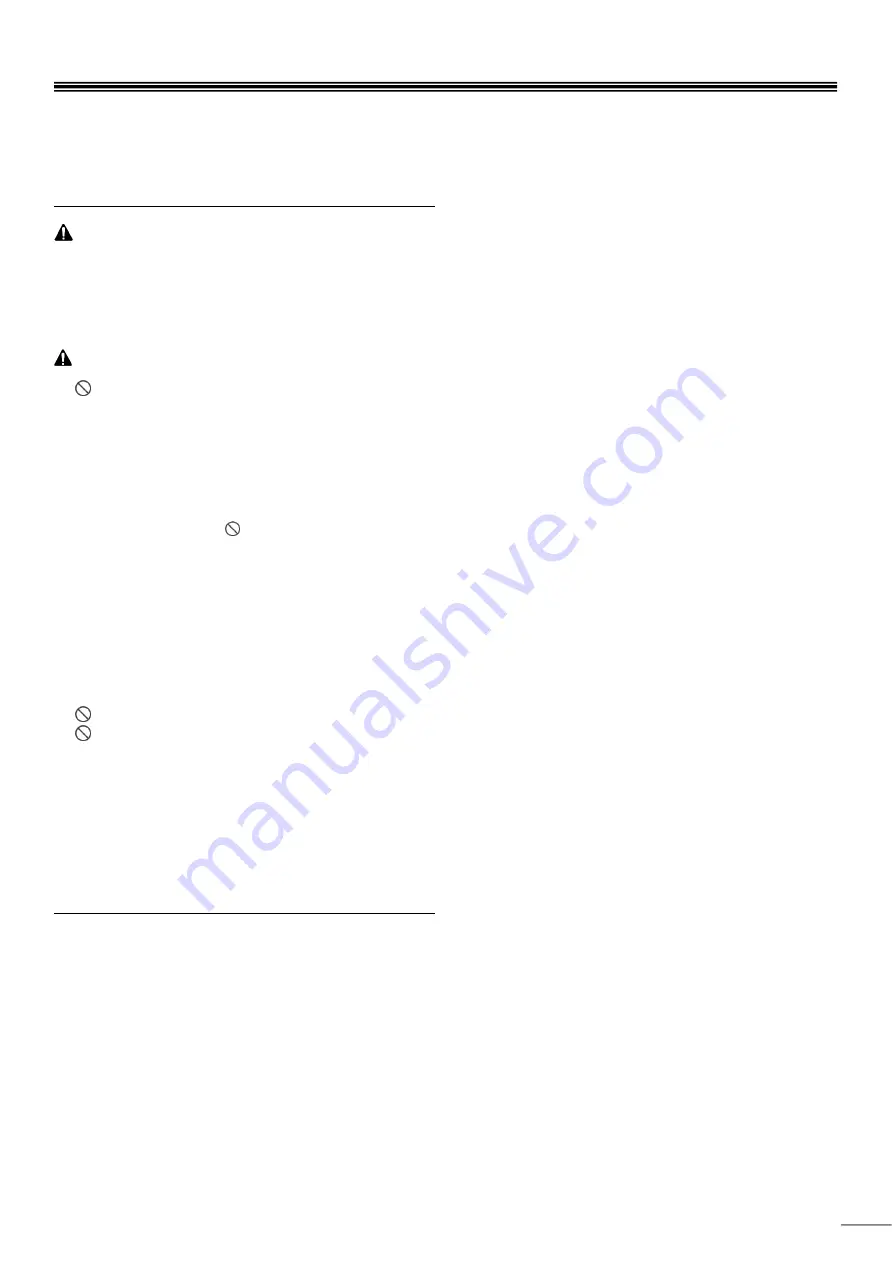
Due to our policy of continuous product innovation, some specifications may change without notification.
©LG Electronics U.S.A., Inc., Englewood Cliffs, NJ. All rights reserved. “LG” is a registered trademark of LG Corp.
33
LEAK / PRESSURE CHECK AND EVACUATION
Leak / Pressure Check
After the refrigerant piping installation is complete,
perform a triple leak / pressure test to check for leaks at
any joints or connections within the piping system.
DANGER
Using combustible gases, including oxygen, will result in fire or
explosion and result in severe personal injury or death. Use
inert gas (medical-grade dry nitrogen) when checking leaks,
cleaning, installing/repairing pipes, etc. The use of a 600psig
nitrogen regulator is required for safety.
WARNING
•
Do not apply power to the units before performing a
system leak test. There is a possibility that the EEV valves
will close and isolate sections of the piping system, making
the leak test inconclusive. Contact your LG Applied Rep or
service technician for the procedure to reopen the EEV
valves before the leak test ONLY if the power has been
applied
•
Use a vacuum pump or Inert (nitrogen) gas when doing
leakage test or air purge.
Do not compress air or Oxygen
and do not use Flammable gases. Otherwise, it may cause
fire or explosion. There is the risk of death, injury, fire or
explosion.
•
For multi-frame outdoor units, connect the nitrogen cylinder
regulator to the gauge manifold, then connect the gauge
manifold to the Schrader port on the service port of only
one outdoor unit, preferably the slave outdoor unit that is
farthest away from the refrigerant piping system and
connected indoor units / heat recovery units.
•
Never perform the leak test using refrigerant
•
To avoid nitrogen entering the refrigerant system in a
liquid state, the top of the cylinder must be higher than its
bottom (used in a vertical standing position) when the
system is pressurized
•
Use only a leak-free gauge manifold set
•
The bubble solution must be a solution designed for
refrigerant leak testing. Common soap solution must never
be used on refrigerant piping as those contain chemicals
that could corrode copper and brass, and cause product
malfunction
Leak / Pressure Check Procedure Steps.
1. After the refrigerant piping installation is complete,
open the isolation ball valves, if any that will have
been included in the piping system.
2. Verify that all outdoor unit service ports are closed.
For multi-frame outdoor units, verify the service
valves on all master and slave outdoor units are
closed and the stem head access caps are tight. The
leak / pressure check is to be performed to only the
refrigerant piping system and connected DOAS units
3. Remove the caps on the Schrader ports. Connect
the (medical-grade dry) nitrogen cylinder regulator to
a gauge manifold, then connect the gauge manifold
to the Schrader ports on the hot gas line (high
pressure vapor), liquid line, and suction (low
pressure vapor) service ports..,
4. Perform the leak / pressure check at 150 psig for five
(5) minutes (standing pressure check).
5. Perform the leak / pressure check at 300 psig for
fifteen (15) minutes (standing pressure check).
6. Perform the leak / pressure check at 550 psig for 24
hours to make sure the piping system is leak-free.
After the gauge reading reaches 550 psig, isolate the
system by first closing the gauge manifold, then
close the nitrogen cylinder valve. Check the flared
and brazed connections for leaks by applying a
bubble solution to all joints.
7. If the pressure does NOT drop for 24 hours, the
system passes the test. See how ambient conditions
will affect the pressure test below.
Ambient Conditions and the Leak /
Pressure Check
If the ambient temperature changed between the times when
pressure was applied and when the pressure drop was
checked, adjust results by factoring in approximately 0.79 psi
for each 1°F of temperature difference.
Correction formula:
(°F Temperature when pressure was applied - °F Temperature
when pressure drop was checked) x 0.79.
Example: When pressure (550 psig) was applied, temperature
was 80°F; 24 hours later when pressure drop (540 psig) was
checked, temperature was 68°F.
Thus, (80°F - 68°F) x 0.79 = 9.5 psig.
In this case, the pressure drop of 9.5 psig was due to
temperature differences, therefore, there is no leak in the
refrigerant piping system.
8. If the pressure drops and it is not due to ambient
conditions, there is a leak and it must be found.
Remove the bubble solution with a clean cloth, repair
the leak(s), and perform the leak / pressure check
again.
9. After the system has been thoroughly tested and no
leaks are found, depressurize by loosening the
charging hose connector at the nitrogen cylinder
regulator. When system pressure returns to normal,
completely disconnect the charging hose from the
cylinder, and release the nitrogen charge from all
refrigerant piping. Wipe off any remaining bubble
solution with a clean cloth
.