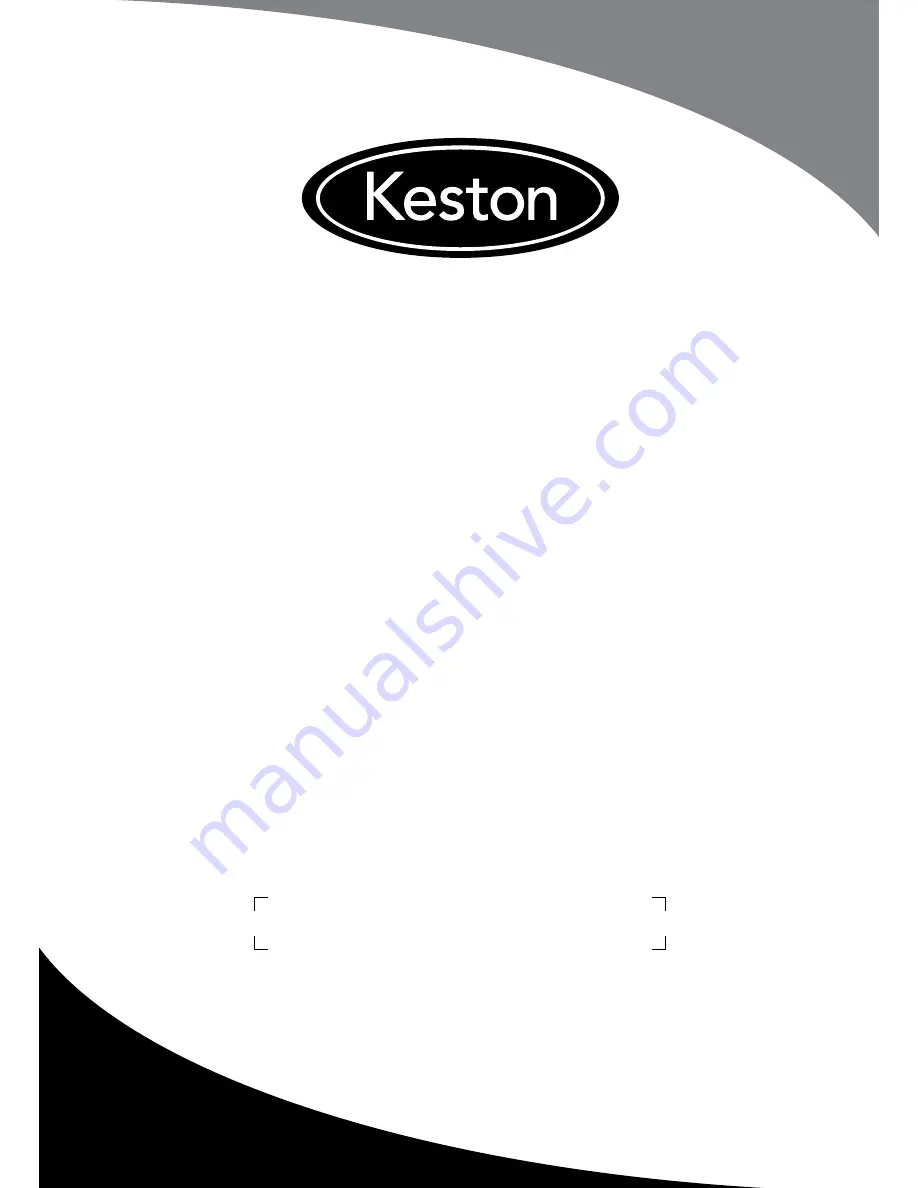
Installation and Servicing Instructions
FAN POWERED HIGH EFFICIENCY
MODULATING CONDENSING
GAS BOILER
Heat 45 & 55
When replacing any part on this appliance, use only spare parts that you can be
assured conform to the safety and performance specification that we require.
Do not use reconditioned or copy parts that have not been clearly authorised by Keston.
For the very latest copy of literature for specification and maintenance practices visit our website
www.keston.co.uk where you can download the relevant information in PDF format.
June 2015
UIN 208964 A04
Содержание HEAT 45
Страница 4: ...4 Keston Heat Installation Servicing ...
Страница 5: ...5 Keston Heat Installation Servicing ...