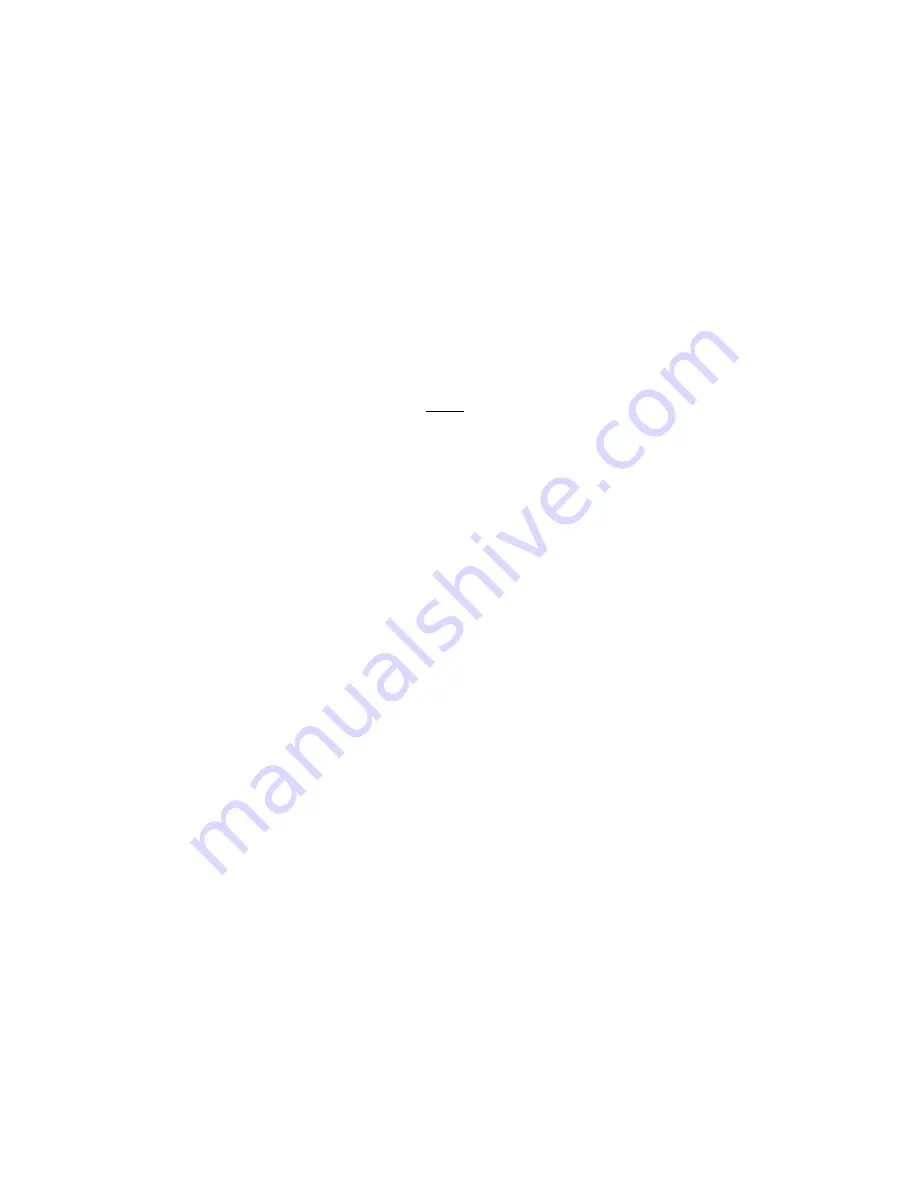
LEADER EVAPORATOR WSE Evaporator
2018
Page:
4
3.
When
a.
Keep stack temperature in range of 650
o
F to 800
o
F
b.
Maintain the arch ½ to ⅔ full
c.
Fire consistently with small amounts of wood to maintain level of heat
d.
Use timer to stay on schedule with firings
e.
Adjust firing intervals as needed to maintain an even boil
Defoamer
The purpose of defoamer is to prevent foam build up in the pans. Foam build up will prevent proper evaporation of the
water from the sap. It will give a false liquid level to the float not allowing the incoming sap to flow in a consistent
manner. Inconsistent defoamer usage will create large volume adds of sap into the pans as the foam is reduced (when
you do add defoamer) and the float seeks to replace the level with incoming sap. The following items should be of
concern in the use of defoamer:
1.
Use defoamer on a regular basis. It is suggested you add defoamer to the flue pan each time you fire the
evaporator.
2.
Add defoamer primarily to the flue pan. Modify this only under certain conditions.
3.
The estimated usage for a 2 foot wide WSE is 3 drops. The usage may need to be changed as the sap
characteristics change. NOTE: This is based on the use of ATMOS 300 Defoamer
4.
NEVER add defoamer to the center compartments of the syrup pan. Use one drop at a time in the syrup (draw-
off) compartment.
Minimize Reversal Effects
Reversal occurs when the boil in the flue pan is reduced (when firing is inconsistent, end of day, change pan flow
direction). As the flue pan boil reduces, the level is reduced so more fresh sap is added and sap will flow back from the
syrup pan. This causes the “sweet” in the syrup pan to mix back across the syrup pan and increases the volume of sap in
the flue pan. To minimize this effect:
1.
Maintain a consistent boil
2.
After the last syrup draw of the day, draw 1 to 1 ½ gallons of “sweet” from the syrup pan into a clean container.
This will be added to the boiling syrup pan at the beginning of the next boil and aid in setting up the gradient.