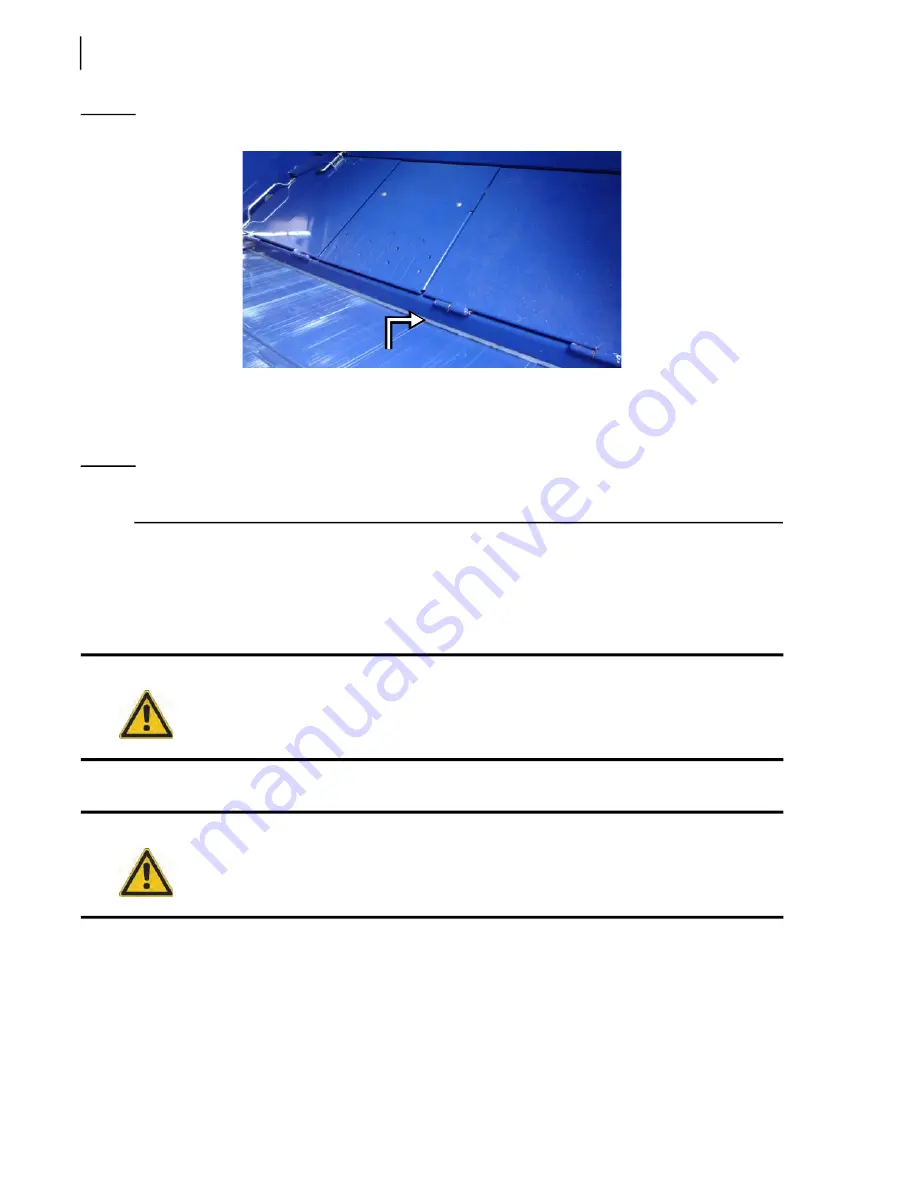
166
General Maintenance
Figure 3
-
235 Lower wear pad (in units without an automated arm)
Replacing Lower Wear Pad
A. Standard Units W/ Loading Arm and Dual H
ELPING
-H
AND
™ Units
N
OTE
:
For standard units with no loading arm, go to page 167; for co-mingle units with loading arm,
go to page 170; for co-mingle units with no loading arm, go to page 175.
To replace a worn-out lower wear pad, apply the following procedure:
1.
Start the engine and engage the hydraulic pump.
2.
Using the joystick, extend the automated arm to get better access to the hopper area.
In dual H
ELPING
-H
AND
™ units, extend the right-hand side automated arm only.
3.
Fully retract the packer using the yellow button on the packer control station.
4.
Turn OFF the hydraulic pump and the engine.
5.
Lock out and tag out the vehicle (see
Locking Out and Tagging Out the Vehicle
6.
Remove the anti-spill guards located on each side of the hopper (see Figure 3
250).
An R-pin located just behind the anti-spill guard (see Figure 3
251) must be pulled completely to
allow for the removal of the guard.
7.
Remove the deflector panel by unscrewing the 4 bolts that hold it in place.
Danger!
Secure the area around the path of the automated arm when performing maintenance
or repair.
Danger!
Do not enter the hopper while the packer is moving.
Содержание EXPERT
Страница 1: ...EXPERT TM MAINTENANCE MANUAL...
Страница 2: ......
Страница 3: ...EXPERT MAINTENANCE MANUAL...
Страница 10: ...viii Table of Contents...
Страница 18: ...8 Introduction...
Страница 244: ...234 General Maintenance...
Страница 251: ...Lubrication 241 Figure 4 11 Glass compartment lubrication chart optional...
Страница 252: ...242 Lubrication Figure 4 12 EXPERT lubrication chart...
Страница 261: ...Lubrication 251 Figure 4 27 Packer lubrication points 2 Grease fitting LH side front cylinder pin...
Страница 263: ...Lubrication 253 Pump Drive Shaft U Joint Figure 4 30 Pump drive shaft lubrication points Grease fittings...
Страница 264: ...254 Lubrication...
Страница 320: ...310 Hydraulic System...
Страница 357: ...Troubleshooting 349...
Страница 358: ...350 Troubleshooting...
Страница 386: ...378 Multiplexing...
Страница 388: ...380 Lifting Arms Figure 10 1 Mounting bolts Figure 10 2 Wear pads Figure 10 3 Helping Hand gripper...