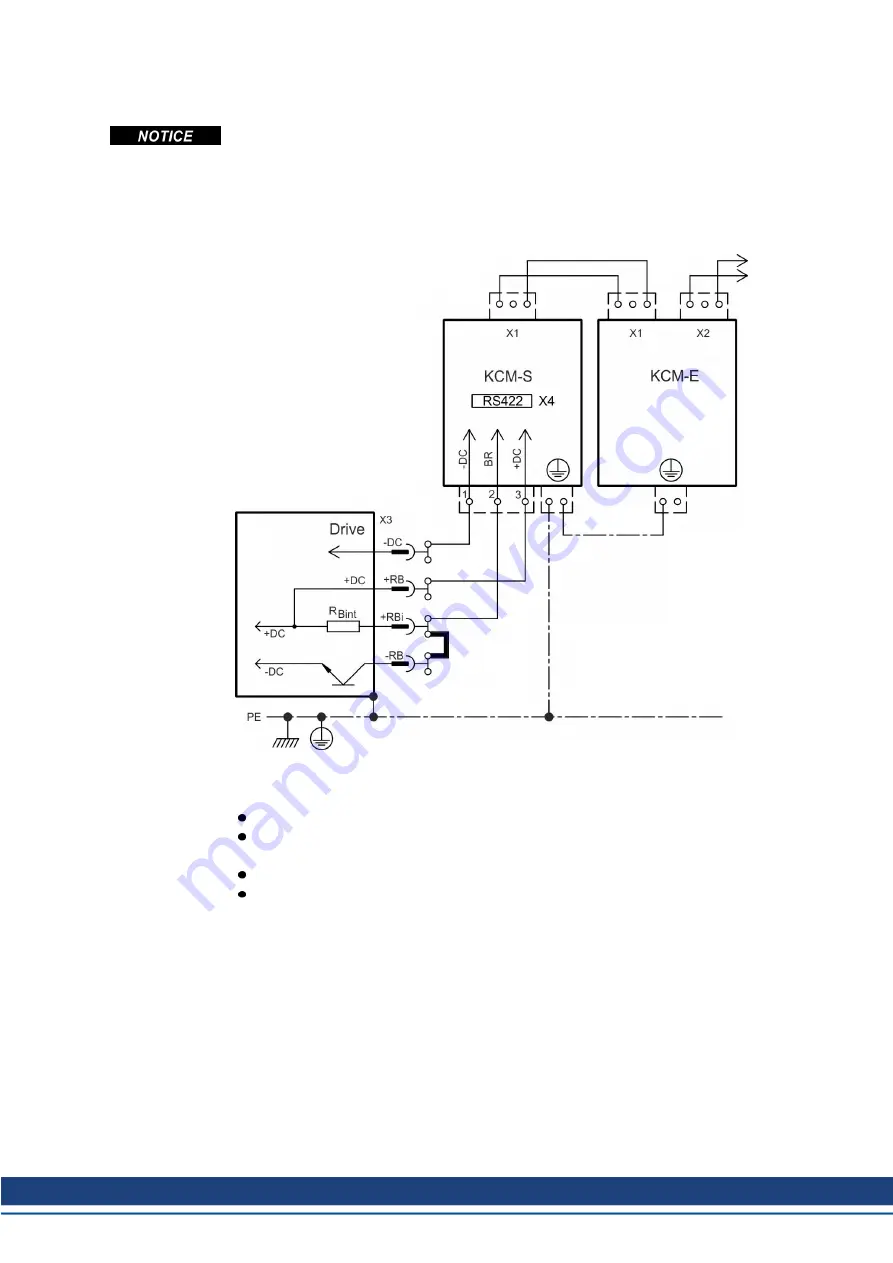
9.9.4.2 Example installation with KCM-S and KCM-E
Maximum cable length between AKD and KCM: 500mm. The DC+ and DC- lines should
always be twisted, maximum cross section is 6mm². Ensure that the polarity is correct,
swapping round DC+/DC- will damage the KCM modules.
Connect the BR connection to theAKD with the most frequent generative braking processes
in the system. This AKD must have an active internal or external brake resistor. Create a
motion profile that causes the brake chopper to respond.
Setup KCM-S and KCM-E
Prerequisite for the following instructions:
Properly disconnected, grounded system.
KCM-S: assembled and wired in the switching cabinet. The load that leads to the activ-
ation of the brake chopper during braking must be connected.
KCM-E: assembled and connected to the KCM-S with connection cable (X1) and PE line.
Discharge aids (plug-in bridge) are removed.
Proceed as instructed below:
1. Switch on the line voltage after the drive has finished the 24V boot process.
2. Enable the AKD and operate the motion profile that causes the brake chopper to respond.
3. The KCM-S determines the chopper threshold and begins to charge; LED (top view)
flashes. The energy stored in the capacitor module during generative braking is available
the next time acceleration happens.
RS422 interface X4 allows data exchange controlled by a terminal software of your choice.
Interface setting: 115200 Baud, 8 Data Bits, 1 Stop Bit, No Parity&Flow Control.
The X4 mating connector is in the package. More information is given in the KCM Instruc-
tions Manual.
AKD Installation | 9 Electrical Installation
Kollmorgen | kdn.kollmorgen.com | October 2017
113
Содержание AKD series
Страница 162: ...AKD Installation 9 Electrical Installation Wiring diagram X24 162 Kollmorgen kdn kollmorgen com October 2017 ...
Страница 179: ...9 20 6 CAN Bus Wiring AKD Installation 9 Electrical Installation Kollmorgen kdn kollmorgen com October 2017 179 ...
Страница 214: ... AKD Installation 11 Index 214 Kollmorgen kdn kollmorgen com October 2017 ...