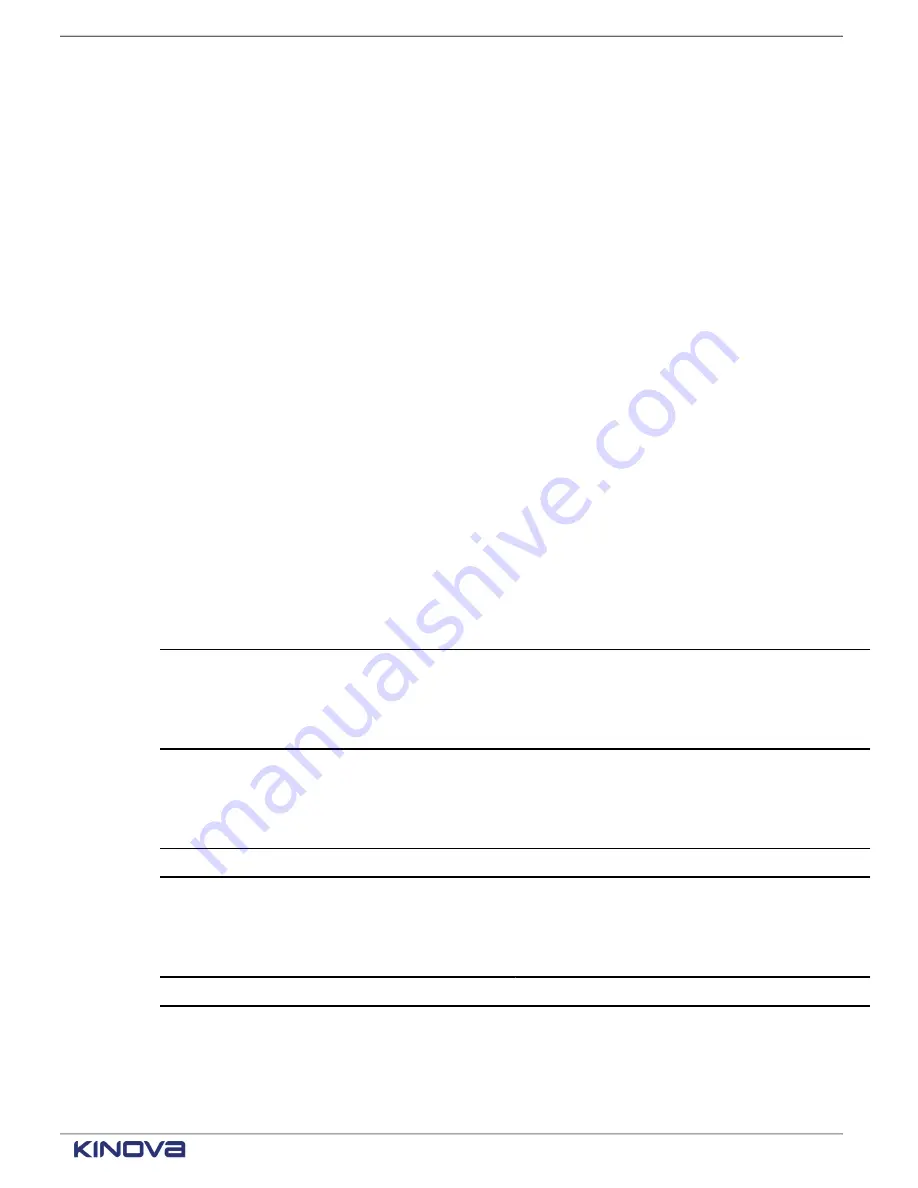
EN UG-020 Link 6 user guide r1.0
87
Safety checksums
The
administrator
needs a quick way to look at the robot and walk away with peace of mind
knowing the safety configurations he put in place are working as expected.
The safety checksum is a human readable hexadecimal value displayed beside the Notification
icon. It is the value calculated from the
SCU
and the
MPU
, using
Cyclic redundancy check (CRC)
,
on all safety parameters.
Whenever the arm is switched on, the
MPU
safety parameter checksum is compared with the
SCU
safety parameter checksum. When a safety parameter is changed, a new checksum is
calculated by the
MPU
and compared against the
SCU
checksum.
The administrator can look at the safety checksum and know whether someone has modified
any of the safety configurations. They can know from a glance whether any safety configurations
are failing. They can write configuration build instructions for their environment and list the
checksum for other administrators to know the valid safety checksum.
If the safety parameter checksums do not match, the robot enters a fault state in which the
administrator must manually correct all safety parameter values. This task is not time-consuming
provided there is a configuration build instruction available that includes the valid safety
checksum value.
Parameters that are the basis for the safety checksum
The calculation of the safety checksum is based on the configuration of the safety functions, the
state of each of the safety functions, and calibration files.
Table 60: Checksum parameters
Safety parameter
Description
Configuration of safety inputs
Binding between safety input channels and the
configured function
Example: Channel 1 is assigned to the function
Enabling device
.
Configuration of safety outputs
Binding between safety output channels and the
configured function
Example: Channel 4 is assigned to the function
Monitored stop
SF03
Safety joint position limit monitoring for joints 1 to 7
SF04
Safety joint speed monitoring for reduced speed
limits for joints 1 to 7
Safety joint speed monitoring for normal speed
limits for joints 1 to 7
SF05
Monitored stop has no parameters
+1 514-277-3777
kinovarobotics.com
© 2022 Kinova inc. All rights reserved.
Содержание Link 6
Страница 1: ...Link 6 user guide Optional gripper shown ...
Страница 8: ......