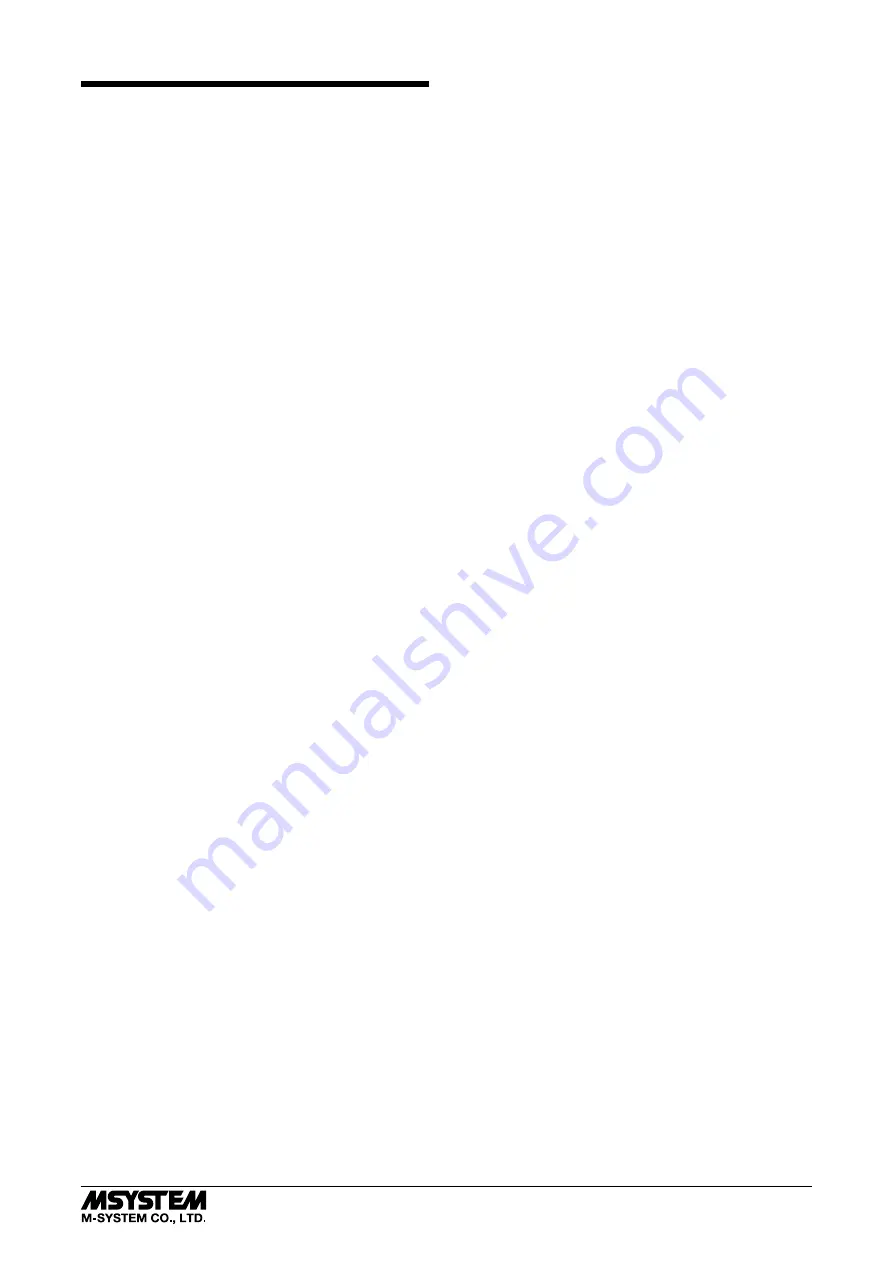
MSP40 / MSP50
5-2-55, Minamitsumori, Nishinari-ku, Osaka 557-0063 JAPAN
Phone: +81(6)6659-8201 Fax: +81(6)6659-8510 E-mail: [email protected]
EM-4883 P. 3 / 18
2. POINTS OF CAUTION
■
POWER INPUT RATING & OPERATIONAL RANGE
• Locate the power input rating marked on the product and
confirm its operational range as indicated below:
24V DC: 24V rating ±10%, approx. 0.6A
■
HUNTING
• Hunting is a condition in which the output stem is os-
cillated repeatedly and persistently without settling at a
single position.
• The actuator unit must operate at an average duty cycle
of 50% (approx. 13 strokes per minute) or less.
■
GENERAL PRECAUTIONS
• Remove the power supply to the actuator before wiring
the unit.
• DO NOT install signal wires and power supply wires to-
gether in one duct because it may cause a malfunction
due to induction noises. Alternatively, use shielded cables
for the input signal wires to prevent interference from
such noises.
• If input signals are to be turned on/off with power sup-
plied to the actuator, be sure to specify the output stem
operation for when abnormally low input is detected.
• DO NOT loosen the screws fixing the potentiometer in-
side the unit.
■
INSTALLATION
• Indoor, or outdoor where the unit is NOT exposed to di-
rect sunlight.
• Operating temperature -5 to +55°C (23 to +131°F)
• Operating humidity 30 to 85% RH (non-condensing)
• The unit is not designed to withstand all vibrations.
M-System does not guarantee long-term use of the unit
even with small vibrations. Please use the unit only after
evaluating in an actual installation environment. Par-
ticularly, avoid using under the condition where valve
cavitation or water hammer is likely to occur.
• Install the unit where it can be reached for maintenance
and inspection. Be sure to allow at least 20 cm (7.9 inch-
es) clearance above the unit and around the terminal box.
• Keep away from hazardous atmosphere such as explosive
or corrosive gases.
■
PID CONTROL SIGNAL
• Choose PID parameters carefully so that the MV remains
as stable as possible to prevent hunting. Unstable control
shortens the life of actuator and valve.
■
REATTACHING TERMINAL BOX COVER
• When reattaching the terminal box cover after wiring,
make sure that the O-rings are securely in place.
■
SCREW TORQUE
• The torque for tightening screws for the terminal cover is
between 1.2 – 2 N·m (0.89 – 1.5 ft·lbf). The screws must
be tightened evenly and crosswise in several steps to pre-
vent uneven clamping.
■
YOKE DESIGN
• When a foreign object is caught in the valve, an excessive
torque may be applied to the yoke. Taking it into account,
design the yoke and joint so as to have sufficient margin
in strength.
• When this unit is used in an application such as temper-
ature control of a steam line, the temperature can rise
higher than the ambient temperature due to heat con-
ducted through or radiated from the piping. Use a longer
yoke for effective heat dissipation and apply insulation
material.