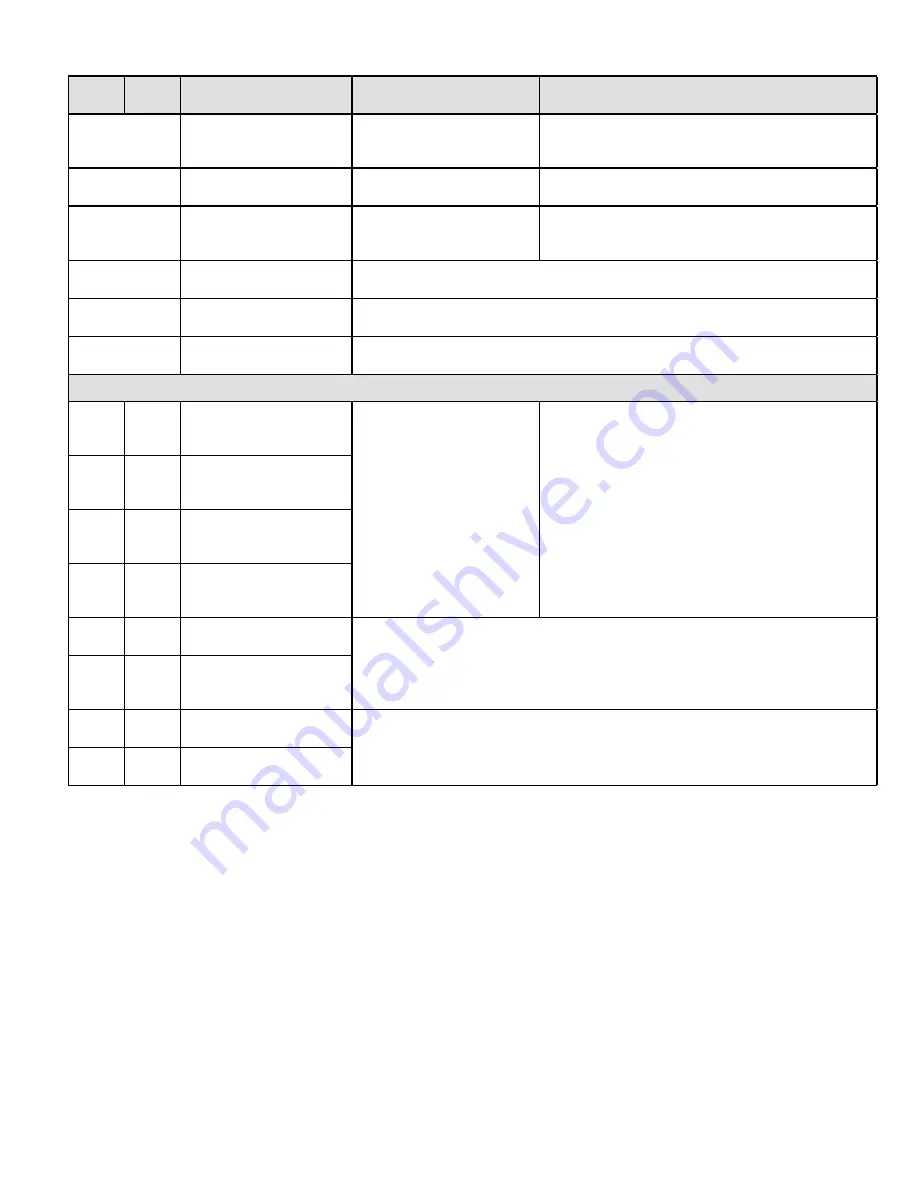
506468-01
Page 17 of 24
Issue 1946
Control Board Diagnostic LEDs
DS2
Green
DS1
Red
Condition / Code
Possible Cause(s)
Solution
Off
Power problem
No power (24V) to board
terminals R & C or board
failure.
1
Check control transformer power (24V).
2
If power is available to board and LED(s) do not light,
replace board.
Simultaneous
SLOW flash
Normal operation
Unit operating normally or in
standby mode.
None required.
Alternating
SLOW flash
5-minute anti-short cycle
delay
Initial power up, safety trip,
end of room thermostat
demand.
None required (Jumper TEST pins to override)
Simultaneous
FAST flash
Ambient sensor problem
Sensor being detected open or shorted or out of temperature range. Board will revert
to time/temperature defrost operation. (System will still heat or cool)
Alternating
FAST flash
Coil sensor problem
Sensor being detected open or shorted or out of temperature range. Board will not
perform demand or time/temperature defrost operation. (System will still heat or cool)
On
Circuit board failure
Indicates that board has internal component failure. Cycle 24V power to board. If
code does not clear, replace board.
Fault & Lockout Codes (Each fault adds 1 strike to that code’s counter; 5 strikes per code = LOCKOUT)
Off
SLOW
flash
Low pressure fault
1.
Restricted air flow over
indoor or outdoor coil.
2. Improper refrigerant
charge in system.
3. Improper metering device
installed or incorrect
operation of metering
device.
4. Incorrect or improper
sensor location or
connection to system.
1. Remove any blockages or restrictions from coils
and/or fans. Check indoor and outdoor fan motor
for proper current draws.
2. Check system charge using approach & sub-
cooling temperatures.
3. Check system operating pressures and compare
to unit charging charts.
4. Make sure all pressure switches and sensors
have secure connections to system to prevent
refrigerant leaks or errors in pressure and
temperature measurements.
Off
On
Low pressure LOCKOUT
SLOW
flash
Off
High pressure fault
On
Off
High pressure LOCKOUT
SLOW
flash
On
Discharge line
temperature fault
This code detects shorted sensor or high discharge temperatures. If the discharge
line temperature exceeds a temperature of 300°F (148°C) during compressor
operation, the board will de-energize the compressor contactor output (and
the defrost output if active). The compressor will remain off until the discharge
temperature has dropped below 225°F (107°C).
FAST
flash
On
Discharge Line
Temperature LOCKOUT
Off
FAST
flash
Discharge sensor fault
The board detects open sensor or out of temperature sensor range. This fault is
detected by allowing the unit to run for 90 seconds before checking sensor resistance.
If the sensor resistance is not within range after 90 seconds, the board will count one
fault. After 5 faults, the board will lockout.
FAST
flash
Off
Discharge sensor
LOCKOUT
Table 6. Control Board Diagnostic LEDs