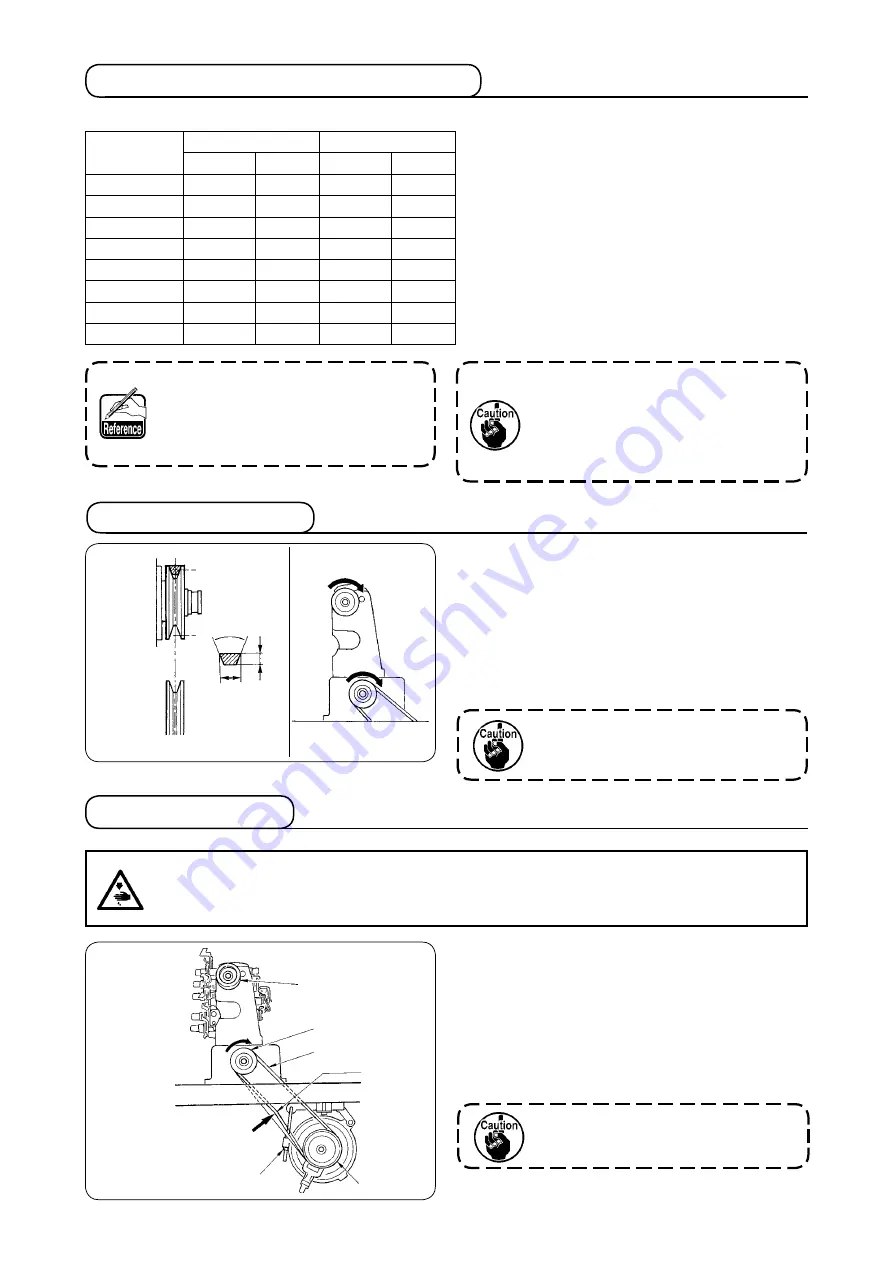
– 7 –
– 7 –
‒ 7 ‒
2. Selecting the motor pulley and the belt
* The table shows the numbers when a 3-phase
2-pole 400 W clutch motor (1 / 2 HP) is used.
* The commercially-available motor pulley near to
the counted value is designated since the outside
diameter of the commercially-available motor pulley
counts by 5 mm.
Use a motor pulley which is adaptable to
this sewing machine. The sewing speed
exceeds the max. sewing speed of this
sewing machine and machine trouble will
be caused unless a motor pulley which is
adaptable to this sewing machine is used.
When you use a new sewing machine, use
the machine at a speed of 4,500 sti/min or
less for the first 200 hours (approximately
one month). A good result can be obtained
in terms of the durability.
Motor pulley and belt
Speed of
stitch
(sti/min)
50Hz
60Hz
Pulley size
Belt size
Pulley size
Belt size
4,500
ø 100
M-35
ø 85
M-35
4,800
ø 105
M-36
ø 90
M-35
5,000
ø 115
M-36
ø 95
M-35
5,500
ø 125
M-37
ø 105
M-36
5,800
ø 130
M-37
ø 110
M-36
6,000
ø 135
M-37
ø 115
M-37
6,200
ø 140
M-38
ø 120
M-38
6,500
ø 150
M-39
ø 125
M-38
3. Installing the motor
Motor pulley
5.5
mm
10 mm
M type V belt
Use a clutch motor of 3-phase, 2-pole, 400 W (1/2HP).
Use the M type V belt.
1) The motor pulley shifts to the left-hand side when de
-
pressing the pedal. At this time, install the motor so
that the centers of motor pulley and lower pulley align
with each other.
* For the installing procedure of the motor pulley, refer to
the Instruction Manual for motor.
Lower pulley
2) Install the motor so that the pulley rotates clockwise.
If the machine pulley rotates in the reverse
direction, nomal lubrication cannot be per-
formed. As a result, machine trouble will
be caused.
4. Setting the belt
WARNING :
When replacing the belt, be sure to turn OFF the power to the motor and ascertain that the motor has
totally stopped rotating before starting the work. There is a danger of injury since hands or clothes may
be caught in the belt.
1) Fit belt
❶
to lower pulley
❷
.
2) Turning upper pulley
❸
, set the other side of the belt to
motor pulley
❹
.
3) Adjust the belt tension so that the belt sags 15 to 20
mm when the center of the belt is pressed with an ap
-
proximate 10N (1.02 kgf) load.
4) Securely fix the belt with lock nut
❺
when the belt has
been set.
❶
❸
❹
❺
❷
15 - 20 mm
If the deflection of the belt is excessive
when the sewing machine is operated,
check again the belt tension.
40˚
Содержание MF-7500 Series
Страница 1: ...i ENGLISH INSTRUCTION MANUAL MF 7500...