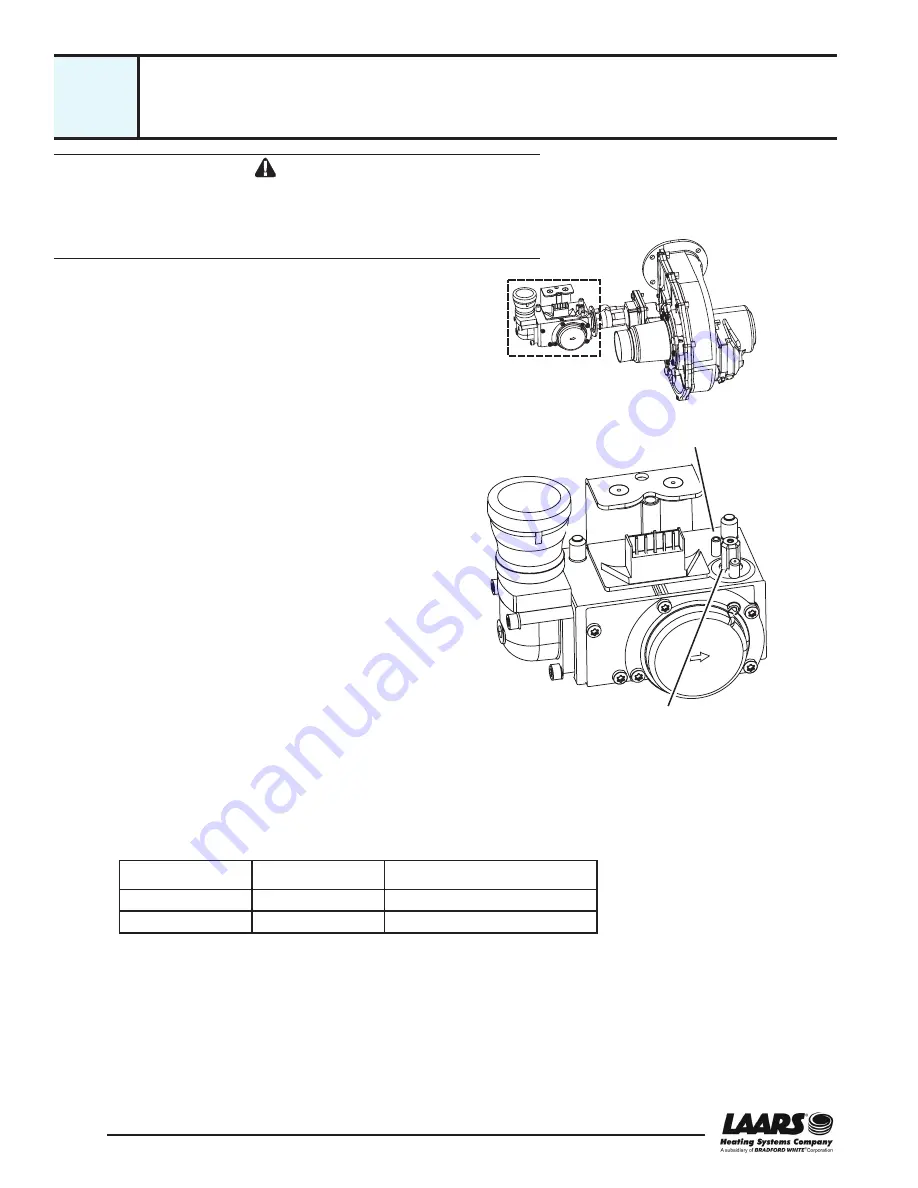
62
Service Manual - NeoTherm 500
Combustion Adjustment Procedure -
Units with Current User Interface
WARNING
Improper adjustment of the high fire and low fire settings may lead
to poor combustion, increasing the amount of carbon monoxide
produced. Excessive carbon monoxide levels may lead to personal
injury or death.
Equipment required:
• Combustion analyzer
• 2 mm Allen wrench
Fig. C3-1 - High- and low-fire adjustments on gas valve
Procedure:
1. Start by measuring the CO
2
and O
2
in the flue prod
-
ucts at high fire. The controller has a feature that
makes it easy to go directly to the high fire condition.
The unit will operate at high fire for 5 minutes, then
return to normal operation.
How to get there: From the “Home” screen, press
“I” to go to “Info/ Install.” Choose “Test,” then go to
“Forced Rate.” Select “Set High Fire,” then select
“Start Test.”
The CO
2
readings should be between the values
shown in Table C3-1. If the CO
2
is not within the cor
-
rect range, adjust the high fire setting. See Fig. C3-1
to locate the high fire adjuster screw. Slowly make
adjustments (1/16 of a turn at a time) until the CO
2
is within the range shown in the table. For the high
fire adjustment, turning the screw counter-clockwise
(CCW) makes the mixture richer.
Gas Type
High Fire CO
2
Low Fire CO
2
Natural
8.8% to 9.0%
0.5% lower than high fire CO
2
Propane
9.8% to 10.0%
0.5% lower than high fire CO
2
Table C3-1 - CO
2
Range and Pressure Differential
C3
Low fire CO
2
adjustment
High fire CO
2
adjustment
Содержание NEOTHERM NTV
Страница 2: ......
Страница 10: ...Service Manual NeoTherm 500 viii...
Страница 68: ...58 Service Manual NeoTherm 500...
Страница 115: ...105 Service Manual NeoTherm 500 Appendix 3 Wiring Diagram App3...
Страница 116: ...106 Service Manual NeoTherm 500...
Страница 117: ......