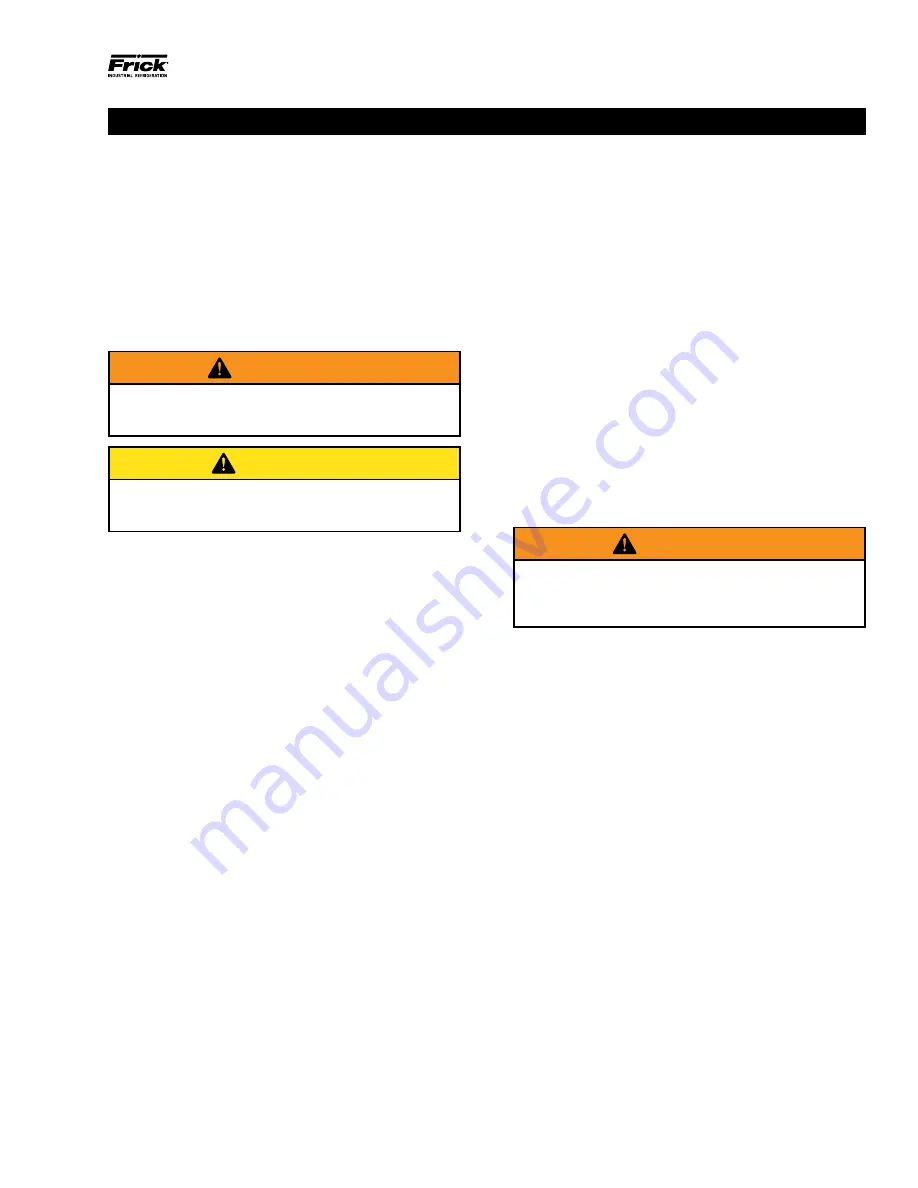
070.550-IOM (JUN 2016)
Page 17
NGC GAS ROTARY SCREW COMPRESSOR
OPERATION
GENERAL INFORMATION
This section provides instructions for normal maintenance,
a recommended maintenance program, troubleshooting
and correction guides. Changing gear sets is not part of the
normal service program. Gear changes must only be
performed by JOHNSON CONTROLS - FRICK personnel or
other specially trained personnel. Drawings and a step-by-
step picture series showing how to perform a gear change
are available from JOHNSON CONTROLS - FRICK. A number
of special tools are needed to do a gear change and a
special tool KIT is available from JOHNSON CONTROLS -
FRICK that must be used.
WARNING
THIS SECTION MUST BE READ AND UNDERSTOOD BE-
FORE ATTEMPTING TO PERFORM ANY MAINTENANCE
OR SERVICE TO THE UNIT.
CAUTION
Cylinder assembly under high spring load. Consult
manual before disassembly. Improper disassembly may
cause injury due to spring tension release.
NORMAL MAINTENANCE OPERATIONS
When performing maintenance you must take several
precautions to ensure your safety:
1. IF UNIT IS RUNNING, PRESS [STOP] KEY.
2. STOP ENGINE AND LOCK OUT STARTER BEFORE
PERFORMING ANY MAINTENANCE.
3. WEAR PROPER SAFETY EQUIPMENT WHEN
COMPRESSOR UNIT IS OPENED TO ATMOSPHERE.
4. ENSURE ADEQUATE VENTILATION.
5. TAKE NECESSARY SAFETY PRECAUTIONS REQUIRED
FOR THE GAS BEING USED.
GENERAL MAINTENANCE
Proper maintenance is important in order to assure long and
trouble-free service from your screw compressor and
package. Some areas critical to good compressor operation
are:
1. Keep gas and oil clean and dry, avoid moisture
contamination. After servicing any portion of the
refrigeration system, evacuate to remove moisture before
returning to service. Water vapor condensing in the
compressor while running or more likely while shut down,
can cause rusting of critical components and reduce life.
2. Keep suction strainer clean. Check periodically,
particularly on new systems where welding slag or pipe
scale could find its way to the compressor suction. Excessive
dirt in the suction strainer could cause it to collapse,
dumping particles into the compressor.
3. Keep oil filters clean. If filters show increasing pressure
drop, indicating dirt or water, stop the compressor and
change filters. Running a compressor for long periods with
high filter pressure drop can starve the compressor for oil
and lead to premature bearing failure. Dual oil filters are
recommended so that the filters can be changed without
shutting down the package.
4. Avoid slugging compressor with liquids (oil). While screw
compressors are probably the most tolerant of any
compressor type available today about ingestion of some
liquid, they are not liquid pumps. Make certain a properly
sized suction accumulator is used to avoid dumping liquid
into compressor suction.
5. Protect the compressor during long periods of shutdown.
If the compressor will be sitting for long periods without
running it is advisable to evacuate to low pressure and
charge with dry nitrogen or oil. This is particularly true on
systems known to contain water vapor.
6. Preventive maintenance inspection is recommended any
time a compressor exhibits a noticeable change in vibration
level, noise or performance.
CHANGING OIL
WARNING
DO NOT MIX OILS of different brands, manufacturers,
or types. Mixing of oils may cause excessive oil foam-
ing, nuisance oil level cutouts, oil pressure loss, gas or
oil leakage and catastrophic compressor failure.
Shut down the unit when changing oil. At the same time all
oil filter cartridges must be changed and all
oil strainer
elements removed and cleaned. The procedure is as follows:
1. Stop the compressor unit.
2. Lock out the engine starter.
3. Close the suction and discharge service valves
4. Using appropriate equipment, lower the compressor
pressure to 0 psig.
5. Open the drain valve(s) and drain oil into a suitable
container.
6. Drain the oil filter(s) and the oil coolers.
7. Remove the old filter cartridges, and install new ones.
8. Remove, clean, and reinstall elements in the strainers.
9. Evacuate the unit.
10. Open the suction service valve and pressurize the unit
to system suction pressure. Close the suction valve and
leak test.
11. Add oil.
12. Open the suction and discharge service valves
13. Remove the lockout from the engine starter.
14. Start the unit
OIL PUMP
The oil pump is integral and directly driven by the
compressor drive shaft. There is no dynamic seal and the
end clearance is fixed. Service will normally not be needed
as long as the pump provides adequate pressure.
Maintenance