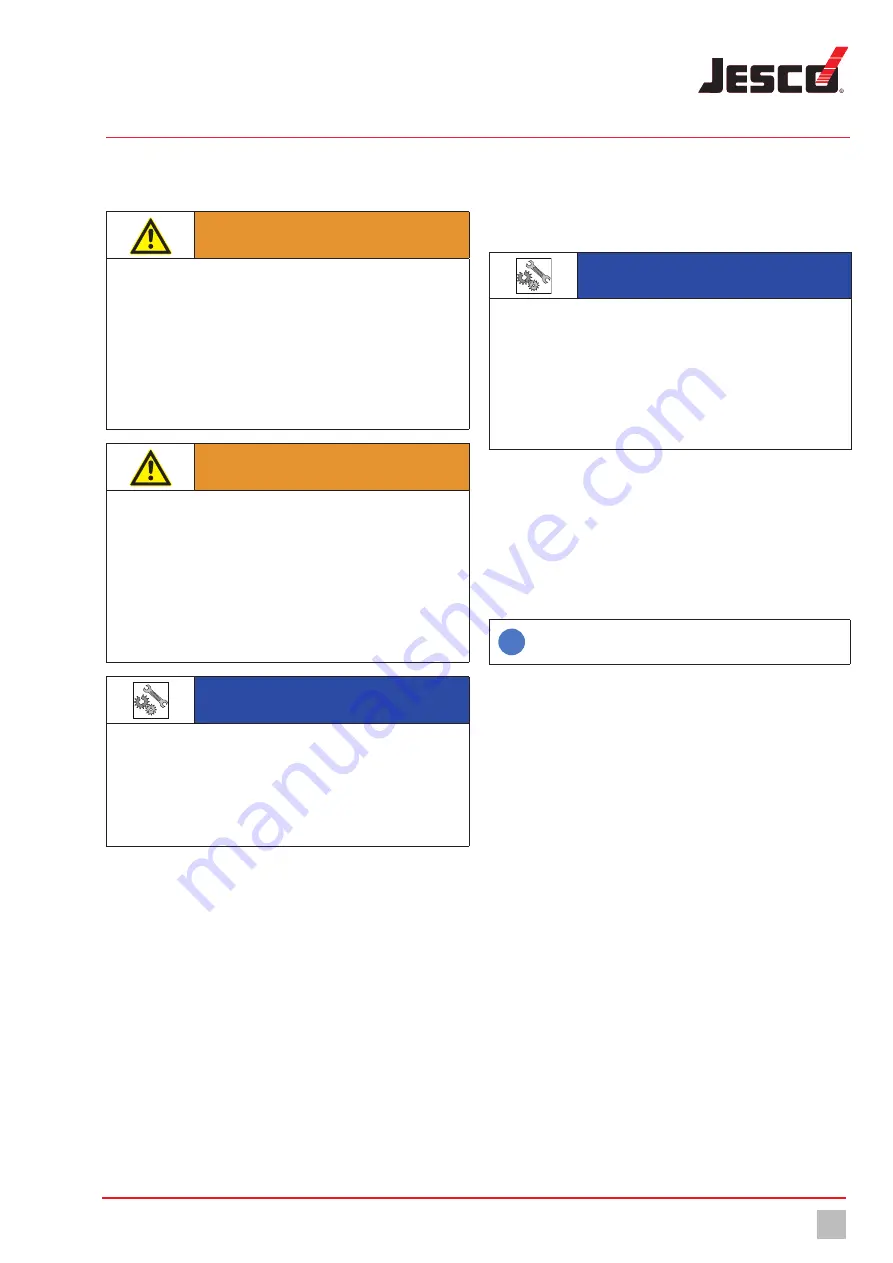
Installation
Installation location
17
© Lutz-Jesco GmbH 2015
Subject to technical changes.
150527
BA-70200-02-V01
Polymer preparing and dosing station EASYPURE Powder and Liquid
Operating instructions
7 Installation
WARNING
Increased risk of accidents due to insufficient qualifica-
tion of personnel!
This device and its accessories may only be installed, operated and
maintained by personnel with sufficient qualifications. Insufficient
qualification will increase the risk of accidents.
ð
Ensure that all action is taken only by personnel with sufficient and
corresponding qualifications.
ð
Prevent access to the system for unauthorised persons.
WARNING
Danger of personal injury and material damage!
The device is extremely heavy. The failure to take adequate safety
precautions during transportation and to act with caution can lead to
accidents involving personal injuries and damage to property. Limbs
can be crushed when the device is set up.
ð
Transport the device using a floor conveyor that is suitable for the
load such as a pallet truck, forklift truck or crane.
ð
Wear safety shoes while transporting the device.
Note
Damage to the system due to incorrect installation
The failure to observe installation instructions (e.g. use of unsuitable
tools, incorrect torque) can damage the system parts.
ð
Use suitable tools.
ð
Note the specified torque.
7.1 Installation location
n
A base with a maximum incline of 1:200 is recommended on which to
set-up the device.
n
The system must be accessible for operation, maintenance and filling
with dosing medium
7.2 Hydraulic installations
Note
Soiling from water of an insufficient quality
The use of water from the cleaning process or other water with insuffi-
cient cleaning leads to soiling of the pressure-relief valve and
flocculate deposit on the chambers. This results in increased soiling in
the system and increases the maintenance requirements.
ð
The water used must be of a quality similar to drinking water. It
should be free of solids and suspended matter.
Precondition for action:
ü
The device is not filled.
ü
The system has been disconnected electrically and is protected
against reconnecting.
Perform the following working steps:
1.
Close the water supply on the input of the water equipment.
i
Size of the connections see chapter 5.4 „Connection
dimensions“ on page 14.
2.
Install a pipe disconnecter in the drinking water supply if the local
conditions require it.
3.
Connect the dosing pump suction line to the dosing chamber output.
4.
Connect the overflow pipe and lead the pipe in a suitable outflow
ü
Hydraulically installed
Содержание EASYPURE 1000
Страница 2: ......