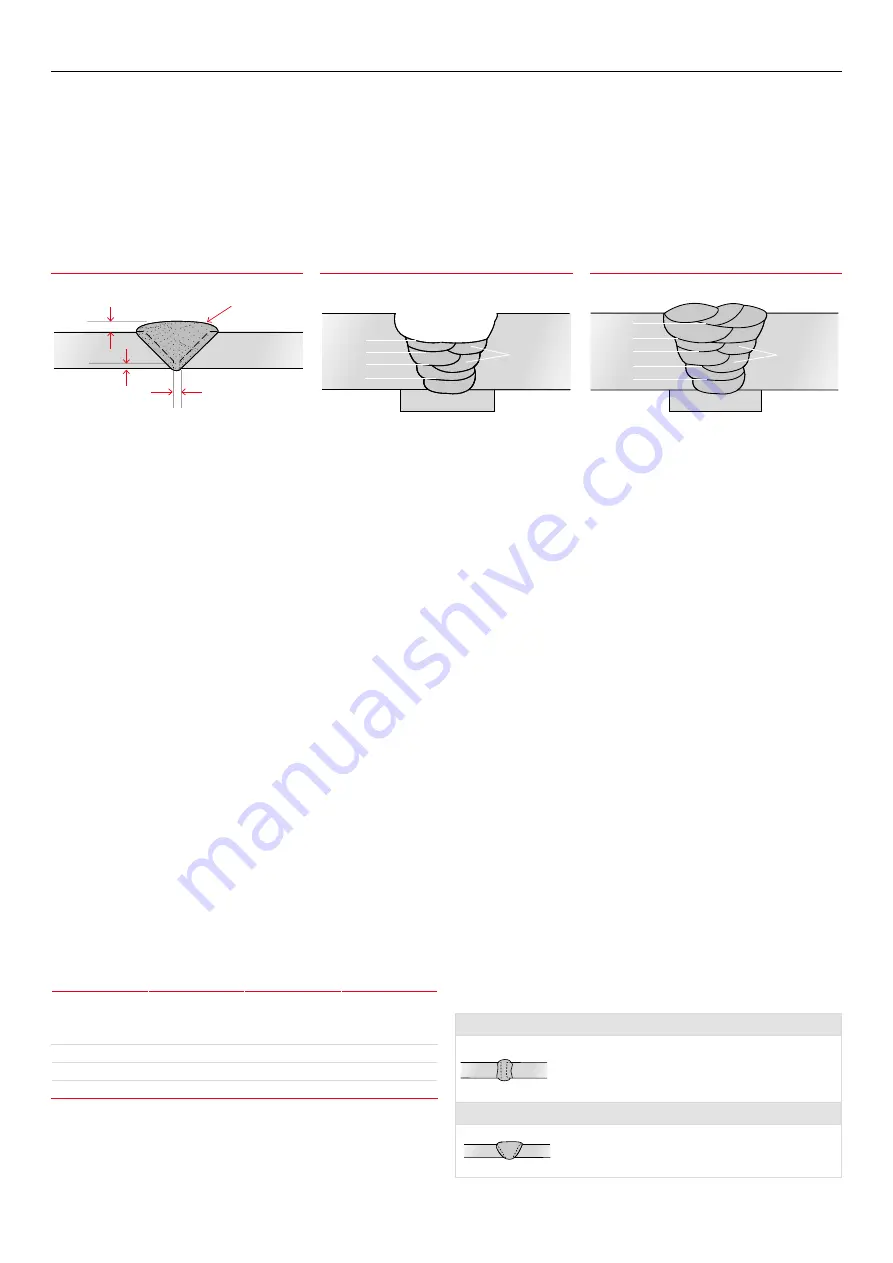
Electrode angle
The angle which the electrode makes with the work is important to
ensure a smooth, even transfer of metal. The recommended angles
for use in the various welding positions are covered later.
Correct travel speed
The electrode should be moved along in the direction of the joint being
welded at a speed that will give the size of run required. At the same
time the electrode is fed downwards to keep the correct arc length
at all times. As a guide for general applications the table below gives
recommended run lengths for the downhand position.
Correct travel speed for normal welding applications varies between
approximately 125–375 mm per minute, depending on electrode size,
size of run required and the amperage used.
Excessive travel speeds lead to poor fusion, lack of penetration, etc.
Whilst too slow a rate of travel will frequently lead to arc instability, slag
inclusions and poor mechanical properties.
Run length per electrode – BOC Smootharc 13
Electrode
Size (mm)
Electrode
Length (mm)
Run Length (mm)
Minimum
Maximum
4.0
350
175
300
3.2
350
125
225
2.5
350
100
225
Correct work preparation
The method of preparation of components to be welded will depend on
equipment available and relative costs. Methods may include sawing,
punching, shearing, lathe cut-offs, flame cutting and others. In all
cases edges should be prepared for the joints that suit the application.
The following section describes the various joint types and areas
of application.
3.5 Types of joints
Butt welds
A butt weld is a weld made between two plates so as to give continuity
of section. Close attention must be paid to detail in a butt weld to ensure
that the maximum strength of the weld is developed. Failure to properly
prepare the edges may lead to the production of faulty welds, as correct
manipulation of the electrode is impeded.
Two terms relating to the preparation of butt welds require explanation
at this stage. They are:
→
Root Face: the proportion of the prepared edge
that has not been bevelled.
→
Root Gap: the separation between root
faces of the parts to be joined.
Various types of butt welds are in common use and their suitability for
different thickness of steel are described as follows:
Square Butt Weld
Weld Beads
Weld Beads
Layers
Layers
70˚ - 85˚
Electrode
Slag
Weld Pool
Weld Metal
Arc
Direction Of Welding
The edges are not prepared but
are separated slightly to allow fusion through the full thickness
of the steel. Suitable for plate up
to 6 mm in thickness.
Single ‘V’ Butt Weld
Weld Beads
Weld Beads
Layers
Layers
70˚ - 85˚
Electrode
Slag
Weld Pool
Weld Metal
Arc
Direction Of Welding
This is commonly used for plate up to 16 mm in thickness and on
metal of greater thickness where access
is available from only one side.
Electrode Angle for 1st and 2nd Layers
Electrode Angle for Subsequent Layers
Butt Welding
Weld Face
Face Reinforcement
Root Face
Root Gap
Weld Beads
Weld Beads
Layers
Layers
70˚ - 85˚
Electrode
Slag
Weld Pool
Weld Metal
Arc
Direction Of Welding
Weld Beads
Weld Beads
Layers
Layers
70˚ - 85˚
Electrode
Slag
Weld Pool
Weld Metal
Arc
Direction Of Welding
17
BOC Smootharc Advance II MIG 400R Operating manual