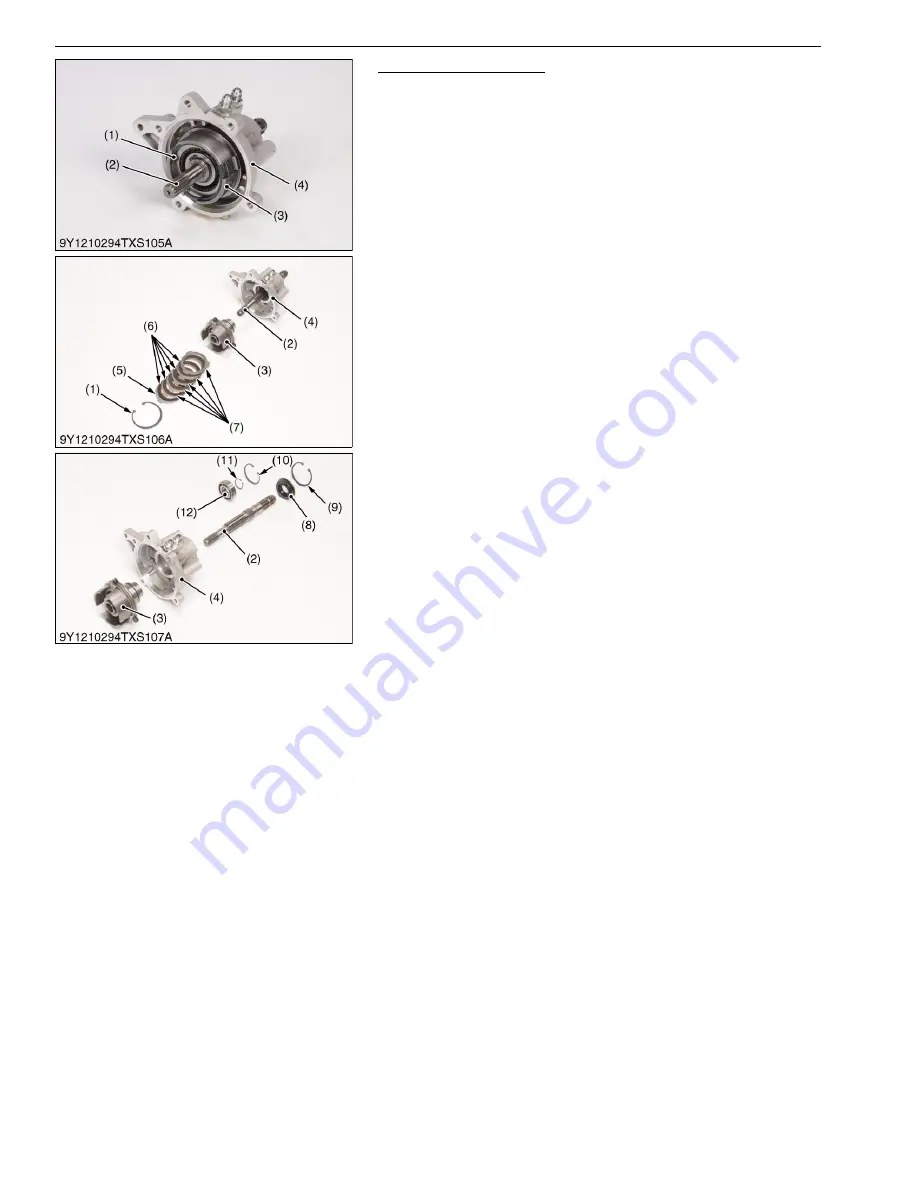
TRANSAXLE
G23, G26, WSM
2-S36
(EU)
Hydraulic PTO Clutch 3
1. Remove the cir-clip (1).
2. Remove the backing plate (5), the disk plates (6), and the
separate plates (7) from the clutch case (3).
3. Remove the cir-clip (9) and the oil seal (8).
4. Remove the cir-clip (10) and the front PTO shaft (2) from the
rear case (4).
5. Remove the cir-clip (11) and the ball bearing (12) from the front
PTO shaft (2).
(When reassembling)
• Do not damage the oil seal.
• Install the disk plates and the separate plates to the original
positions.
9Y1210294TXS0054US0
(1) Cir-clip
(2) Front PTO Shaft
(3) Clutch Case
(4) Rear Case
(5) Backing Plate
(6) Disk Plate
(7) Separate Plate
(8) Oil Seal
(9) Cir-clip
(10) Cir-clip
(11) Cir-clip
(12) Ball Bearing
KiSC issued 08, 2009 A
Содержание G23
Страница 1: ...G23 G26 WORKSHOP MANUAL KiSC issued 08 2009 A ...
Страница 3: ...I INFORMATION KiSC issued 08 2009 A ...
Страница 9: ...INFORMATION G23 G26 WSM I 5 EU 9Y1210294INI0003US0 KiSC issued 08 2009 A ...
Страница 10: ...INFORMATION G23 G26 WSM I 6 EU 9Y1210294INI0004US0 KiSC issued 08 2009 A ...
Страница 11: ...INFORMATION G23 G26 WSM I 7 EU 9Y1210294INI0005US0 KiSC issued 08 2009 A ...
Страница 15: ...INFORMATION G23 G26 WSM I 11 EU 4 DIMENSIONS LD 9Y1210294INI0007US0 KiSC issued 08 2009 A ...
Страница 16: ...INFORMATION G23 G26 WSM I 12 EU HD 9Y1210294INI0008US0 KiSC issued 08 2009 A ...
Страница 17: ...G GENERAL KiSC issued 08 2009 A ...
Страница 81: ...1 ENGINE KiSC issued 08 2009 A ...
Страница 149: ...2 TRANSAXLE KiSC issued 08 2009 A ...
Страница 205: ...3 FRONT AXLE KiSC issued 08 2009 A ...
Страница 216: ...4 STEERING KiSC issued 08 2009 A ...
Страница 231: ...5 HYDRAULIC SYSTEM KiSC issued 08 2009 A ...
Страница 266: ...6 ELECTRICAL SYSTEM KiSC issued 08 2009 A ...
Страница 268: ...ELECTRICAL SYSTEM G23 G26 WSM 6 M1 EU 1 WIRING DIAGRAM 1 G23 KiSC issued 08 2009 A ...
Страница 269: ...ELECTRICAL SYSTEM G23 G26 WSM 6 M2 EU 2 G26 KiSC issued 08 2009 A ...
Страница 308: ...7 MOWER KiSC issued 08 2009 A ...
Страница 329: ...8 GRASS COLLECTOR KiSC issued 08 2009 A ...