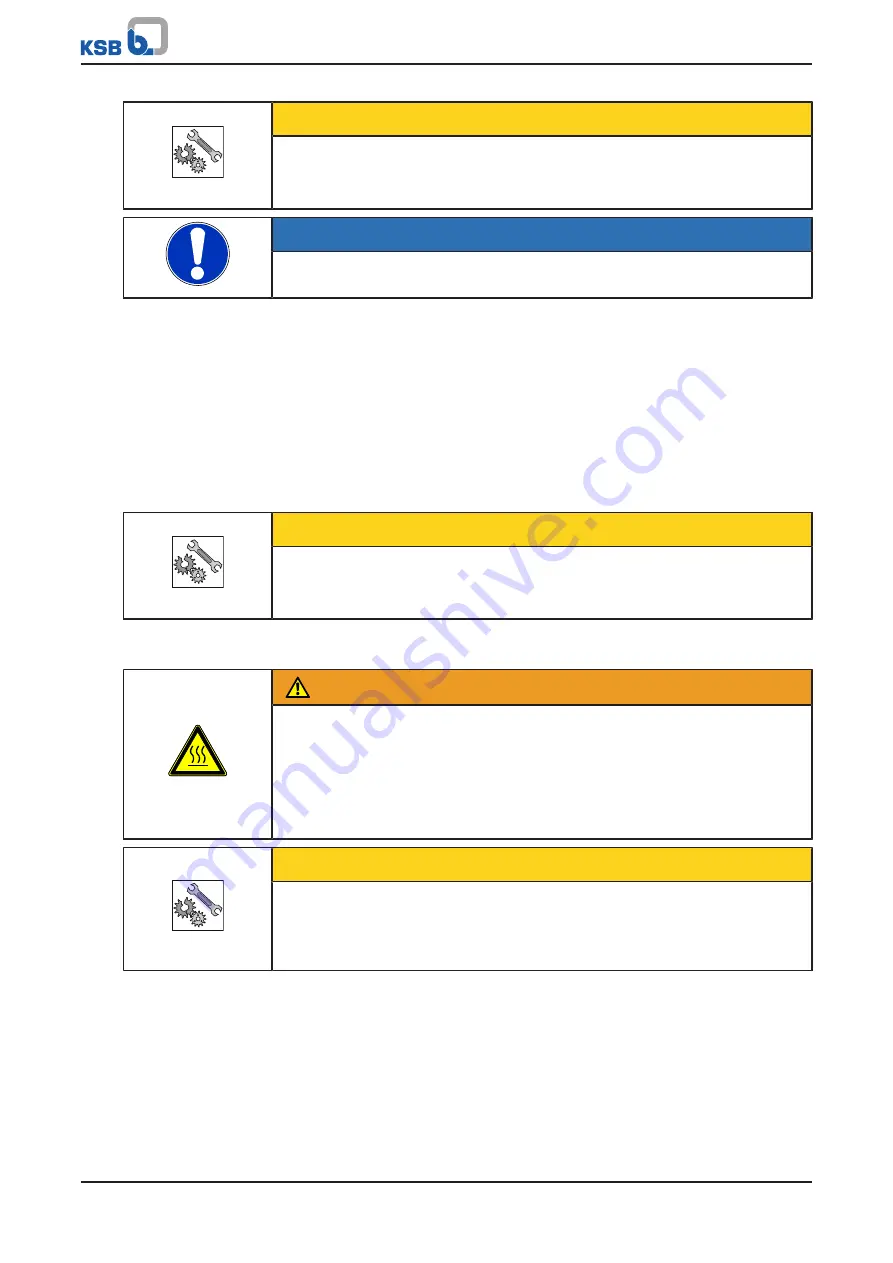
5 Installation at Site
16 of 32
Calio-Therm S NC/NCV
CAUTION
Air entering the pump
Damage to vertically installed pump sets whose direction of flow is downwards!
▷
Fit a vent valve at the highest point of the suction line.
NOTE
To prevent any impurities from collecting in the pump do not install the pump at
the lowest point of the system.
1.
The circulator is usually installed in the piping directly upstream of the drinking
water storage tank. The water is pumped from the last tapping point via the
circulation line back to the storage tank.
2.
Install a lift check valve on the pump's discharge side. It prevents backflow
through the pump when the tap is opened.
3.
A shut-off valve is installed on the pump's suction side to facilitate maintenance.
Calio-Therm S NCV comes with a lift check valve and a shut-off option integrated
in the lower pump section.
4.
Install the pump with the pump shaft in a horizontal position. Connect the
piping without transmitting any stresses and strains.
An arrow on the pump casing indicates the direction of flow.
CAUTION
Heat building up at motor housing and pump casing
Pump overheating!
▷
Never insulate the motor and electronic system housings.
5.4 Connecting the piping
WARNING
Impermissible loads acting on the pump nozzles
Risk of burns by leakage of hot fluids!
▷
Do not use the pump as an anchorage point for the piping.
▷
Anchor the pipes in close proximity to the pump and connect them without
transmitting any stresses or strains.
▷
Take appropriate measures to compensate for thermal expansion of the piping.
CAUTION
Contamination/dirt in the piping
Damage to the pump!
▷
Flush the piping prior to commissioning or replacing the pump. Remove any
foreign matter.
Содержание Calio-Therm S NC
Страница 1: ...Drinking Water Pump Calio Therm S NC NCV Installation Operating Manual ...
Страница 29: ......
Страница 30: ......
Страница 31: ......
Страница 32: ...KSB SE Co KGaA Johann Klein Straße 9 67227 Frankenthal Germany Tel 49 6233 86 0 www ksb com 1157 88 05 EN ...