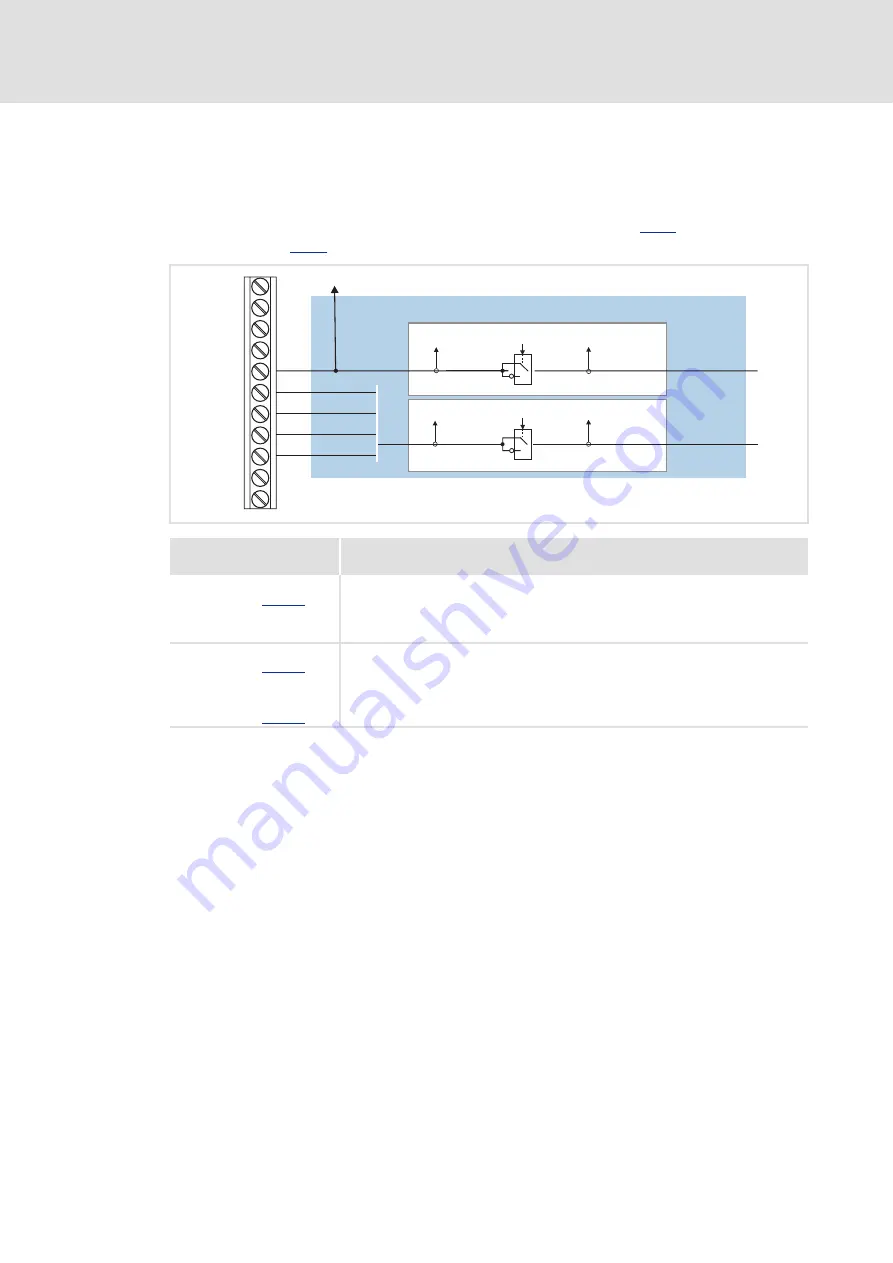
Firmware 03.00 - DMS EN 5.0 - 07/2009
L
117
8400 BaseLine D | Software Manual
I/O terminals
Digital inputs
6.2.3
System block "LS_DigitalInput"
The system block
LS_DigitalInput
displays the digital inputs in the function block editor.
A total of four digital inputs DigIn1 ... DigIn4 can be parameterised. For each of the
processing functions, the terminal function can be inverted with
The status can be
at the input and output of the processing function.
Output
DIS code | data type
Value/meaning
bCInh
| BOOL
Controller enable
Note:
In addition, there is a direct and non-configurable connection to the output stages
of the frequency inverter.
bIn1
| BOOL
...
Digital input DI1
bln4
| BOOL
Digital input DI4
LS_DigitalInput
GND
A1U
AR
12I
RFR
DI1
DI2
DI3
DI4
24E
DO1
X4
bCInh
bIn1 ... bIn4
Bit 0 ... 3
Bit 1
Bit 0 ... 3
Bit 1
C443/2
C114
0
1
C443/1
C443/1
C443/2
C114
0
1