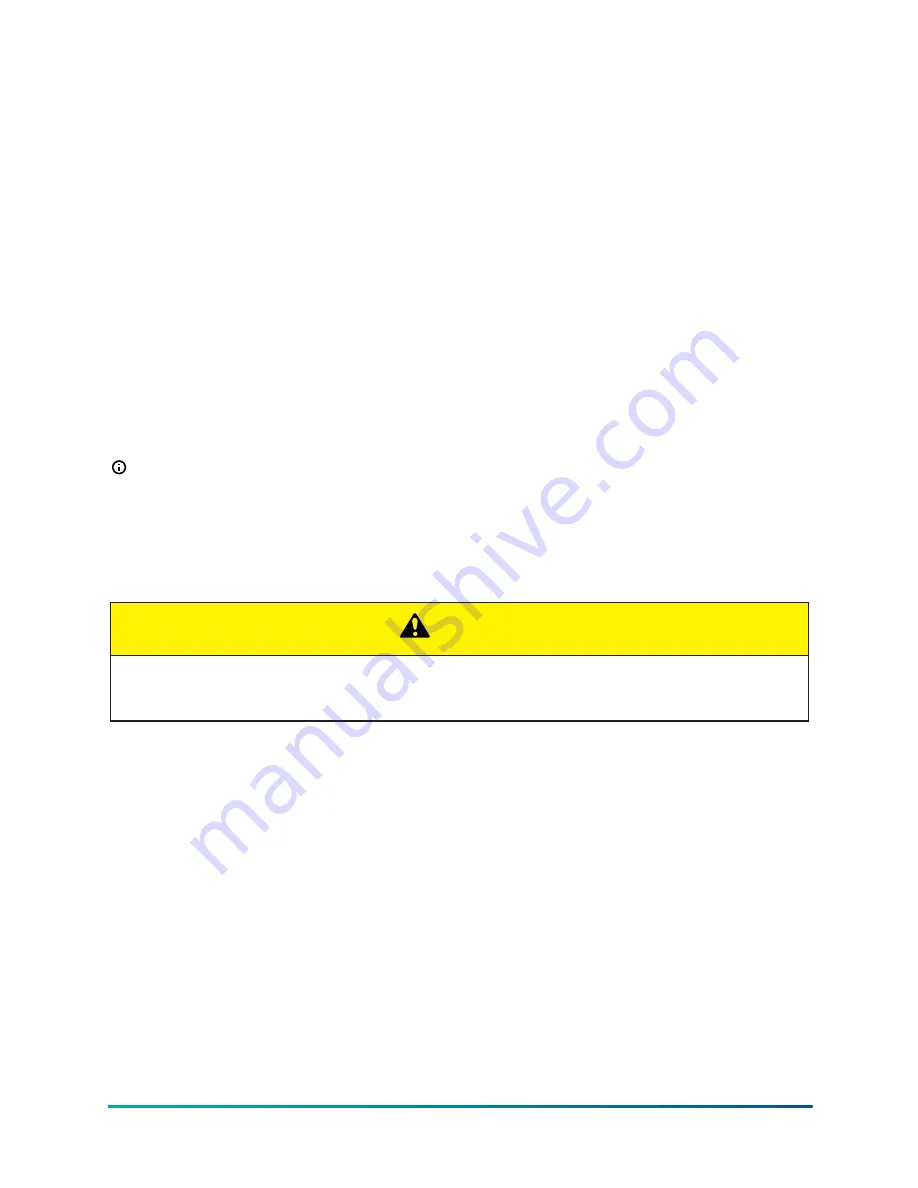
•
Carefully position the evaporator section atop the condensing section. Align all sides, the
evaporator motor wire routing hole, and the refrigerant line routing holes.
•
Install the securing brackets at all four corners, on the evaporator/condenser separation
joint.
•
For the 25-ton model, cut off spun copper ends on each refrigerant pipe in evaporator and
condenser. Units with optional Hot Gas Bypass will also require to have spun ends cut. Cut
pipe to appropriate length to fit on couplings. Ensure circuit 1 from condenser connects to
circuit 1 piping in evaporator; follow the same procedure for circuit 2. Do not cross circuits.
•
Braze copper couplings to refrigerant pipe while using a flow of nitrogen gas through the
refrigerant piping to minimize contamination to internal piping. Otherwise, fouling and
damage to unit may occur. Use the service gauge ports for this procedure to introduce
nitrogen flow. Once complete, pressure test with nitrogen (500 psig).
•
Evacuate each circuit to at least 350 microns. If gauge pressure rises above 500 microns in
one minute, evacuation is incomplete or the system has a leak.
•
Charge circuit(s) to the value indicated on the unit nameplate, or see
•
Install bushing/clamp into evaporator wiring routing hole, and pull wires through into
electrical control panel. Connect motor leads to load terminals on contactor/overload relay.
Note:
Ensure evaporator motor rotation is correct upon unit start-up. Switch any two wires at
contactor if blower rotation is not correct.
Water piping
All factory installed water piping terminates at the face of the unit and features a wrenchless
connection. Multi-condenser units feature manifolded single water in and out connections.
CAUTION
Water connection fittings are threaded copper. Use caution when tightening steel pipe into copper
fittings.
It is recommended that flexible connectors be provided on the water supply and return lines if
noise and vibration transmission could be a problem.
Installer should include shutoff/balancing valves to the water piping so that the unit can be
serviced without shutting down and draining the entire water supply circuit. Since units are piped
in parallel piping circuits, the shutoff valves may be used to equalize the pressure drop to each
branch for even condenser water distribution. A bibcock or a plugged tee fitting should be installed
between the shutoff valves and the unit in both the inlet and outlet pipes. These connections are to
provide for acid cleaning of the condenser, if this should become necessary.
Units can be factory supplied with water piping in either left-hand (typical, as shown in dimensional
drawings) or right-hand configuration.
Waterside economizer
Optional Waterside economizer can be ordered as an accessory from the factory. When entering
fluid temperatures are appropriate, unit will power off compressors and divert fluid to water coil
to minimize power consumption. The control setpoint for the economizing cycle is user-adjustable
(recommended operating setpoint is 55.0 °F). Equipped with water coil, internally mounted
compressor, and temperature staging control panel and a three-way diverting valve. Refer to
13
C-Series Vertical (CSV) Water-Cooled Self-Contained Units, B Generation, R-410A Installation, Operation, and
Maintenance Manual