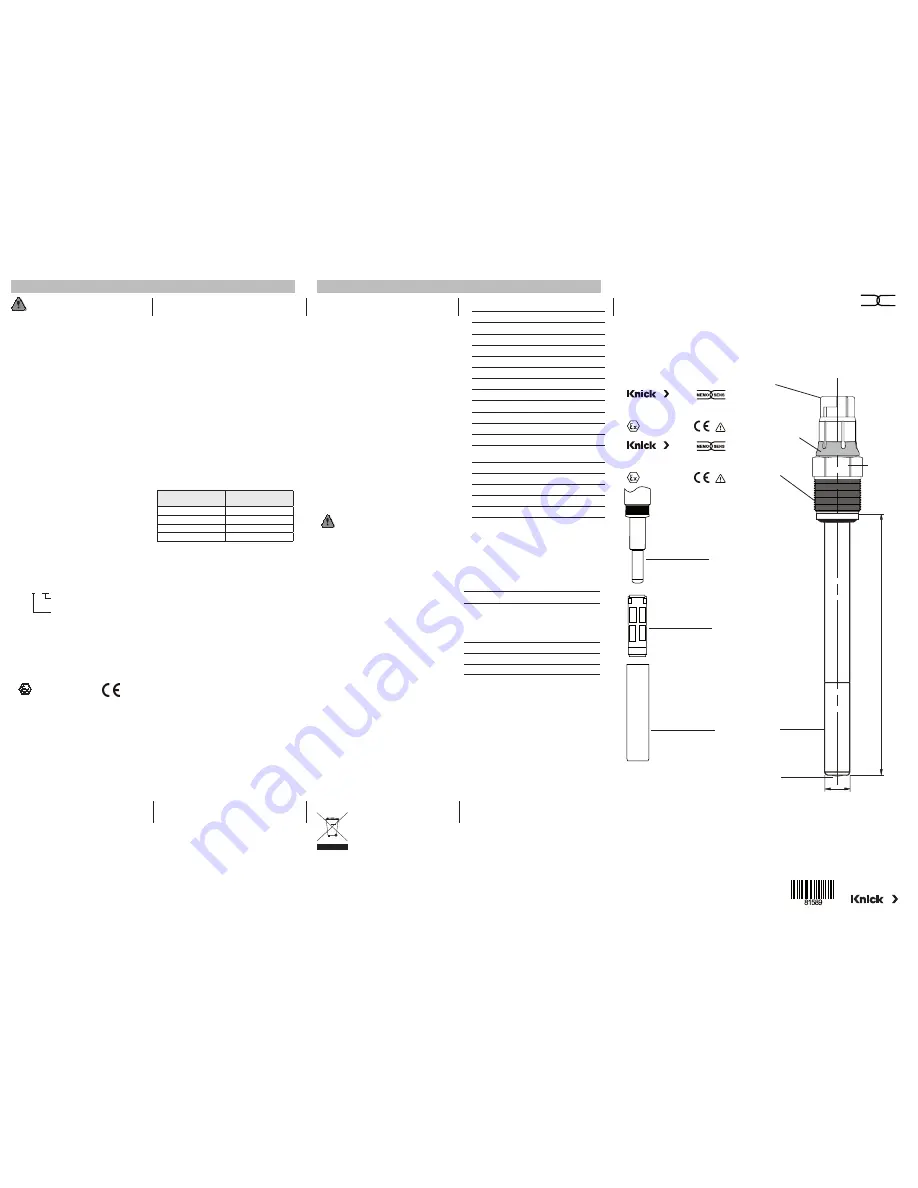
8.2 Assembly
Perform steps 1, 2 and 3 for mounting the interior body.
1. Insert the interior body in the sensor body. Turn it
until the slot in the interior body engages with the
pin in the sensor body.
2. Press the interior body in the sensor shaft until the
stop is reached. Then screw on the lock nut and
tighten it using a 3/8" open-end wrench.
3. Check all O-rings for damage. Replace if necessary.
4. Half fill the membrane module with O
2
electrolyte.
Make sure that there are no air bubbles in the mem-
brane module.
Note: Air bubbles can be removed by carefully tap-
ping on the membrane module.
Caution!
The electrolyte is strongly alkaline. Avoid
contact of electrolyte with skin, mucous
membranes or eyes. Wear suitable protec-
tive gloves and goggles when servicing the
sensor.
5. Slip the membrane module over the interior body
while holding the sensor in a vertical position.
Remove excess electrolyte with a paper tissue.
Note: Make sure that there is no electrolyte, process
solution or any other contamination between mem-
brane module and cap sleeve.
6. Carefully slip the cap sleeve over the membrane
module and screw it tight.
7. Note: After each replacement of electrolyte, mem-
brane module or interior body, you must repolar-
ize (see section 6. Polarization) and recalibrate the
sensor (see section 7. Calibration).
8.1 Disassembly
1. Unscrew the cap sleeve from the sensor shaft and
carefully pull it off the sensor.
2. Pull off the membrane module from the interior
body. Before replacing electrolyte, you must remove
the membrane module from the cap sleeve.
3. Rinse the interior body with distilled water and care-
fully dab it dry with a paper tissue.
Perform steps 4 and 5 only when dismounting the
interior body:1 ⁾
4. Loosen the lock nut using a 3/8" open-end wrench.
5. Pull the interior body out of the sensor shaft. (Use a
plier if necessary.)
Note
Do not twist the interior body when pulling it out. The
contact pins might break off.
4. Hazardous-Area Concept
The sensors are intrinsically safe equipment of Cat-
egory 1. They may be installed within explosive gas
atmospheres up to Zone 0.
1. Connect the sensors only to an intrinsically safe, ap-
proved cable of Type CA/MS-***X** (BVS 09 ATEX E
083 X) from Knick Elektronische Messgeräte GmbH
& Co. KG.
2. Do not operate the sensors under electrostatically
adverse conditions. Prevent strong vapor and dust
streams from acting directly on the sensors and
measuring cable. The shaft length is not Ex-relevant.
1. Observe the stipulations for electrical installations in
explosive gas atmosphere (EN/IEC 60079-14) when
using the sensors and cables.
2. Observe the stipulations/conditions for safe use of
the connected intrinsically safe Memosens® sensor.
1. Introduction
The Knick oxygen sensors of the SE 707 series with
Memosens
®
connector system are low-maintenance
and pressure-resistant oxygen sensors with integrated
temperature detector.
SE 707 sensors are suitable for in-line measurement
of dissolved oxygen and temperature in the different
fields of analytical chemistry:
• Biotechnology
• Pharmaceutical industry
• Fermentation
SE 707 sensors are suitable for sterilization and auto-
claving and are CIP capable.
Instructions for Use of Series SE 707-Memosens
®
Oxygen Sensors
Caution!
Please read these instructions carefully before
putting the sensor into operation, in order
to ensure faultless function. Operation and
servicing of the sensor must be carried out by
specially trained personnel authorized by the
operating company.
Warning!
After an Ex-certified sensor has been used with
non-Ex components, this sensor must no longer
be used in a hazardous location.
II 1 G Ex ia IIC T3/T4/T6
BVS 10 ATEX E 089 X
0044
Instructions for Use of Series SE 707-Memosens
®
Oxygen Sensors
Knick
Elektronische Messgeräte GmbH & Co. KG
P.O. Box 37 04 15
D-14134 Berlin
Germany
Tel: +49 (0)30 - 801 91 - 0
Fax: +49 (0)30 - 801 91 - 200
www.knick.de
TA-SE707MS-KNX02
20100709
SE 707
MEMO
SENS
Memosens
®
connector
Pg
13.5
Ø 12 mm
120
/ 225
mm
12345
67
Serial No.
Note!
If the ambient temperatures indicated are observed,
no impermissible temperatures for the temperature
class in question occur at the equipment.
Cap sleeve
Membrane
Membrane module
Interior body
Recommended fittings:
ARI 106
ARF 200/202
ARF 210
ARD 230
SensoGate® WA 130/131
2. Safety information
The sensor is intended only for the use described in
section 1. Introduction above. Be sure to wear safety
goggles and gloves when cleaning or calibrating a sen-
sor using acid or alkaline solutions.
The sensors are designed for an operating pressure
of 6 bars and meet the PED requirements (Pressure
Equipment Directive 97/23/EC, Article 3, Sec. 3).
3. Product description
The markings on each sensor or on the packaging label
include the following information:
Knick
Manufacturer of sensor
SE 707/*-*MSN Model designation
Memosens® connector (MS)
Length (1: 120 mm, 2: 225 mm)
-5…80 °C
Temperature range
The serial number is printed on and also electronically
stored in the sensor head. See also enclosed quality
certificate.
6. Polarization
Prior to first use or when the sensor has been discon-
nected from the voltage source for longer than 5 min-
utes, you must polarize the sensor by connecting it to
an operating transmitter and then calibrate it.
Polarization time depends on the time without polar-
ization voltage. The respective polarization times are
shown in the following table.
Time without
polarization voltage d [min.]
Required
polarization time [min.]
d > 30
360
30 > d > 15
6 * d
15 > d > 5
4 * d
d < 5
2 * d
7. Calibration of sensor and transmitter
When the sensor is continuously used, you must cali-
brate it at regular intervals. Calibration is also required
after replacement of electrolyte, membrane module
or interior body.
Note: To check whether the sensor needs to be cali-
brated, you can take it in the air, dab it dry and check
the display on the transmitter. The indicated oxygen
saturation should be close to 100%. If not, you must
calibrate the sensor.
7.1 One-point calibration
Calibration in air with known water-vapor saturation
1. Take the sensor out of the process medium.
2. Clean the sensor shaft.
3. Carefully dab the membrane dry with a paper tissue.
4. Perform the calibration as instructed in the trans-
mitter manual.
(Refer to the manual for further calibration methods.)
7.2 Two-point calibration
For two-point calibration, always start with the zero
calibration before calibrating the slope.
With two-point calibration, you achieve a higher ac-
curacy with very low oxygen concentrations. For zero
calibration, we recommend an oxygen-free medium,
e.g. nitrogen with a purity level of at least 99.995%.
After the sensor signal has stabilized, the sensor and
transmitter are calibrated to the zero value of the
desired process variable.
Please refer to the user manual of the transmitter.
8. Maintenance
The maintenance intervals depend on the sensor
application.
Maintenance comprises cleaning the sensor and
replacing wear parts and consumables such as:
- O-rings
- Electrolyte
- Membrane module
- Interior body
9. Cleaning the sensor
Depending on the measured medium, the sensor must
be cleaned to ensure accurate measurements.
You can clean the sensor shaft with water and a suit-
able brush.
Use water and a soft paper tissue to remove dirt par-
ticles from the membrane or membrane module.
After cleaning, thoroughly rinse with clean water.
Note: Do not use cleaning agents or alcohol. This
could damage the sensor or lead to fault currents.
10. Warranty
12-month warranty after date of shipment in the event
of manufacturing faults.
11. Specifications
Measuring range
pO2 < 1200 mbars
Detection limit
1 ppb
(3 ppb in in liquids containing CO2)
Accuracy
1 % + 1 ppb
(1% + 3 ppb in liquids containing CO2)
Response time at 25 °C
(air –> N2)
98 % full scale < 90 s
Signal in ambient air
290 ... 500 nA
Residual signal in
O2-free medium
≤0.1% of signal in ambient air
In CO2: ≤0.01% of signal in ambient air
Flow dependence
≤ 5%
Permissible pressure
range (measurement)
0.2 ... 6 bars absolute
Mechanical
pressure resistance
Max. 12 bars absolute
Permissible
temperature range
-5 ... 80 °C
Temperature range
(stability)
-5 ... 121 °C
O-ring material
Silicone
(FDA & USP approved up to VI)
Membrane material
PTFE / silicone / PTFE,
FDA compliant
(steel-mesh reinforced)
Process-wetted
sensor parts
Stainless steel, 1.4435
(material certificate 3.1B)
Surface roughness
N5 (RA < 0.4µm)
Temperature detector
NTC 22 kΩ
Interior body
incl. sensing electrodes
Replaceable (ZU 0568)
Sensor cap
Memosens®
12. Accessories / Spare parts
O2 membrane module, separate
ZU 0563
O2 membrane kit, consisting of:
Membrane module (4x),
O-ring set (1x),
25ml electrolyte (1x)
ZU 0564
O2 electrolyte 25 ml
ZU 0565
Interior body for SE 707
ZU 0568
O-ring set, silicone, FDA
ZU 0679
1 ⁾ The interior body must only be replaced if the
electrode system is poisoned or the interior body
is broken.
Cap sleeve
5. Installation and commissioning
1. On unpacking, check the sensor for mechanical
damage. Report any damage to your Knick service
team.
2. Prior to first use, you must fill the sensor with new
electrolyte (see section 8).
3. Remove the protective cap.
4. Please refer to the instruction manual of the relative
fitting in order to install the sensor.
5. Sensor and cable are plugged together and locked
by a quarter turn of the coupling ring. See function
description of Memosens
®
cable.
Prior to first use, you must polarize the sensor. After 6
hours, the sensor is polarized and ready for operation.
See section 6. Polarization for more information.
Note
As delivered, a moderate slope value is stored in the
sensor. The sensor must be calibrated before first use.
SE 707X/1-NMSN
14163 Berlin
00
44
BVS 10 ATEX E089 X
II 1G Ex ia IIC T3/T4/T6
SE 707X/2-NMSN
14163 Berlin
00
44
BVS 10 ATEX E089 X
II 1G Ex ia IIC T3/T4/T6
orange-red ring
Ex-Sensors
11. Disposal
Please observe the applicable local or
national regulations concerning the dis-
posal of “waste electrical and electronic
equipment”.