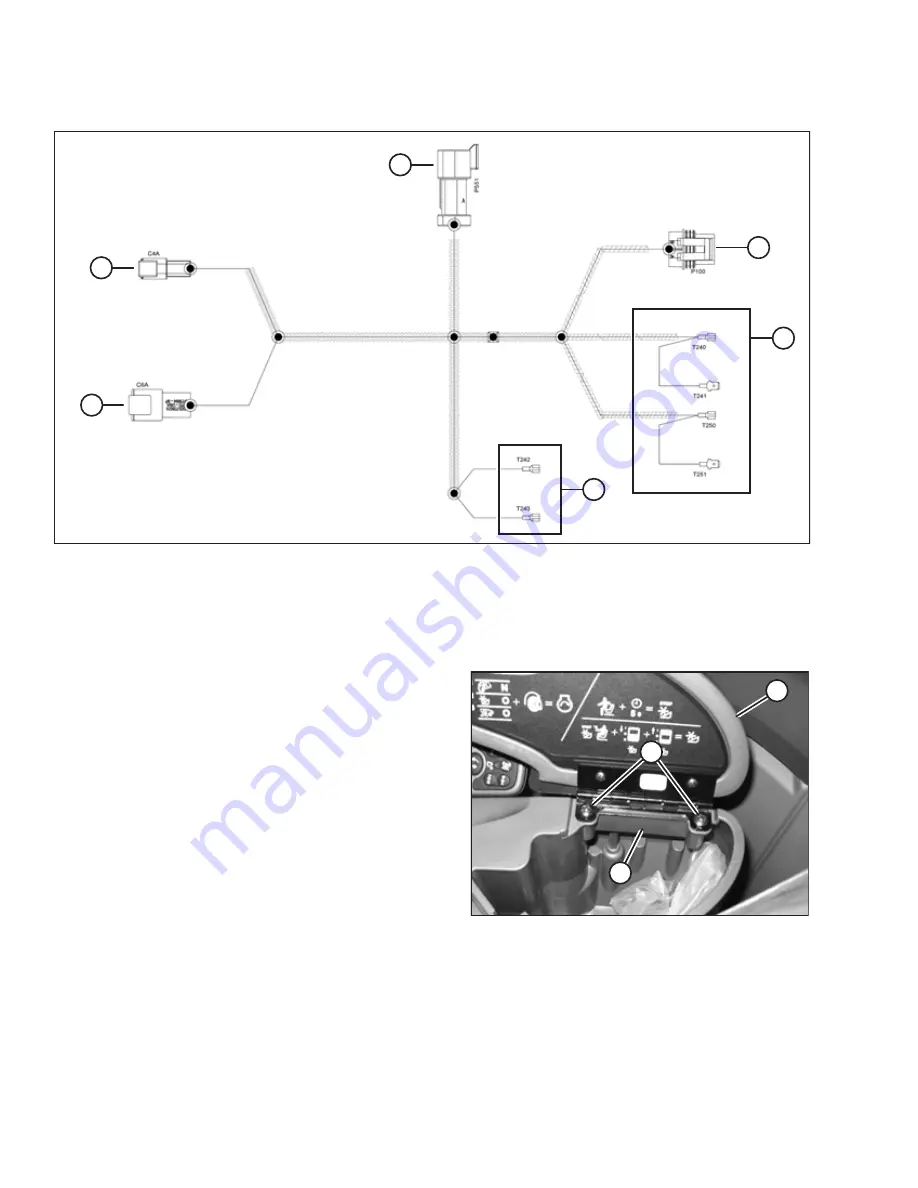
215184
236
Revision A
Figure 7.73: Cab Draper Control Harness (MD #304210)
1027102
A
B
C
D
E
F
A - Terminals Connect to Rocker Switch
B - Terminals Connect to Auxiliary Power Outlet Strip
C - P551 Connects to Speed Control Rheostat
D - C4A Connects to C4B on Harness (MD #304211)
E - C6A Connects to C6B on Harness (MD #304211)
18. If the In-Cab Side Draper Speed Control kit has been installed, connect connector P551 to the speed control rheostat. If
the In-Cab Side Draper Speed Control kit has not been installed, leave connector P551 unconnected.
1008184
C
A
B
Figure 7.74: Support Position on Console
–
S6 and
T6 Series Combines
19.
S6 and T6 Series combines only:
Position rocker switch
support (C) onto console and align the holes in the support
with the holes in the console.
20.
S6 and T6 Series combines only:
Reinstall cover (B) and
secure in place with existing screws (A).