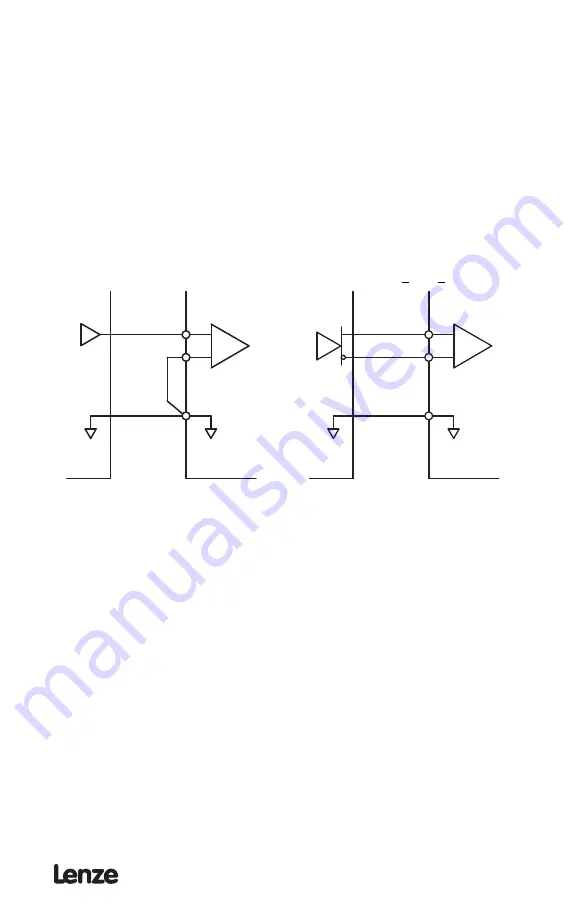
S94P01B
25
5.3 Analog I/O details
5.3.1 Analog reference input
AIN+, AIN1- (P3.24 and P3.25)
The analog reference input can accept up to a ±10V analog signal across AIN1+
and AIN2-. The maximum limit with respect to analog common (ACOM) on each
input is ±18VDC. The analog signal will be converted to a digital value with 16 bit
resolution (15 bit plus sign). This input is used to control speed or torque of the motor
in velocity or torque mode. The total reference voltage as seen by the drive is the
voltage difference between AIN1+ and AIN1-. If used in single-ended mode, one of the
inputs must be connected to a voltage source while the other one must be connected
to Analog Common (ACOM). If used in differential mode, the voltage source is
connected across AIN+ and AIN- and the driving circuit common (if any) needs to be
connected to the drive Analog Common (ACOM) terminal.
Reference as seen by drive: Vref = (AIN1+) - (AIN1-) and -10V < Vref < +10V
����
����
�����
����
�����
��
�����
�
�
����
����
�����
����
�����
��
�����
�
�
Reference
Source
Reference
Source
Single-ended
Differential
S909
AIN2+, AIN2- (P3.20 and P3.21)
The analog reference input can accept up to a ±10V analog signal across AIN2+ and
AIN2-. The maximum limit with respect to analog common (ACOM) on each input is
±18VDC. The analog signal will be converted to a digital value with 10 bit resolution
(9 bit plus sign). This input is available to the User’s program. This input does not
have a predefined function. Scaling of this input is identical to AIN1.
5.3.2 Analog output
AO (P3.23)
The analog output is a single-ended signal (with reference to Analog Common
(ACOM) which can represent the following Motor data:
• Not Assigned
• RMS Phase Current
• Peak Phase Current
• Motor Velocity
• Phase U Current
• Phase V Current
• Phase W Current
• Iq current
• Id current
MotionView Setup program can be used to select the signal source for the analog
output as well as its scaling.
If the output function is set to “Not Assigned” then the output can be controlled directly
from user’s program. See the 940 Programming Manual for details on programming.
Содержание PositionServo 940
Страница 1: ...Model 940 USERS MANUAL S94P01B S929...
Страница 12: ...S94P01B 10 3 2 Clearance for Cooling Air Circulation S924...
Страница 66: ...S94P01B 64 Notes...
Страница 67: ......