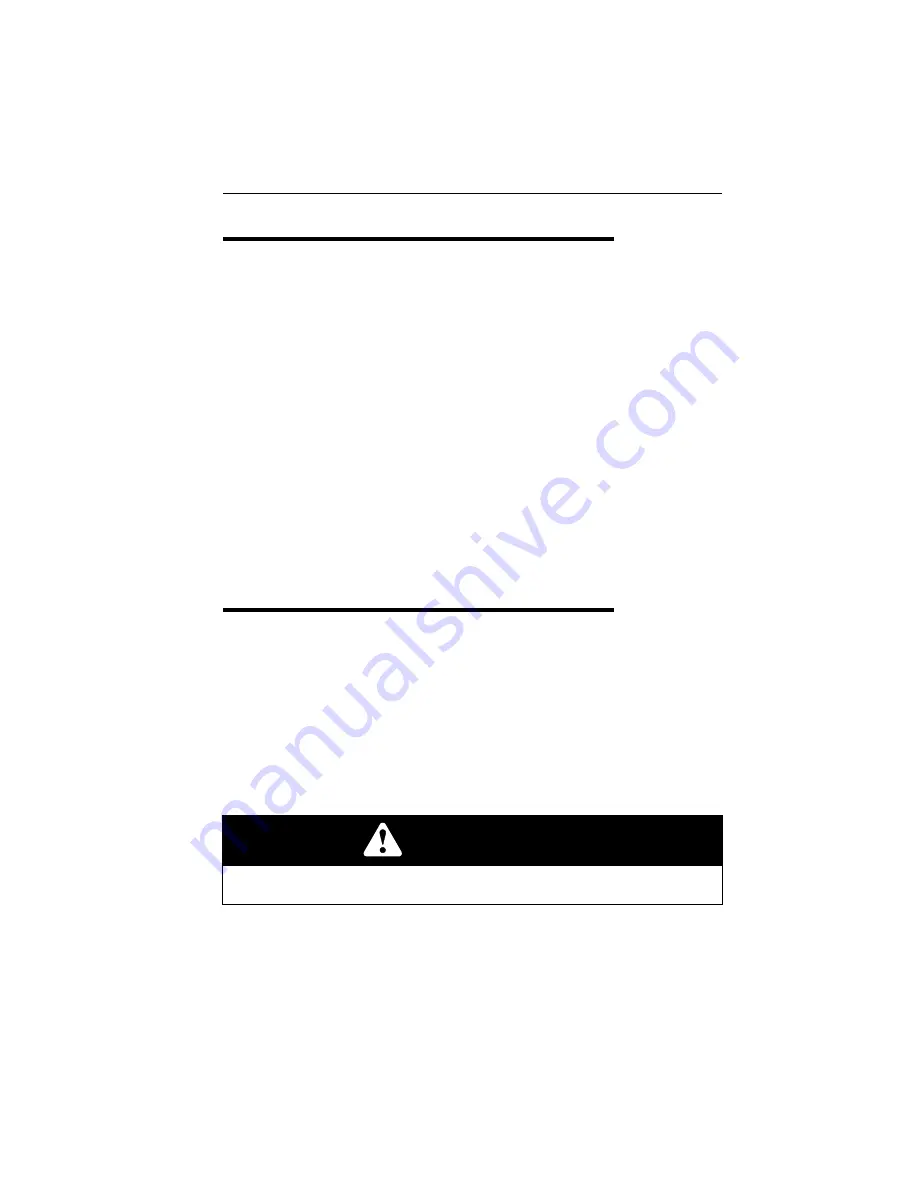
Section 5- Attachments
5-1
31211018
SECTION 5 - ATTACHMENTS
5.1
APPROVED ATTACHMENTS
To determine if an attachment is approved for use on specific telehandler you are using,
perform following prior to installation.
• The machine is authorized for use with original equipment manufactured (OEM)
supplied attachments or where explicit written authorization has been provided by
the manufacturer.
• The model on the capacity chart must match the model telehandler being used.
• Hydraulically powered attachments must only be used on machines equipped with
auxiliary hydraulics.
• Hydraulically powered attachments that require auxiliary electrics must only be used
on machines equipped with auxiliary hydraulics and electrics.
If any of the above conditions are not met, do not use attachment. Telehandler may not
be equipped with proper capacity chart or attachment may not be approved for the
model telehandler being used. Contact JLG or a local distributor for further information.
5.2
UNAPPROVED ATTACHMENTS
Do not use unapproved attachments for the following reasons:
• Range and capacity limitations for “will fit,” homemade, altered, or
other non-approved attachments cannot be established.
• An overextended or overloaded telehandler can tip over with little or no warning and
cause serious injury or death to the operator and/or those working nearby.
• The ability of a non-approved attachment to perform its intended function safely
cannot be assured.
WARNING
Use only approved attachments. Attachments which have not been approved for use
with your telehandler could cause machine damage or an accident.
Содержание Skytrak 6036
Страница 44: ...Section 3 Controls and Indicators 3 2 31211018 3 2 CONTROLS OH4980 9 2 1 10 11 7 6 4 3 8 5 12 13...
Страница 80: ...Section 4 Operation 4 14 31211018 This Page Intentionally Left Blank...
Страница 89: ...Section 5 Attachments 5 9 31211018 This Page Intentionally Left Blank...
Страница 134: ...Section 6 Emergency Procedures 6 4 31211018 This Page Intentionally Left Blank...
Страница 143: ...Section 7 Lubrication and Maintenance 7 9 31211018 8042 10042 O 5731 H 50 EVERY...
Страница 144: ...Section 7 Lubrication and Maintenance 7 10 31211018 10054 O 5711 H 50 EVERY...
Страница 145: ...Section 7 Lubrication and Maintenance 7 11 31211018 250 Hour Lubrication Schedule 6036 6042 O 1830 A EVERY 250 6042 ONLY...
Страница 147: ...Section 7 Lubrication and Maintenance 7 13 31211018 1000 Hour Lubrication Schedule OH4181 1000 EVERY...
Страница 166: ...Section 8 Additional Checks 8 4 31211018 This Page Intentionally Left Blank...
Страница 182: ...Index 4 31211018...
Страница 184: ...Inspection Maintenance and Repair Log Date Comments...
Страница 186: ......