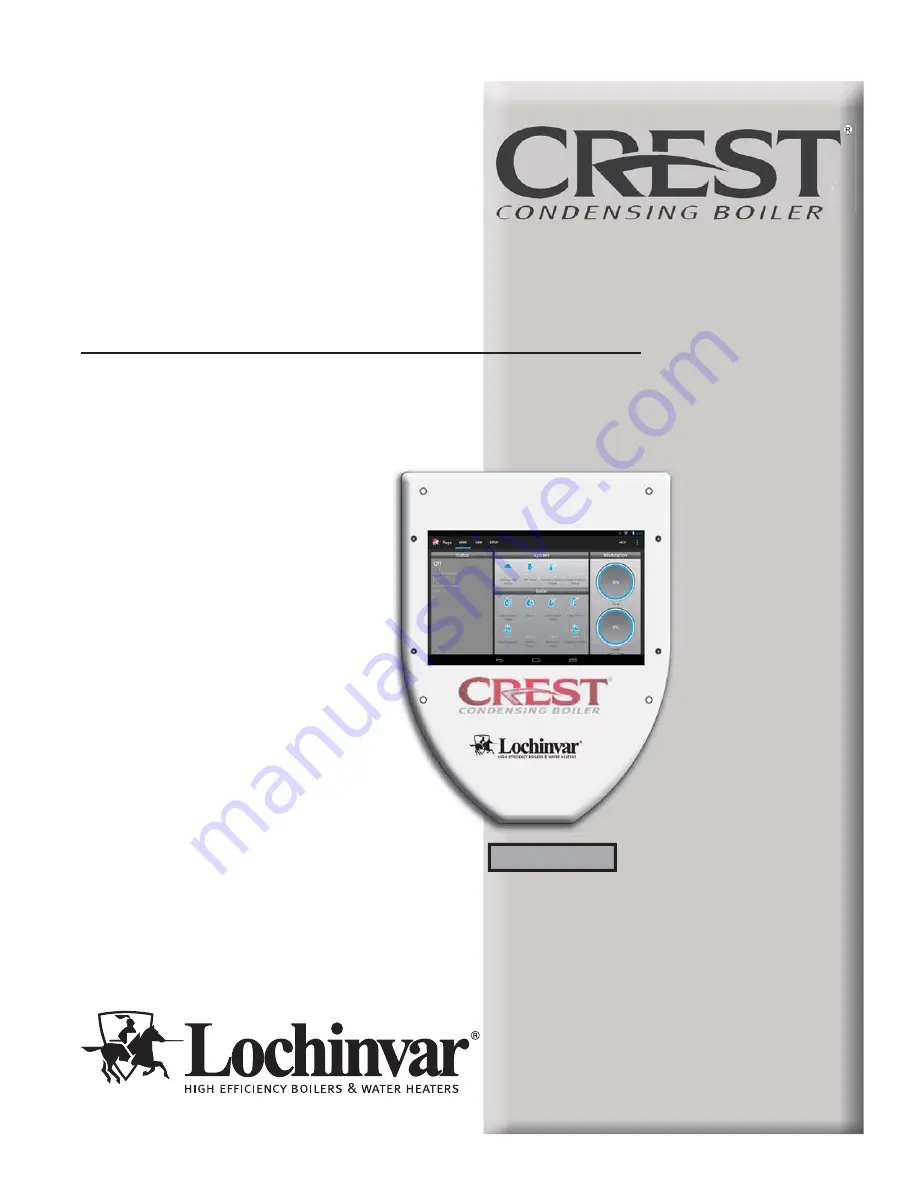
Service Manual
w/CON•X•US Interface
Models:
2500 - 6000
This manual must only be used
by a qualified heating installer
/ service technician. Read
all instructions, including
this manual and the Crest
Installation and Operation
Manual, before installing.
Perform steps in the order
given. Failure to comply could
result in severe personal injury,
death, or substantial property
damage.
WARNING
Save this manual for future reference.
FB-SER_100161013_2000004598 Rev R