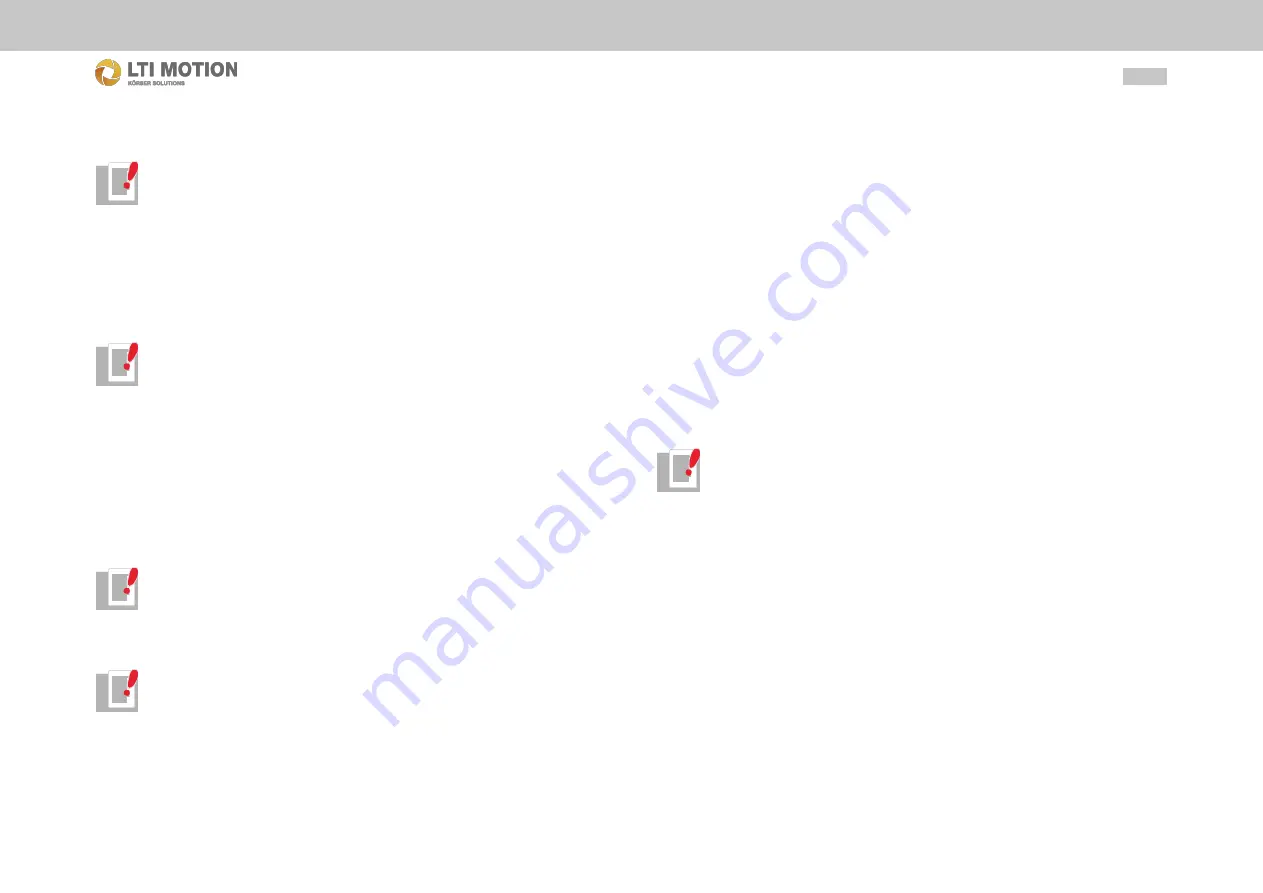
26
Id.-Nr.: 1556.212 .1-07
Connections and wiring
Information
For further information please consult the respective manuals.
5.3
Connecting the stationary operating
panel
Stationary operating panels are connected to the control via the graphic interface.
Information
For additional information, please refer to the respective manuals.
5.4
Connecting the Handterminal
The handheld terminal communicates with the central unit via an Ethernet connec-
tion. The interface between both communication partners is called the "junction box".
It contains connections for the handheld terminal and for the PLC.
The junction box is usually mounted inside the cabinet such that the plug socket is
pushed through an outlet in the cabinet's wall. It must be locked against torsion.
Information
There are 2 possible ways to configure the network. Either actuate the
handheld terminal and the programming (programmer PC) together via one
ethernet interface (with a switch) or divide the programming (Eth0) and the
handheld terminal (Eth1). Therefore see chapter "Network design".
Information
For further information on installation please consult the respective manu-
als. All required safety regulations must be strictly adhered to.
Caution
Before the robot is started the emergency stop and the enabling switch
must be wired via the junction box to the safety-PLC.
5.5
Connecting axis modules
If a LACP 26x is used axis modules (SO CM-x) can be connected decentralized via
the EtherCAT interface of the CPU module. The axis modules must be supplied by a
supply module (SO CMP).
Up to 9 axis modules with maximum 27 axis can be appended to a MO CM via a con-
nected supply module (SO CMP).
Motors and encoder connections
Motors are connected to a SO CM-x axis controller via a power cable which also in-
cludes the brake control (optionally also temperature values). The encoder values
are transmitted to the axis controller via the encoder cable.
For "Hyperface DSL" encoders, the connection is established via a power cable that
includes all lines (power cable includes brake + temperature (optional) + encoder val-
ues).
Information
For further information please consult the respective manuals.
5.6
Test of interference immunity
Immunity interference is tested according to guidelines and standards.
See EC directives and standards [
48].