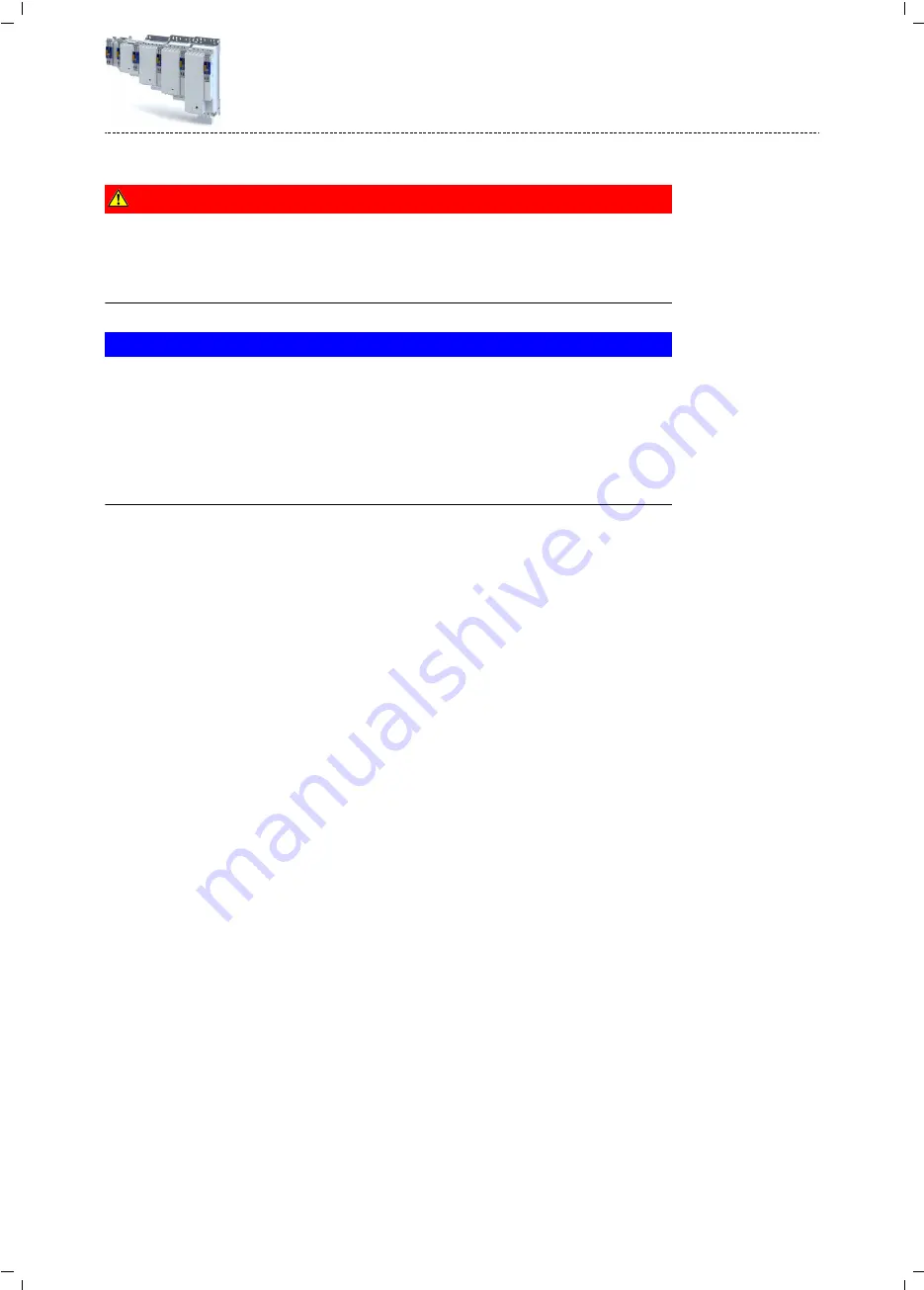
12.4.3
Pole position identification (PPI) with minimum movement
DANGER!
Mechanical damage of the motor caused by hanging loads!
The motor may be permanently damaged.
▶
The motor must not be braked or blocked during the pole position identification. Thus, this
function must not be used for hanging loads!
NOTICE
Thermal overload of the motor!
The motor may be permanently damaged.
▶
Before executing the pole position identification, check that the following monitoring sys-
tems are parameterised correctly in order to prevent a permanent damage of the motor in
the event of an error:
▶
Motor overload monitoring (i²*t)
▶
Functional description
If servo control for synchronous motor is set and if no error is pending, the current position is
memorised after controller enable, and the current is increased along a ramp for 10 s to 35 %
of the rated motor current. This will cause the rotor to align, which, however, is compensated
by a position control. If the rotor makes an electrical movement of more than 20°, an error
message is output, and the value measured is discarded. This might occur in the case of
motors with considerable detent torques.
If the current has reached its final value, a plausibility check is executed after a short interval:
in order to detect a non-permissible blocking of the motor, a positive and a negative test angle
(± 20°) relative to the current position are defined after the identification. The motor must
align itself to these two test angles within a tolerance of 25 %.
Conditions for the execution
•
The motor must not be braked or blocked during the pole position identification.
•
The servo inverter is error-free and in
device state.
Response of the motor during performance
The motion of the motor will maximally correspond to the set "Max. permissible motion"
(Lenze setting: 20°). If a greater motion is detected via the encoder system, the pole position
identification is cancelled and the parameterised error response (Lenze setting: Fault) is trig-
gered.
How to execute the pole position identification PLI (min. movement):
1
.
If the servo inverter is enabled, disable it.
2
.
Set the object
to "6" to change to the "pole position identification PLI (min. move-
ment)" operating mode.
3
.
Enable the servo inverter to start the process.
Note: Inhibiting the controller serves to abort the started procedure any time if required
without changing the settings.
Configuring the feedback system
Synchronous motor: Pole position identification (PPI)
Pole position identification (PPI) with minimum movement
231
Содержание i950 Series
Страница 1: ...Inverters i950 servo inverters Commissioning EN ...
Страница 2: ......
Страница 312: ...15 Configure engineering port The given path leads you to the engineering port Configure engineering port 312 ...
Страница 397: ...19 Safety functions Supported safety functions for Basic Safety STO 4Safe Torque Off STO 398 Safety functions 397 ...
Страница 497: ......
Страница 498: ......
Страница 499: ......